浸出油溶剂残留量检测的重要性与技术要求
浸出油作为现代油脂工业中广泛应用的提取工艺,通过有机溶剂(如正己烷)从油料中高效提取油脂。然而,溶剂残留可能对人体健康造成潜在威胁,长期摄入微量残留溶剂可能引发神经系统损伤或慢性中毒。我国《GB 2716-2018 食品安全国家标准 植物油》明确规定,浸出油脂中溶剂残留量不得超过50mg/kg。因此,溶剂残留量的精准检测不仅是保障食品安全的重要屏障,更是油脂生产企业质量控制的关键环节。
核心检测项目与实施要点
1. 残留溶剂种类鉴定 通过气相色谱-质谱联用技术(GC-MS)对油脂中可能残留的正己烷、丙酮、异丙醇等溶剂进行定性分析,建立各溶剂的特征峰数据库,确保检测覆盖所有可能残留的挥发性有机物。
2. 定量检测方法验证 依据《GB 5009.262-2016 食品安全国家标准》要求,采用顶空进样气相色谱法进行定量分析。需验证方法的线性范围(0.5-100mg/kg)、检出限(≤0.1mg/kg)和加标回收率(85%-115%),确保检测数据可靠性。
3. 残留限值符合性判定 建立三重四级杆质谱的多反应监测模式(MRM),针对不同溶剂的特性离子对进行精准定量,结合标准曲线法计算结果,严格对照国家标准进行合规性判断。
