船体防污防锈漆检测的重要性
船体防污防锈漆是船舶维护中至关重要的保护层,其性能直接关系到船舶的使用寿命、航行效率及运营成本。这类涂料通过抑制海洋生物附着和延缓金属腐蚀,可显著降低船体阻力、减少燃料消耗,并延长维修周期。然而,若涂装质量不达标或检测不到位,可能导致漆膜开裂、剥落或防污失效,进而引发船体锈蚀、生物污损等问题,甚至造成环境污染。因此,针对船体防污防锈漆的系统化检测,是船舶建造和日常维护中不可或缺的环节。
核心检测项目与标准
1. 附着力测试
附着力是衡量漆膜与船体基材结合强度的关键指标,直接影响涂层的耐久性。检测常采用划格法(ASTM D3359)或拉拔法(ISO 4624),通过专用仪器测量漆膜剥离所需力值,确保其符合IMO PSPC标准(≥5MPa)。
2. 耐腐蚀性能检测
通过盐雾试验(ASTM B117)模拟海洋环境,连续喷洒含盐雾滴并观察漆膜腐蚀情况。同时结合电化学阻抗谱(EIS)分析,评估涂层对金属基体的保护效率,测试周期通常需500-1000小时以上。
3. 防污剂释放率测定
针对自抛光防污漆,需检测防污剂(如铜离子、有机硅)的释放速率。利用旋转挂片法(ISO 15181)或实验室动态模拟装置,监测单位时间内有效成分的释放量,确保其符合IMO生物杀灭剂管控要求。
