紧急切断阀作为工业管道系统中的重要安全装置,承担着在突发工况下快速切断介质流动、防止事故扩大的关键作用。它广泛应用于石油化工、天然气输送、危化品储运等高危领域,其性能可靠性直接关系到生产安全与环境保护。由于长期处于复杂工况环境中,阀门可能出现密封失效、动作迟滞、部件老化等问题,因此定期开展专业化的紧急切断阀检测是保障其应急功能的核心手段。
一、密封性能测试
通过注入额定压力介质并保持规定时间,检测阀门关闭后的泄漏量是否符合GB/T 24918标准要求。重点检查阀座与阀瓣接触面的密封完整性,使用气泡检测法或流量计量化泄漏等级,确保在最大工作压力下达到零泄漏标准。
二、动作响应时间检测
使用高精度计时装置记录从触发信号发出到阀门完全关闭的全程耗时,要求气动型阀门响应时间≤3秒,液压型≤5秒。测试需在不同压力工况下重复三次,验证执行机构的灵敏度与信号传输系统的稳定性。
三、外观与结构检查
采用目视检测与超声波测厚仪相结合的方式,检查阀体是否存在裂纹、腐蚀减薄现象,测量关键部位壁厚变化率。同时对传动部件进行拆解检查,评估弹簧疲劳度、密封件硬化程度等隐患,确保结构完整性。
四、材料性能验证
