机械损伤检测:守护设备安全的核心环节
机械损伤检测是工业生产、设备维护和安全生产中至关重要的技术环节。随着现代制造业向高精度、高可靠性和智能化方向发展,机械部件在长期使用过程中可能出现的裂纹、磨损、变形等损伤问题,已成为威胁设备运行安全的关键隐患。通过系统化的检测项目,能够有效识别早期损伤,避免因故障引发的停机事故或安全事故,同时延长设备使用寿命,降低维护成本。本文将从检测技术原理、核心检测项目及行业应用三个维度展开分析。
一、常见机械损伤检测项目分类
1. 表面缺陷检测:通过目视检查、荧光渗透检测或电子显微镜分析,识别零件表面的划痕、凹坑、锈蚀等异常。其中工业内窥镜检测技术可深入复杂结构内部,实现非破坏性检查。
2. 裂纹深度测量:采用超声波探伤仪、涡流检测设备或X射线断层扫描技术,精确测定裂纹的走向和扩展程度。相控阵超声检测技术可实现三维成像,检测精度可达0.1mm级。
3. 材料性能退化评估:通过硬度测试(布氏/洛氏硬度计)、金相分析以及残余应力检测,判定金属材料是否发生疲劳损伤、晶粒变形等问题。
二、智能化检测技术突破
现代检测技术已突破传统人工检测的局限,形成多技术融合的检测体系:
1. 机器视觉系统:配备高分辨率工业相机和AI算法的视觉检测系统,可实现每分钟数百件产品的自动缺陷识别,检测速度较人工提升10倍以上。
