液压软管总成检测的重要性
液压软管总成作为液压系统中传递动力的关键部件,广泛应用于工程机械、航空航天、船舶制造及工业设备等领域。其性能和可靠性直接关系到整个系统的安全性和运行效率。由于液压软管总成长期承受高压、高温、脉冲冲击及外部环境侵蚀,一旦发生泄漏或破裂,可能导致设备停机、能源浪费甚至安全事故。因此,定期对液压软管总成进行系统性检测,是保障设备稳定运行、延长使用寿命的核心手段。
检测工作需依据相关行业标准(如ISO 18752、SAE J517等)进行,覆盖外观检查、耐压性能、脉冲寿命、爆破强度等多项指标,并结合实际工况定制检测方案。通过科学严谨的检测流程,能够及时发现材料老化、接头松动、编织层损伤等问题,为维修或更换决策提供数据支持。
主要检测项目及要求
1. 外观检测
通过目视或放大设备检查软管表面是否存在裂纹、鼓包、磨损、腐蚀或接头变形。重点关注接头与软管的连接处,确保无松动、锈蚀或渗漏痕迹。同时核对标识信息(如压力等级、生产日期)是否清晰可辨。
2. 尺寸测量
使用卡尺、投影仪等工具精确测量软管内外径、长度及接头螺纹参数,确保符合设计图纸和安装要求。公差范围需参考GB/T 3683等标准,避免因尺寸偏差导致安装错位或应力集中。
3. 耐压测试
在实验室模拟工况压力(通常为额定压力的1.5-2倍),保持2-5分钟,观察是否发生泄漏或异常膨胀。此测试可验证软管总成在静态高压下的密封性和结构完整性,是判断其安全裕度的关键指标。
