石油钻机和修井机检测的重要性与核心内容
石油钻机和修井机作为油气田勘探开发的核心装备,其安全性与可靠性直接关系作业效率、人员安全及环境保护。随着油气资源开发向深井、超深井及复杂地质条件区域延伸,设备长期处于高强度、高负荷运行状态,潜在机械疲劳、部件磨损、控制系统老化等问题日益突出。因此,通过科学规范的检测手段对钻机和修井机进行全面“体检”,成为预防重大事故、延长设备寿命、保障生产连续性的必要措施。
主要检测项目及技术要求
1. 结构安全检测
重点检查井架、底座、游车等承重部件的变形、裂纹及腐蚀情况,采用超声波探伤、磁粉检测等技术评估钢材完整性。井架垂直度偏差需控制在1‰以内,关键焊接部位需进行100%无损检测,确保其抗拉强度满足API 4F标准要求。
2. 动力及传动系统检测
针对柴油发动机、变速箱、绞车刹车系统进行性能测试:包括输出功率、扭矩传递效率、制动响应时间等参数。液压系统需检测压力波动、油液污染度(NAS 8级以下),传动链条磨损量不得超过原尺寸的5%。
3. 井控装置检测
防喷器组(BOP)须进行密封试验,环形防喷器在额定压力下保压30分钟无泄漏,闸板防喷器开关动作时间应≤45秒。节流压井管汇需验证耐压等级,测试压力为额定值的1.5倍。