4. 漆膜厚度均匀性检测
采用磁性测厚仪(干膜)或超声波测厚仪(湿膜),按照ISO 19840标准对船体不同区域进行多点测量。干膜总厚度通常需达到200-400μm,且厚度偏差需控制在±20%以内。
5. 耐候性与老化试验
通过紫外加速老化箱(ASTM G154)模拟长期日照影响,配合循环盐雾-湿热试验(ISO 11997-2),评估漆膜抗粉化、变色及开裂能力。试验周期通常为1000-3000小时,要求漆膜保光率≥80%。
6. 环保性能分析
依据IMO《防污系统公约》和欧盟BPR法规,检测涂料中重金属(如铜、锌)、有机锡化合物及VOC含量。需采用ICP-MS检测重金属,GC-MS分析挥发性有机物,确保符合TBT<1%等限值要求。
检测流程与质量控制
完整的检测流程涵盖实验室测试、现场施工监测及实船验证三个阶段。需建立从原材料验收到涂装过程监控的全链条质量管理体系,结合无损检测技术(如红外热成像)及时发现涂层缺陷,确保防护效果达到设计寿命(通常5-7年)。
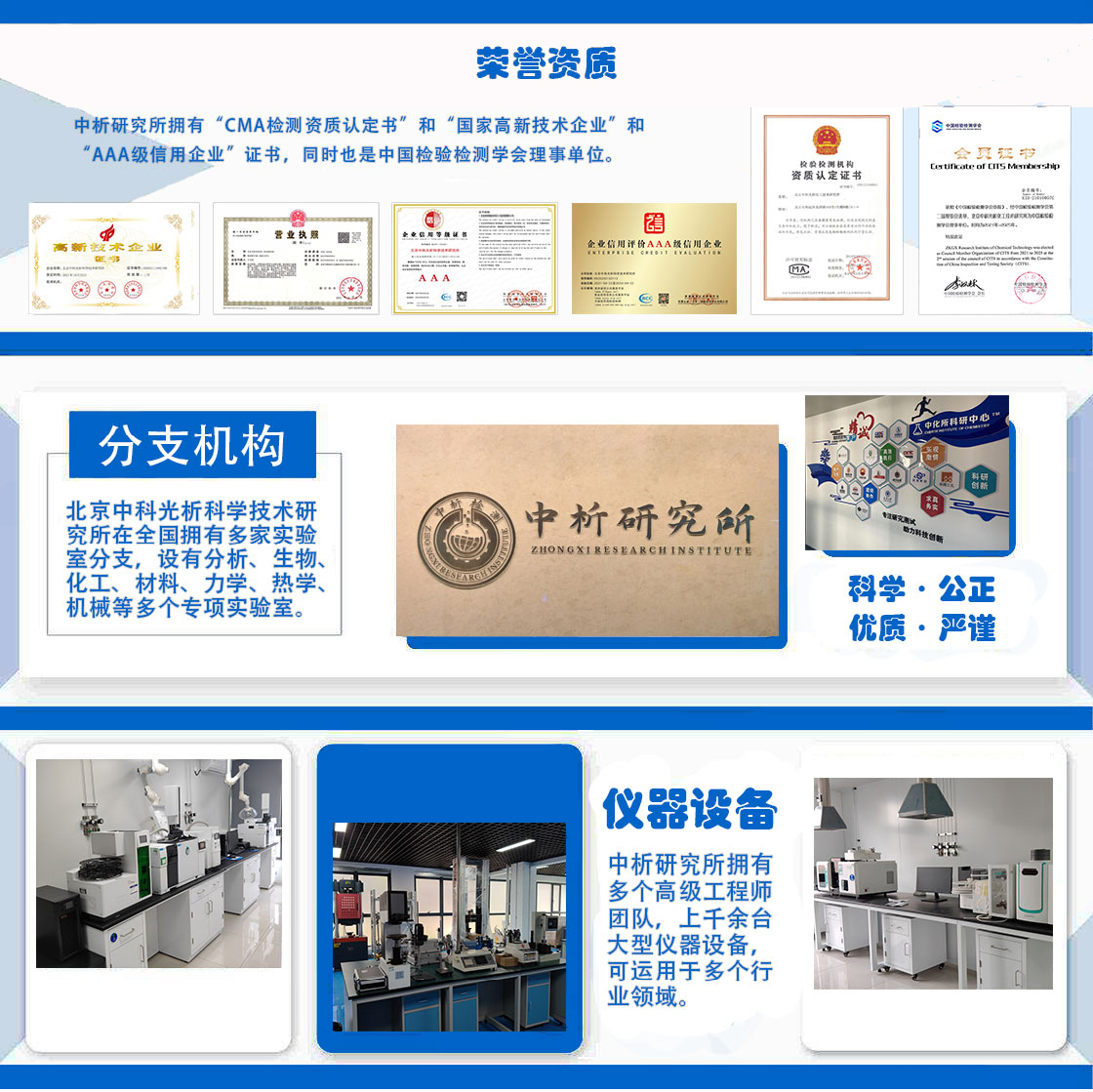
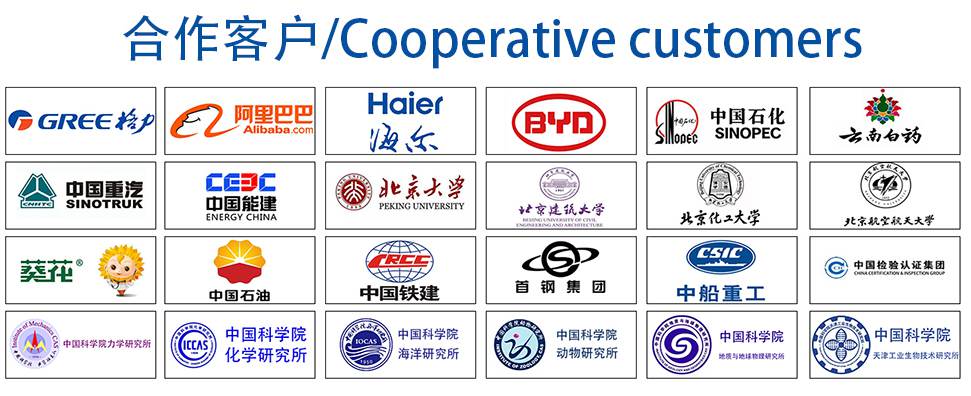