工业制造中的裂球检测技术解析
在精密机械制造、轴承生产及体育用品行业,裂球检测是保障产品质量的核心环节。作为金属球体(如轴承滚珠、高尔夫球芯等)质量控制的核心指标,细微的裂纹缺陷可能导致设备异常磨损、运动器械性能下降甚至安全事故。随着工业4.0时代的到来,现代裂球检测已从传统人工目检发展为融合光学识别、超声波探伤和智能算法的综合检测体系,检测精度可达微米级,每年可帮助企业减少数百万美元的质量损失。
核心检测项目与实施流程
完整的裂球检测系统包含五大关键模块:
1. 表面完整性检测
采用800万像素工业相机配合环形LED光源,通过多角度成像捕捉球体表面0.02mm以上的裂纹。数字图像处理系统运用边缘增强算法,能有效区分加工纹路与真实裂纹,检测速度可达1200件/分钟。
2. 内部缺陷超声检测
使用5MHz高频超声波探头,配合耦合剂实现能量传导。系统通过分析回波信号特征,可精确定位皮下2mm范围内的夹杂、气孔等缺陷,检测灵敏度达到φ0.4mm平底孔当量。
3. 几何尺寸测量
配备激光三维扫描仪,在球体360°自转过程中采集2000个测量点。系统自动计算直径偏差、圆度误差等参数,测量精度±0.001mm,符合ISO3290标准对G5级精密钢球的要求。
