电动执行机构检测的重要性与应用范围
电动执行机构是工业自动化控制系统的核心部件,广泛应用于阀门、风门、闸门等设备的驱动与控制。其性能直接影响生产流程的稳定性、安全性及能源效率。随着工业4.0和智能制造的推进,电动执行机构的检测需求日益增长,涵盖机械性能、电气特性、环境适应性和智能功能等多个维度。通过系统化的检测项目,可有效验证其扭矩输出精度、响应速度、耐久性及抗干扰能力,确保设备在高温、潮湿、振动等复杂工况下的可靠性。
一、基础功能检测
1. 扭矩与推力测试:通过模拟负载条件,检测执行机构在额定电压下的最大输出扭矩和推力,验证是否满足设计参数。 2. 行程精度校准:使用高精度编码器或激光测距仪,测量开度位置的重复定位精度,误差需控制在±0.5%以内。 3. 响应时间分析:记录从控制信号输入到机械动作完成的时间延迟,评估动态响应是否符合工艺要求。
二、电气安全与稳定性检测
1. 绝缘电阻测试:采用500V兆欧表测量带电部件与外壳间的绝缘电阻,标准值需≥100MΩ。 2. 过载保护验证:模拟超负荷运行场景,检查电流保护装置是否及时切断电源并发出报警信号。 3. EMC抗干扰测试:在电磁干扰环境下评估执行机构的信号稳定性,确保其符合IEC 61000-4系列标准。
三、环境适应性评估