通过光谱分析确认阀体材质符合设计规范,对暴露在腐蚀介质中的部件进行硬度测试和金相检测。重点评估应力集中区域的材料延展性,防止因材料劣化导致的突发性断裂风险。
五、控制系统联动测试
模拟火灾、压力骤升等紧急信号,验证切断阀与DCS系统、ESD装置的协同响应能力。测试包括有线/无线信号传输、备用电源切换、手动优先级别等20余项功能指标,确保多级联锁保护有效。
六、重复动作可靠性试验
在额定工况下连续进行50次开闭循环测试,记录每次动作参数曲线。分析密封面磨损趋势、执行机构出力衰减情况,确认阀门在频繁动作后仍能保持规定的性能余量。
七、耐压强度试验
按照API 6D标准执行1.5倍公称压力的静态保压试验,持续时间不少于10分钟。使用应变片监测阀体变形量,要求残余变形率≤0.05%,验证阀门在超压工况下的结构安全性。
专业检测机构需配备压力校准系统、高速数据采集仪、非破坏检测设备等专业工具,并严格遵循TSG D7002等特种设备检验规范。建议企业建立年度检测制度,结合在线监测数据动态调整维保周期,构建全生命周期的安全管理体系。
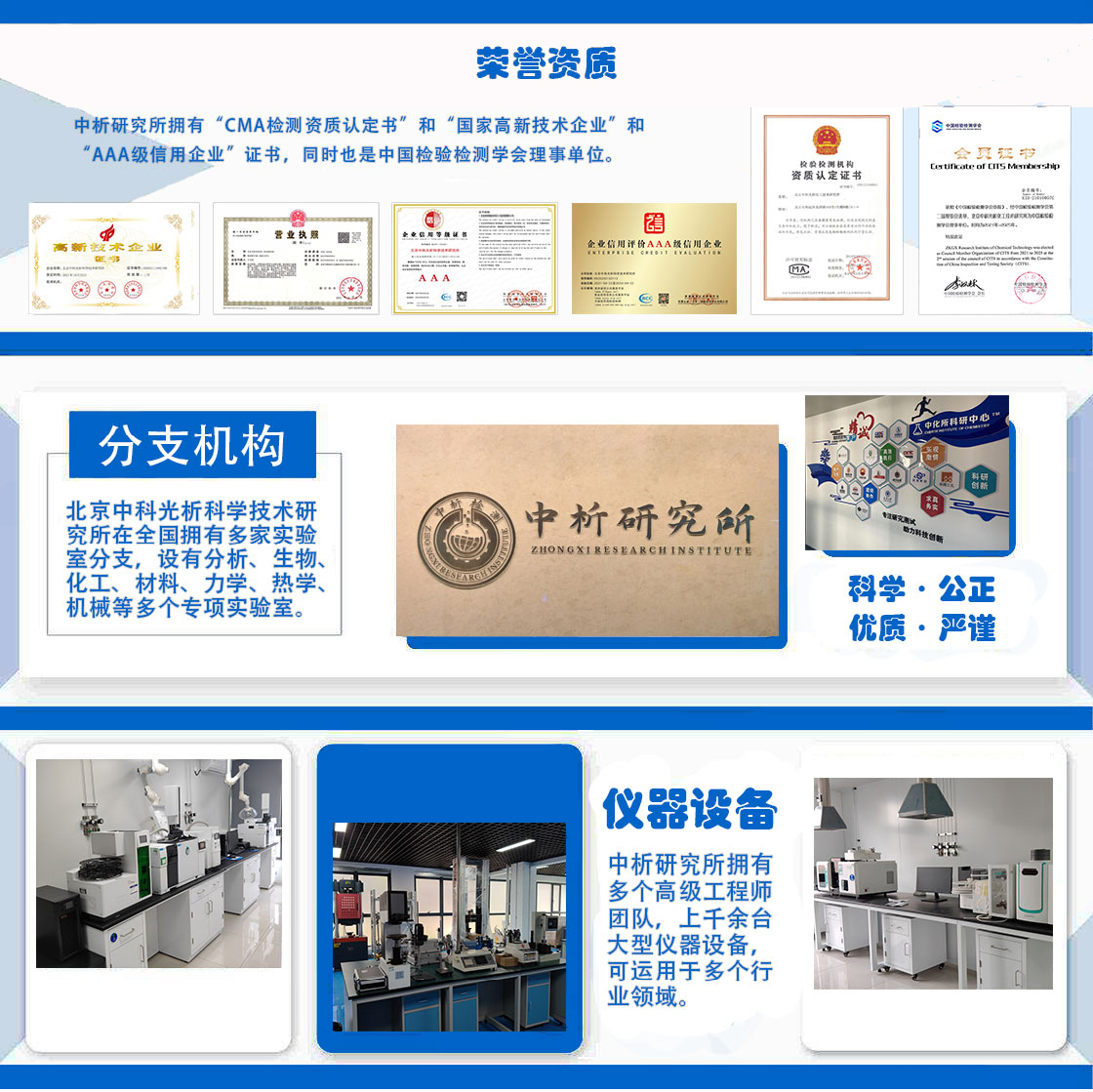
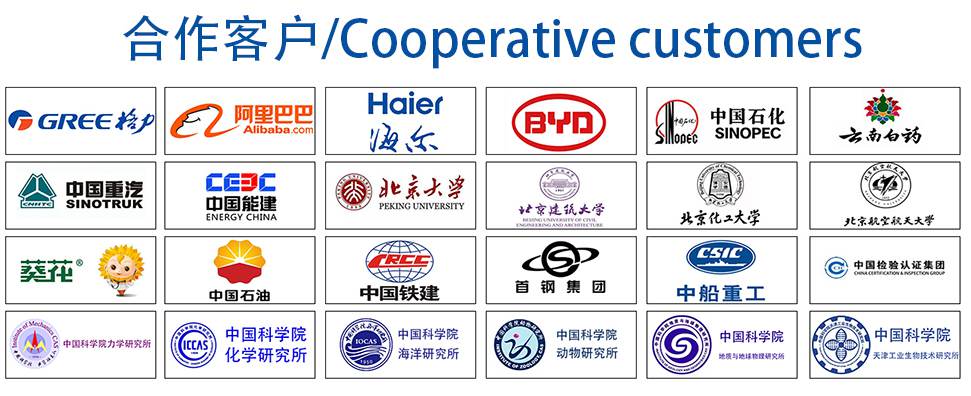