压力测试连接器检测:确保可靠性的关键环节
在工业制造、航空航天、汽车电子及通信设备领域,连接器作为信号与能量的传输核心部件,其可靠性直接影响整个系统的稳定性。压力测试连接器检测通过模拟极端工况下的物理和电气性能变化,评估连接器在长期使用中承受机械应力、环境冲击和负载波动时的耐久性。该检测项目覆盖插拔寿命、温湿度循环、振动冲击等20余项关键指标,是验证产品设计合理性、材料选择有效性和生产工艺严谨性的重要手段。
核心检测项目解析
1. 机械应力测试
采用伺服驱动装置执行插拔循环测试(5000-10000次),监测: - 插拔力衰减幅度(标准要求≤15%初始值) - 接触电阻变化率(IEC 60512-2-1规定≤3mΩ) - 锁扣机构完整性 实验数据将揭示镀层磨损、弹性元件疲劳等潜在失效模式。
2. 环境适应性测试
依据MIL-STD-1344标准构建复合环境仓,进行: - 温度冲击测试(-55℃↔125℃, 5次循环) - 湿热老化测试(85℃/85%RH持续500小时) - 盐雾腐蚀测试(5%NaCl溶液喷雾96小时) 通过显微观察接触面腐蚀程度和绝缘材料形变量,评估环境防护等级是否符合IP67/IP69K要求。
3. 动态负载测试
搭建高压大电流测试平台(最高1000V/200A),模拟: - 脉冲电流冲击(100A脉冲宽度1ms) - 持续过载测试(120%额定电流连续工作) - 接触阻抗温升监测(UL 1977要求ΔT≤30K) 结合红外热像仪记录温度分布,验证载流部件的热稳定性设计。