2. 声发射监测技术:通过采集材料损伤时释放的弹性波信号,可实时监测压力容器、桥梁钢构等大型设备的动态损伤演变过程。
3. 数字孪生预测模型:结合传感器网络和仿真计算,构建设备全生命周期健康管理系统,预测潜在损伤位置及剩余使用寿命。
三、行业标准与质量管控
机械损伤检测需严格遵循行业规范:
1. 国际标准体系:包括ISO 9712(非破坏性检测人员资格认证)、ASTM E1444(磁粉检测规范)等,确保检测流程的规范性和结果可信度。
2. 数据化管理:采用PDCA循环模式,建立检测数据追溯系统,实现从原始数据采集、分析到改进措施的闭环管理。
3. 风险分级管控:根据损伤等级制定差异化的处理方案,对关键承力部件实施加倍抽样检测,确保高风险部位零缺陷。
四、典型应用场景解析
在风电设备领域,机组主轴轴承的微裂纹检测已成为运维重点。某企业采用太赫兹波成像技术,成功将主轴故障预警时间提前800小时。而在汽车制造行业,基于深度学习的焊点质量检测系统,使车身焊接缺陷率下降至0.02‰以下。
随着工业4.0时代的到来,机械损伤检测正朝着智能化、精准化、在线化的方向快速发展。构建多维度检测体系、培养专业检测人才、完善检测标准规范,将成为保障设备安全运行、推动制造产业升级的重要支撑。
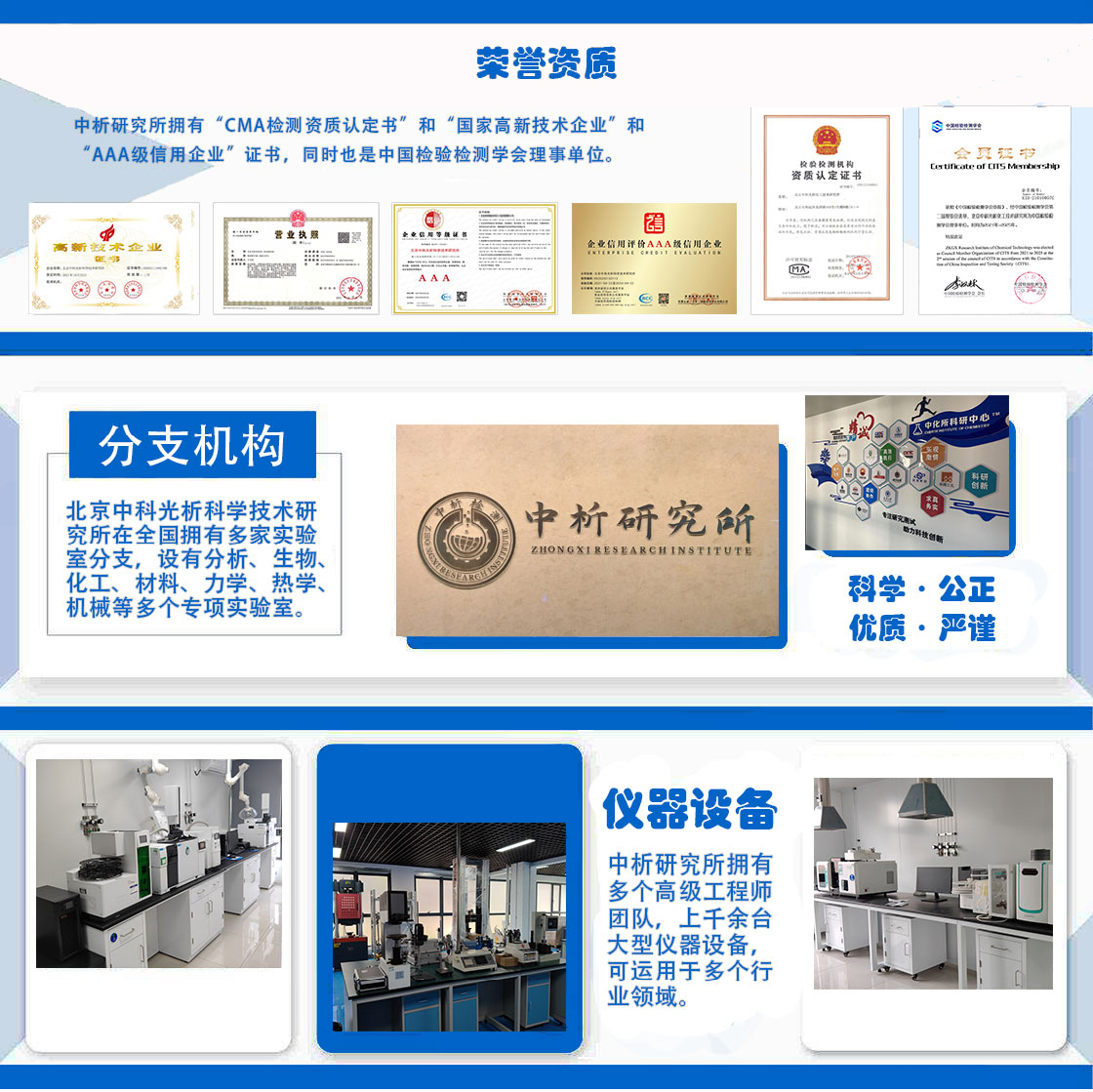
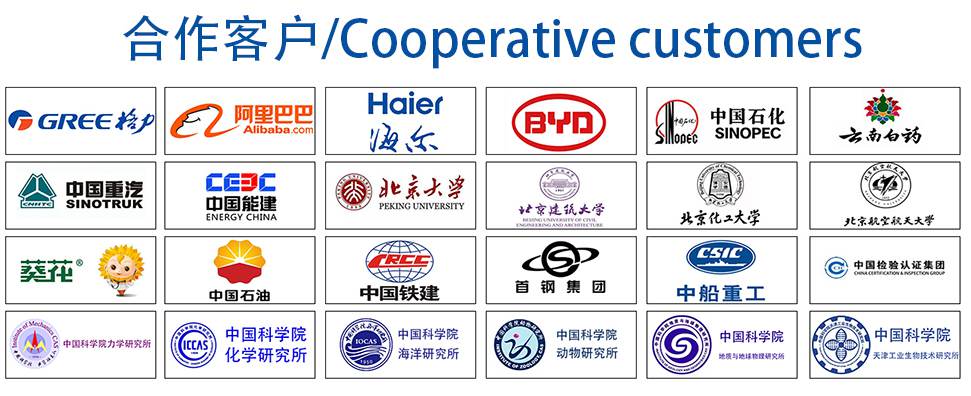