1. 温湿度循环试验:在-40℃~85℃温度范围和95%湿度条件下进行48小时循环测试,观察密封性与材料形变。 2. 防护等级验证:依据IP67/IP68标准进行喷淋、浸水测试,确认防护结构有效性。 3. 振动与冲击测试:模拟运输及运行中的机械振动(频率5-200Hz),检测紧固件松动率和内部元件损伤情况。
四、智能功能专项检测
1. 通讯协议兼容性:测试Modbus、Profibus等工业总线接口的数据传输稳定性与实时性。 2. 故障自诊断能力:模拟电源中断、电机堵转等异常场景,验证故障代码生成与远程报警功能。 3. 能耗监测精度:通过电能质量分析仪记录运行功耗,评估节能模式下的效率优化效果。
五、寿命与可靠性验证
1. 机械寿命测试:连续进行10万次启停循环,统计齿轮磨损率与传动效率衰减值。 2. 电气元件耐久性:对控制板、继电器等关键部件进行加速老化试验,预测MTBF(平均无故障时间)。 3. 润滑系统评估:在长期运行后检测润滑脂的粘度变化与污染度,优化维护周期建议。
结语
电动执行机构的检测需结合行业标准(如GB/T 24923-2010)与具体工况制定方案,通过多维度测试数据建立设备健康档案。定期检测不仅能预防突发故障,还可为智能预测性维护提供数据支持,最终实现生产系统的高效、安全运行。
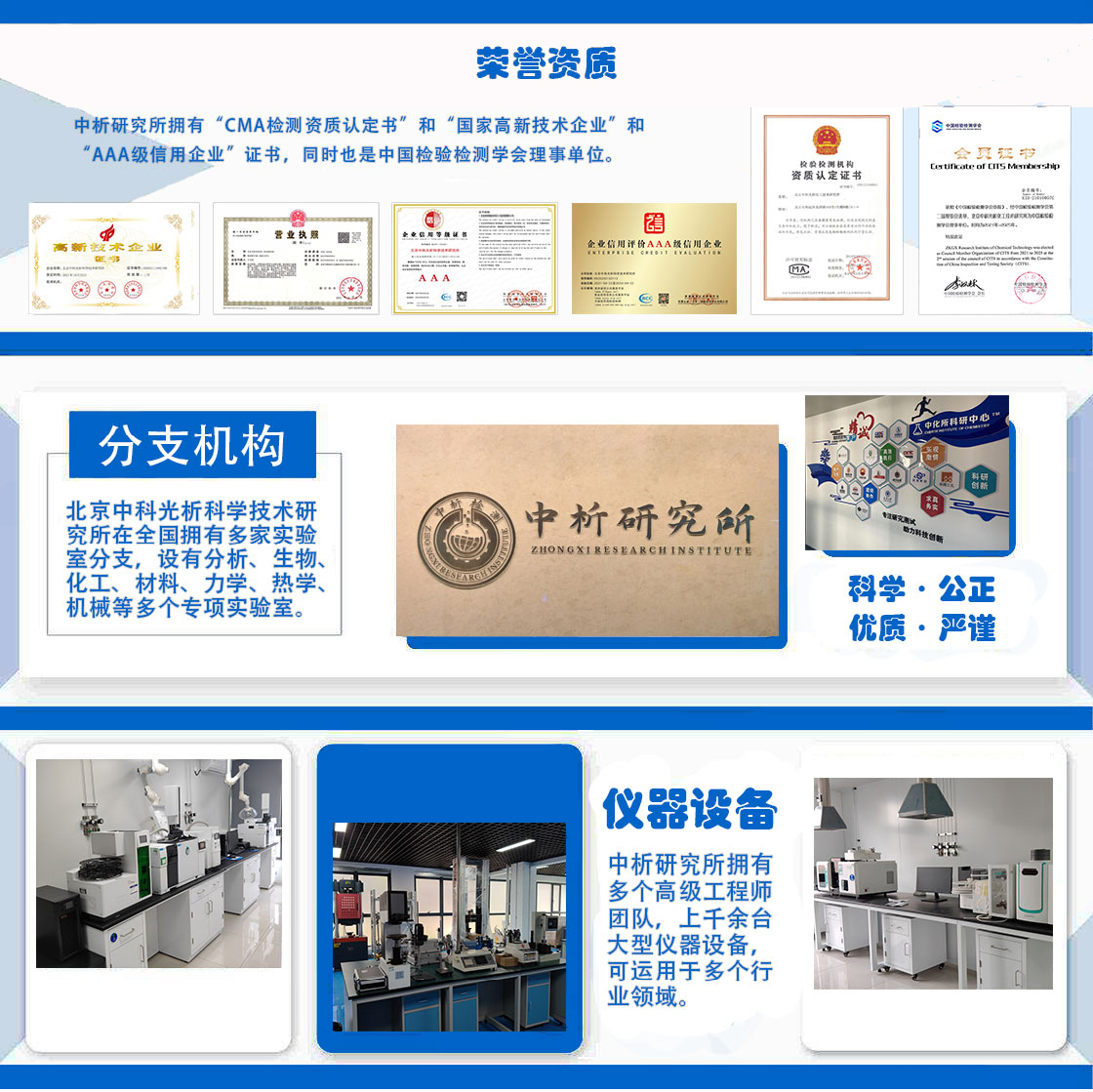
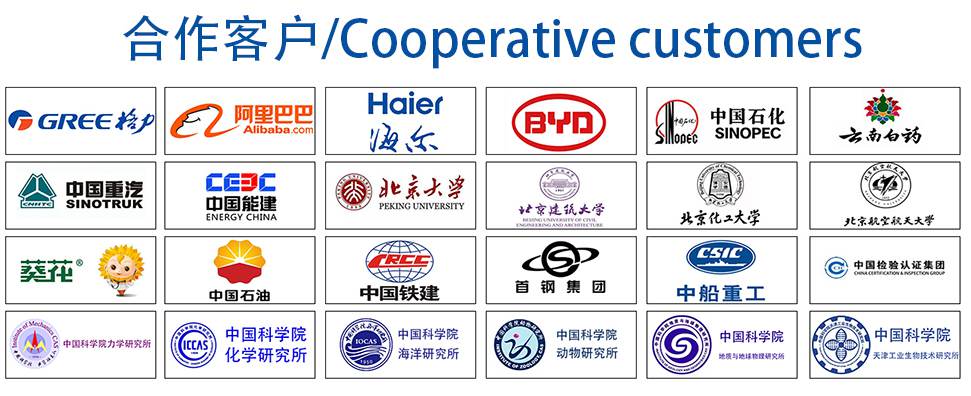