4. 脉冲测试
通过高频压力循环装置模拟实际工作时的压力波动(频率通常为0.5-1.5Hz),记录软管总成在达到规定脉冲次数(如20万次)后的状态。测试后需复测耐压性能,评估其抗疲劳能力是否符合ISO 6803等标准要求。
5. 爆破压力测试
逐步加压直至软管总成破裂,记录最大承受压力值。该测试旨在验证极限承载能力,要求实际爆破压力不得低于额定爆破压力(通常为工作压力的4倍),确保极端工况下的安全性。
6. 弯曲性能测试
将软管按标准半径弯曲后加压,检查其是否因形变导致泄漏或结构损伤。对于频繁移动的设备(如挖掘机臂架软管),还需模拟动态弯曲场景,评估长期使用后的抗弯折能力。
7. 泄漏检测
采用气压法或氦质谱检漏仪,在特定压力下检测微渗漏情况。高精度检测可发现0.1mL/min以下的渗漏量,适用于对密封性要求严苛的航空航天液压系统。
8. 材料分析
通过光谱分析、拉伸试验等手段检测橡胶层老化程度、增强层钢丝抗拉强度及接头金属成分。结合热重分析(TGA)评估材料耐温性能,预防因热降解导致的失效风险。
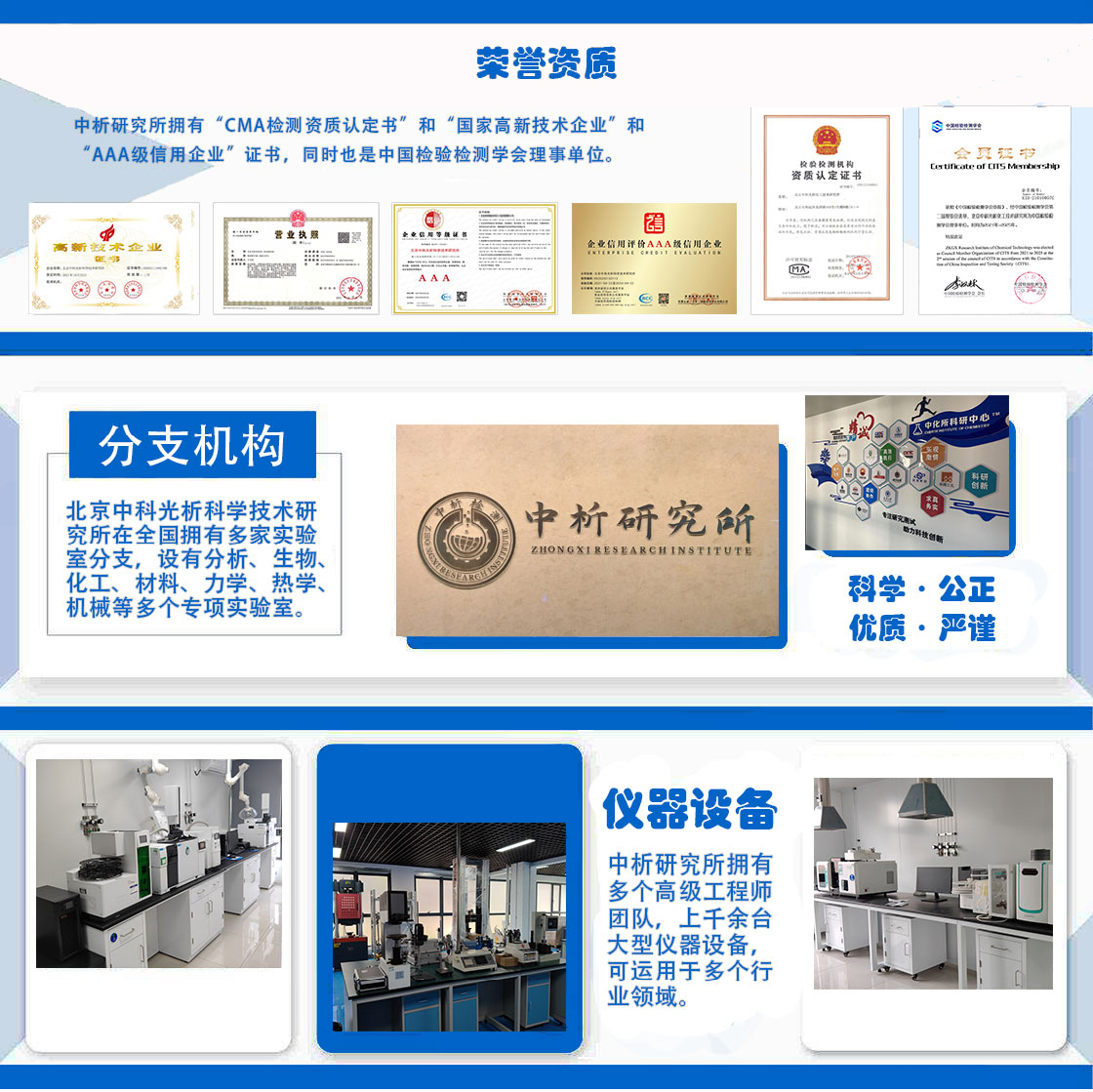
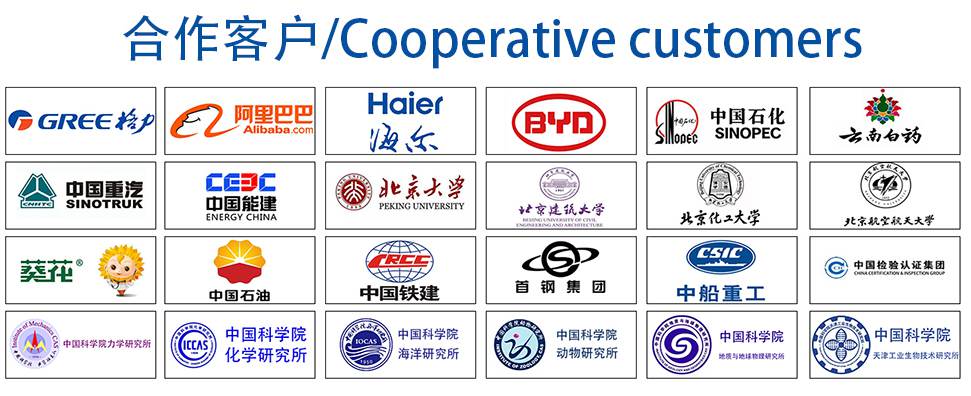