电动汽车用永磁同步驱动电机系统检测的核心意义
随着新能源汽车产业的快速发展,永磁同步驱动电机凭借其高功率密度、高效率及宽调速范围等优势,已成为电动汽车动力系统的核心部件。为确保其在复杂工况下的安全性、可靠性和耐久性,针对永磁同步驱动电机系统的精细化检测已成为行业刚需。检测工作不仅涉及驱动电机的本体性能评估,还需对控制系统、冷却系统及能量转换效率等关键环节进行全面验证。通过科学规范的检测流程,可有效预防高速运转中的退磁风险,优化电磁兼容性能,同时为整车的动力性、经济性提供技术保障。
效率特性检测
通过能量回馈法或直接测量法,在不同转速-转矩工况下精确测定系统效率MAP图。重点检测额定功率点的综合效率是否达到GB/T 18488-2015标准要求,同时验证低转速大扭矩段的效率衰减特性。使用高精度功率分析仪实时采集输入/输出功率数据,建立效率-转速-转矩三维曲面模型。
温升性能检测
在模拟极端工况的环境舱内进行连续加载试验,采用红外热成像仪与嵌埋式温度传感器相结合的方式,实时监测定子绕组、永磁体及轴承等关键部位温升曲线。依据ISO 6469-3:2018标准要求,验证冷却系统效能及材料耐温等级,确保高温环境下不发生不可逆退磁现象。
电磁兼容性(EMC)检测
按照CISPR 25:2016标准构建电磁暗室测试环境,通过传导发射、辐射发射及抗扰度测试三阶段验证。特别关注PWM逆变器产生的高频谐波对车载电子设备的干扰强度,采用LISN网络和磁场探头捕捉30MHz-1GHz频段的EMI特征,确保系统满足Class 3级电磁兼容要求。
振动与噪声检测