4. 作业参数监测系统校验
校验指重表、扭矩仪、泵压表等传感器精度,误差需控制在±2%FS以内。数据采集系统应实现钻压、转速、排量等参数的实时监控,并具备异常值自动报警功能。
5. 环境适应性检测
极端气候环境下需验证设备运行稳定性:-40℃低温启动试验、抗风载能力(阵风12级)、防爆区域电气设备Ex认证有效性核查。海洋平台设备还需通过盐雾腐蚀试验(ISO 9227标准)。
6. 维护保养合规性检查
核查设备维护记录是否完整,包括润滑油更换周期、关键部件寿命管理、易损件库存情况。重点检查钢丝绳断丝率(每捻距内≤6%)、刹车块剩余厚度(不低于原厚度1/3)等指标。
检测周期与标准依据
常规检测应每半年开展一次,大修后或重大工况变化后需增加专项检测。主要依据API Spec 7K(钻井设备规范)、API RP 54(修井作业安全规程)及SY/T 5532(石油钻机现场安装与检验)等行业标准,结合数字化检测技术实现全生命周期管理。
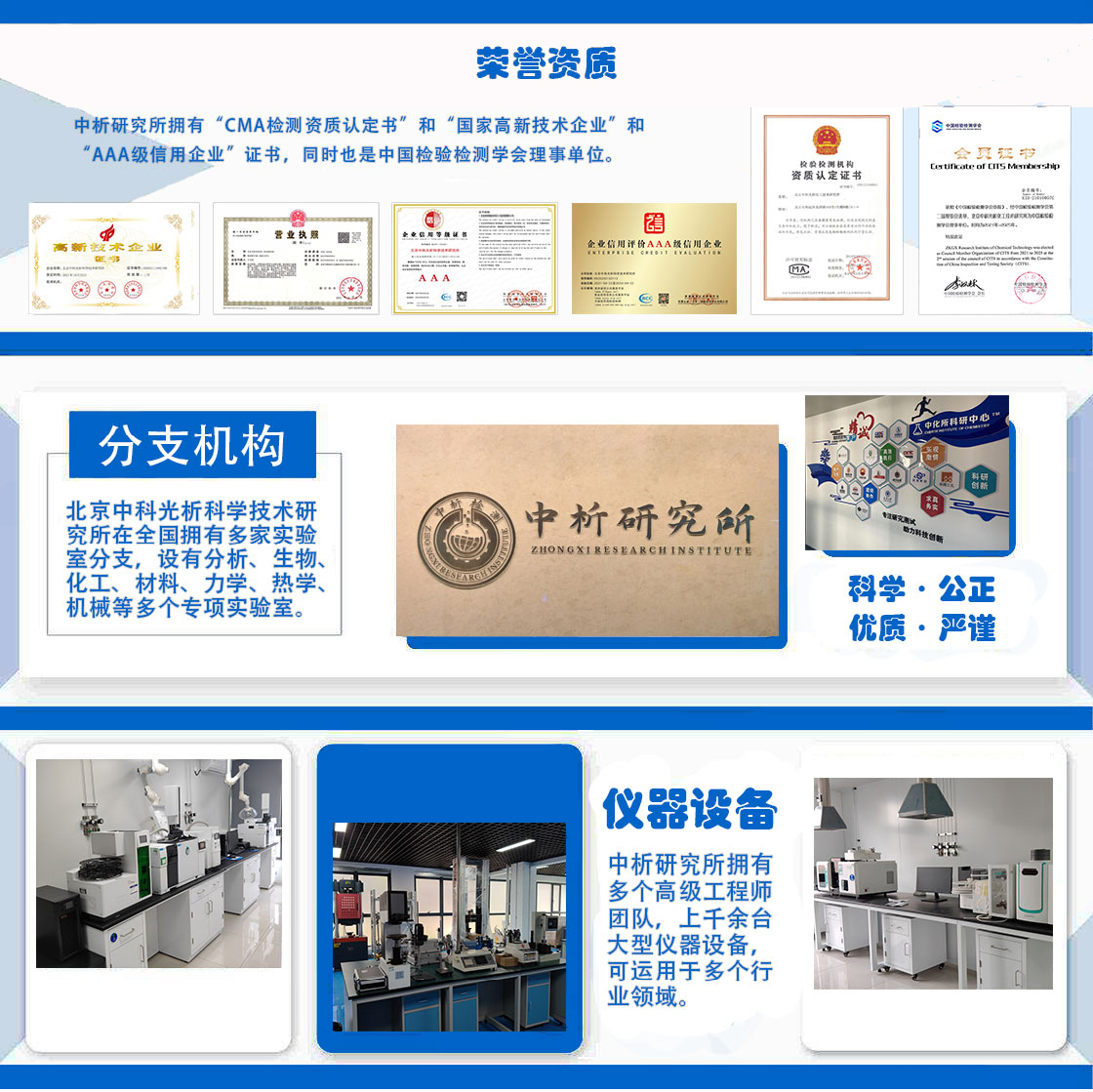
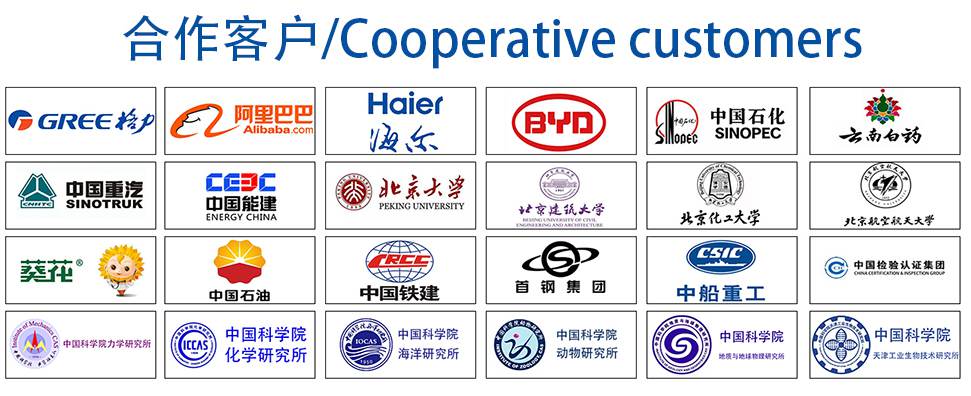