质量控制关键环节
1. 样品前处理标准化 采用密闭式顶空瓶进行样品平衡,控制水浴温度(80±1℃)和平衡时间(40min),使用带聚四氟乙烯垫片的密封瓶盖防止挥发损失,确保检测重现性误差<5%。
2. 仪器状态监控 每日检测前需进行基线噪声测试(≤1%FS)、色谱柱效验证(理论塔板数≥5000)以及保留时间漂移检查(≤0.05min),建立完整的仪器使用日志和期间核查记录。
3. 数据完整性管理 采用实验室信息管理系统(LIMS)实现检测数据的自动采集、计算和存档,配备电子签名和审计追踪功能,确保检测报告的可追溯性符合 认证要求。
行业发展趋势与技术创新
随着分析技术的进步,快速检测设备正逐步推广。基于近红外光谱的在线监测系统可实现生产过程中溶剂残留的实时监控,检测时间缩短至5分钟内。同时,新型环保溶剂的开发推动检测方法持续更新,检测机构需定期参加能力验证,保持检测技术的前沿性。
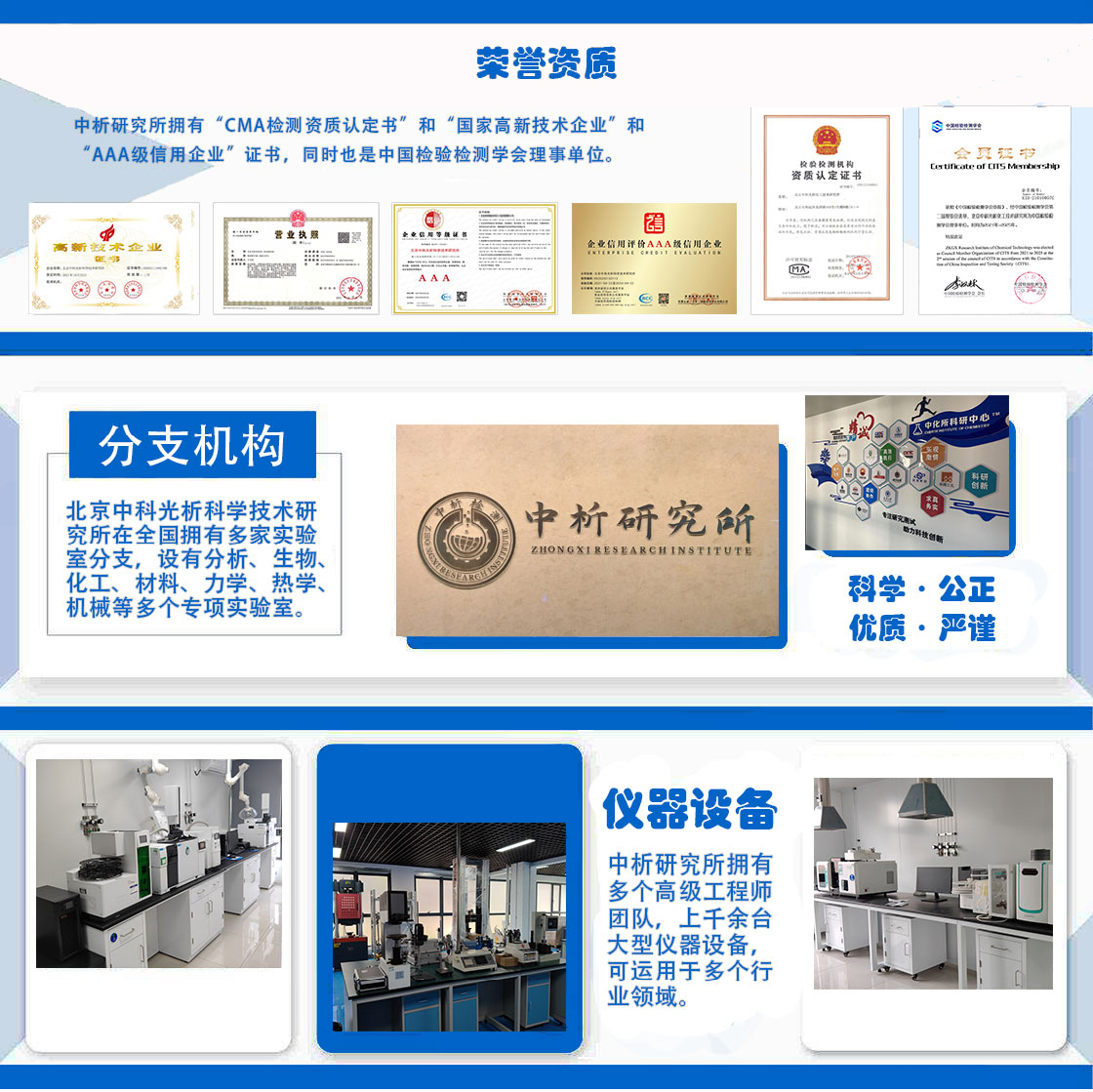
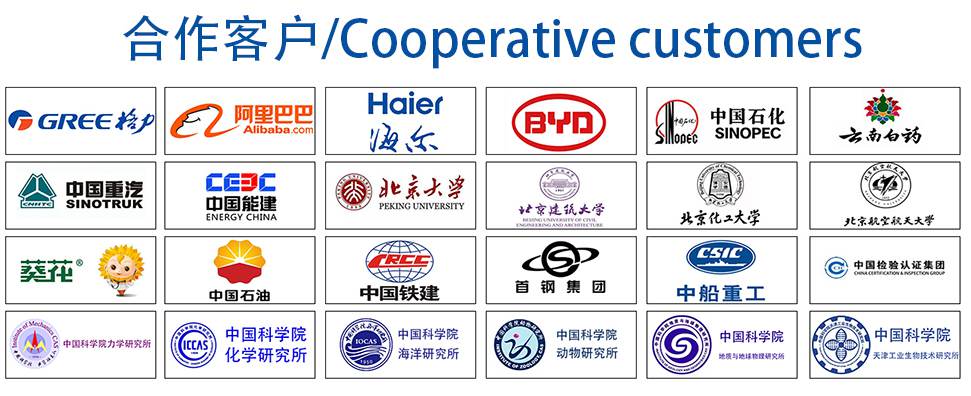