4. 材料性能测试
通过洛氏硬度计(HRC标尺)和能谱分析仪,检测材料硬度分布及成分偏差。针对特殊工况要求,可进行盐雾试验(ASTM B117标准)评估抗腐蚀性能。
5. 动态疲劳试验
在模拟工况的液压加载系统中,对样本施加周期性载荷(通常为额定载荷的120%)。通过振动传感器监测异常信号,结合Weibull分布模型预测产品寿命,试验周期可缩短至传统方法的1/3。
智能检测系统创新应用
前沿检测方案已集成深度学习算法,通过训练数万张缺陷样本建立的卷积神经网络模型,可使误检率降低至0.15%以下。配合六轴机械臂和RFID追溯系统,实现检测、分拣、数据归档的全流程自动化,良品率提升可达23%。
随着机器视觉和工业物联网技术的深度融合,现代裂球检测正朝着在线实时监测、预测性质量管控的方向发展。生产企业通过部署智能检测系统,不仅能提升产品可靠性,更可优化生产工艺,构建完整的质量大数据体系,在高端制造领域形成核心竞争优势。
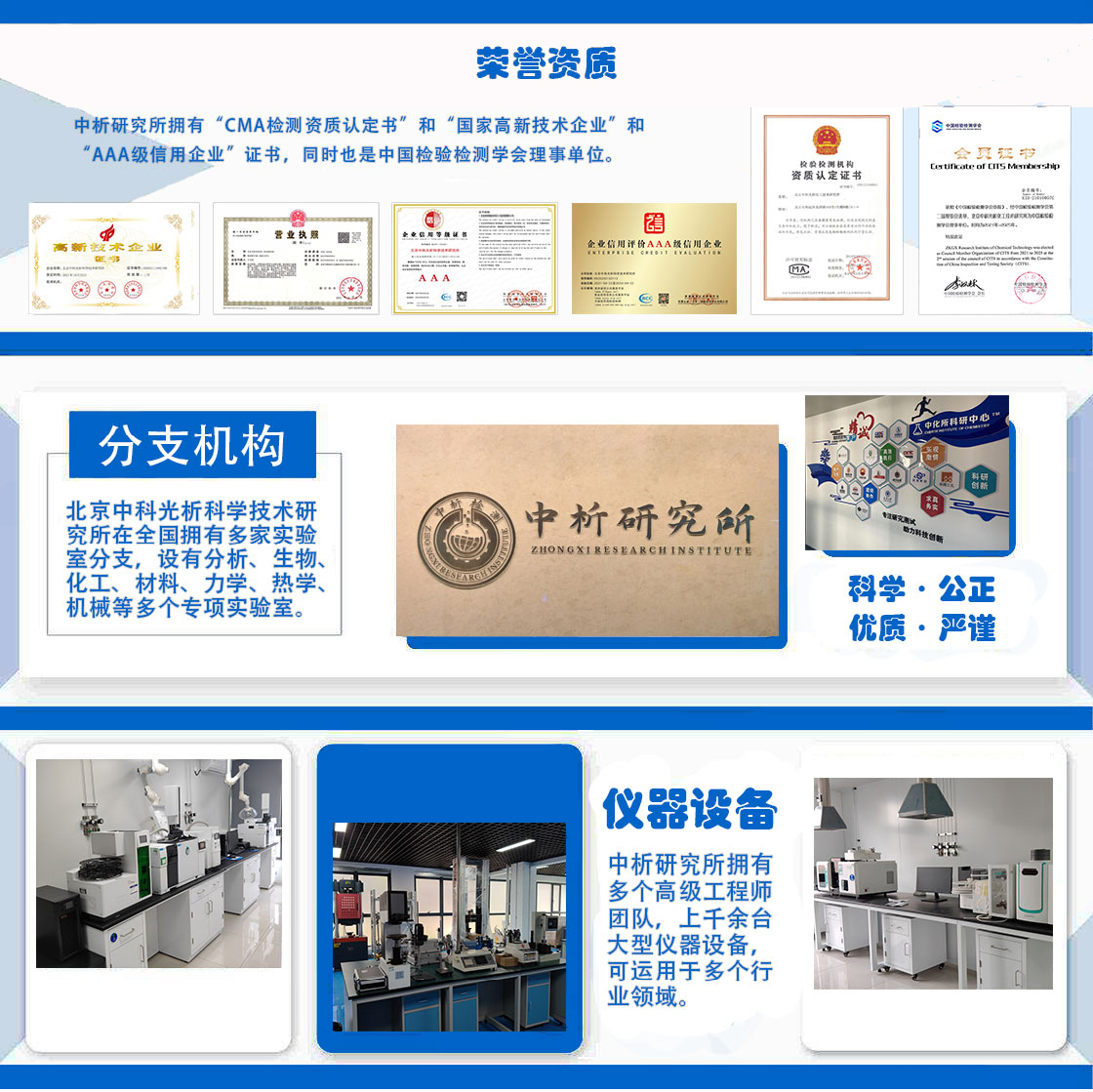
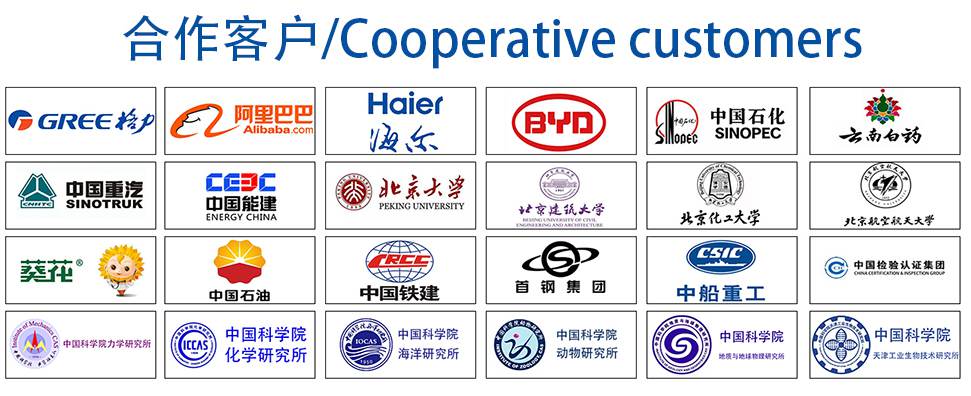