基于GB/T 28046.3-2019标准建立多轴振动测试平台,在0-500Hz频段内分析电磁激振力与机械振动的耦合特性。使用声学照相机进行NVH性能评估,重点检测48阶次电磁噪声和轴承异响,通过阶次跟踪技术分离结构共振与电磁噪声成分,优化转子斜极设计和定子绕组分布。
耐久性试验
构建包含城市工况、高速工况及爬坡工况的复合载荷谱,在温变交变环境仓内进行2000小时加速寿命测试。监测效率衰减率、振动量级增幅及绝缘电阻变化等关键指标,采用威布尔分布模型预测B10寿命值,确保系统满足15万公里整车质保要求。
绝缘性能检测
使用5kV耐压测试仪进行绕组对机壳的绝缘强度验证,通过极化指数(PI)和介质损耗因数(tanδ)测试评估绝缘材料老化状态。依据IEC 60034-18-41标准进行局部放电检测,设置0.5pC检测灵敏度,确保高压系统在潮湿、盐雾等严苛环境下的绝缘可靠性。
控制精度验证
搭建dSPACE快速控制原型平台,通过转矩阶跃响应测试评估电流环带宽。采用MTS测功机系统验证转速控制精度,要求稳态转速误差≤±1rpm,转矩动态响应时间<5ms。通过FOC算法参数优化,确保弱磁扩速阶段的转矩平稳性满足ISO 17408:2020要求。
结语
完善的永磁同步驱动电机系统检测体系是保障电动汽车安全运行的技术基石。随着智能网联技术的演进,检测项目正逐步向云端数据监测、故障预测等方向延伸。未来检测技术将深度融合数字孪生、AI诊断等创新手段,为新能源汽车产业的可持续发展提供更强技术支撑。
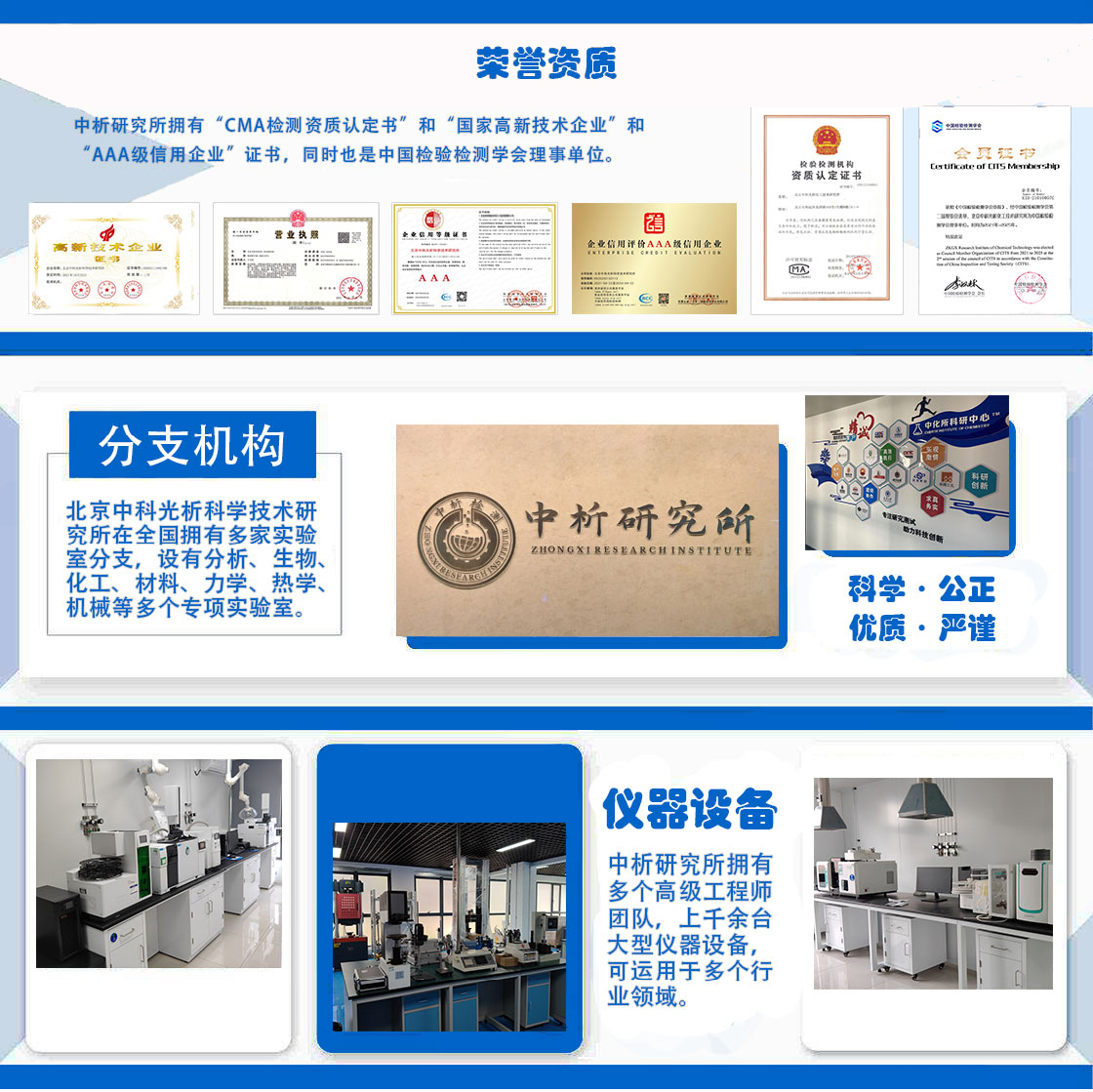
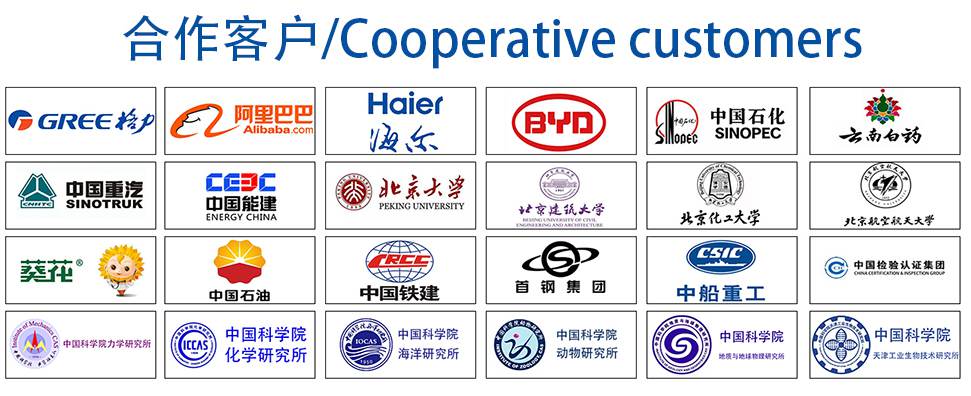