4. 振动与冲击测试
依据GJB 360B-2009标准进行: - 随机振动测试(10-2000Hz,40g RMS) - 机械冲击测试(半正弦波3000g/0.3ms) - 共振点扫描分析 采用激光位移传感器监测接插件微动磨损,确保航空、车载等严苛场景下的连接可靠性。
检测结果判定体系
建立四维评估模型:
1. 机械性能保持率 ≥85%
2. 电气特性偏差 ≤10%标称值
3. 材料形变率 ≤3%
4. 防护等级维持度 100%
同时要求零功能性失效(接触不良、绝缘击穿等)。测试数据需通过威布尔分布分析推算MTBF值,为可靠性设计提供量化依据。
常见问题与改进方向
典型失效案例显示,78%的连接器故障源于:
- 镀层厚度不足(建议金层≥0.8μm)
- 塑料壳体结晶度偏低(需优化注塑参数)
- 接触件应力松弛(推荐铍铜合金材质)
通过DOE实验设计优化插孔弹片结构,可使插拔寿命提升200%以上。
(注:具体测试参数需根据GB/T 5095、EIA-364等标准及产品规格调整)
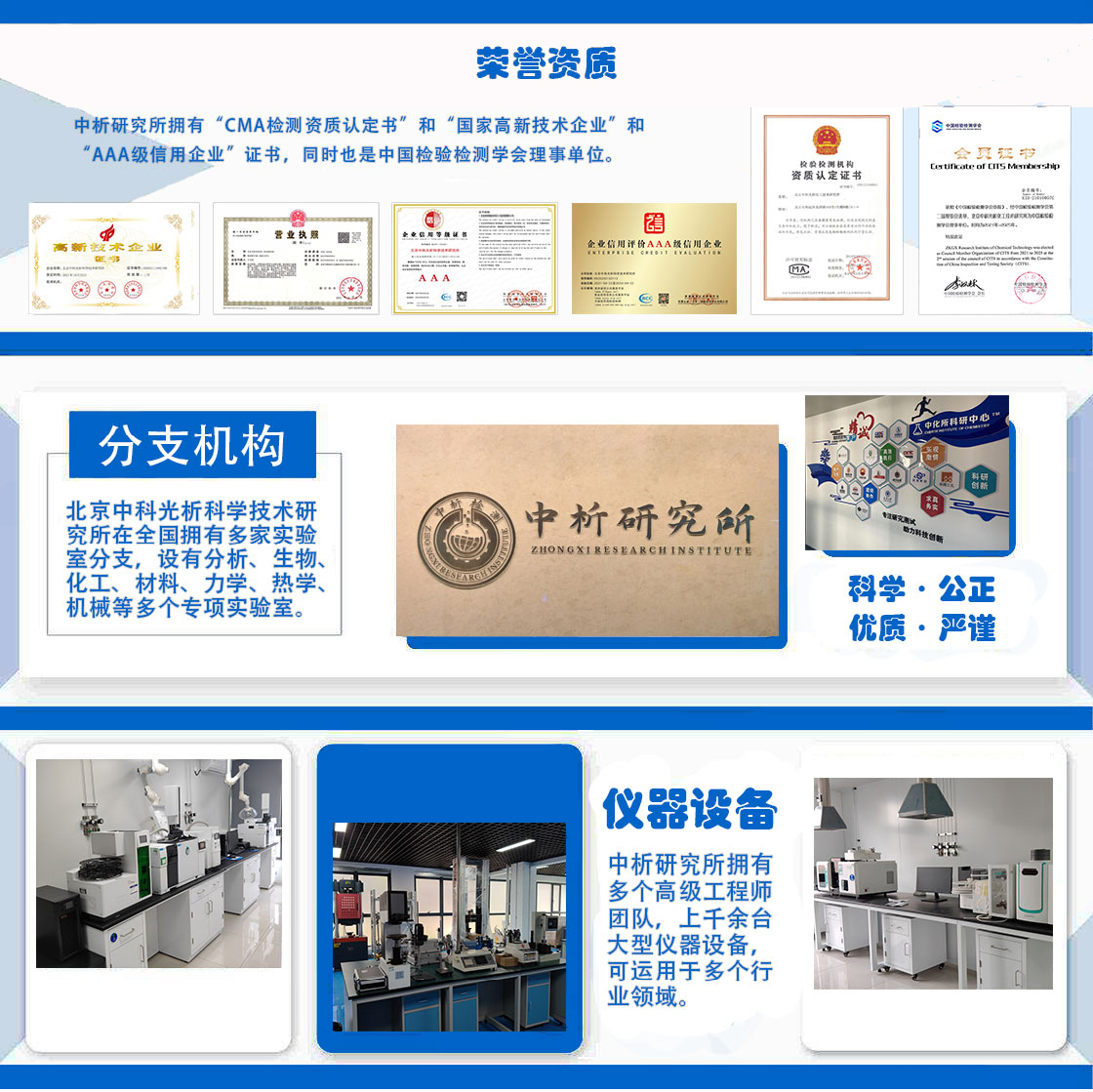
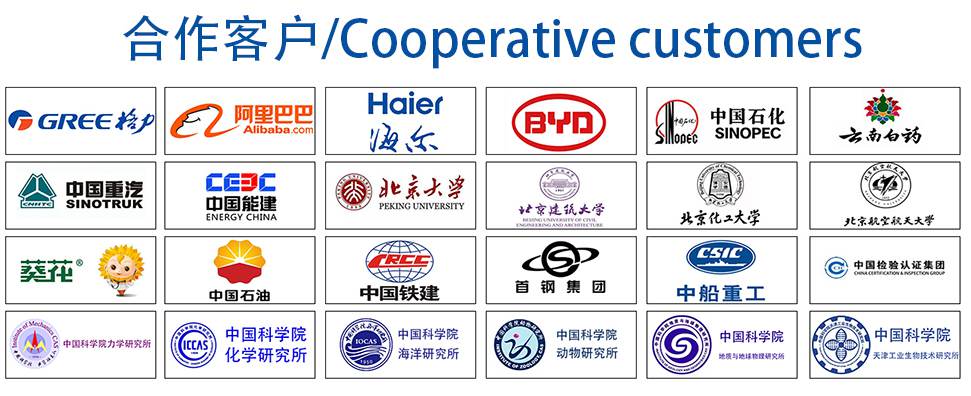