军用航空轮胎内胎检测技术与标准解析
军用航空轮胎作为飞机起降系统的核心部件,其性能直接关系到飞行安全与作战效能。与民用轮胎相比,军用轮胎需承受更高强度的冲击载荷(可达50吨以上)、极端温度(-55℃至70℃)以及复杂战场环境考验。内胎作为轮胎承压与密封的关键单元,其完整性检测贯穿生产制造、装机前验收、定期维护全生命周期。现代军用航空领域已形成涵盖物理性能、材料特性、环境适应性等6大维度的标准化检测体系,确保内胎在高速滑跑、硬着陆等高危场景下的可靠性。
核心检测项目与实施方法
1. 气密性综合检测
采用氦质谱检漏技术实现0.1Pa·m³/s级微泄漏定位,结合三级压力循环测试(0.8-3.5倍工作压力)。通过MIL-DTL-87131标准规定的72小时保压试验,压降需小于初始值的2%。新型数字孪生系统可模拟不同海拔气压下的密封性能衰减曲线。
2. 结构完整性无损检测
实施多模态探伤方案:X射线断层扫描(CT)检测帘线层分布均匀性;脉冲涡流检测金属气门嘴腐蚀;超声相控阵扫描发现≥0.3mm的橡胶分层缺陷。配备AI图像分析系统,对比历史数据自动标记异常区域。
3. 动态疲劳性能测试
在专用多轴试验台模拟舰载机拦阻着陆工况,记录内胎在300次/分钟的脉冲载荷下的形变特征。依据ASTM D430标准,橡胶材料需保证10^6次循环后动态模量衰减不超过15%,同时监测热量积聚对胎压的影响。
4. 极端环境适应性验证
通过三综合试验箱进行温度-湿度-振动耦合测试:在-54℃低温环境中保持48小时后进行瞬时加压;模拟沙漠环境进行120℃热砂冲击试验;盐雾舱内连续暴露96小时评估金属件耐腐蚀性,氯离子渗透深度需小于0.1mm。
5. 材料老化寿命评估
采用加速老化试验(70℃×80%RH条件下持续2000小时)结合Arrhenius模型预测橡胶寿命。利用傅里叶红外光谱分析氧化诱导期,当抗臭氧剂消耗量达到60%时触发更换预警。同步开展实装机队服役数据回归分析,修正理论模型偏差。
6. 智能传感器集成检测
植入MEMS压力-温度双模传感器,实现胎压实时监控(采样频率100Hz)。开发专用诊断算法,通过压力波动频谱分析识别早期慢漏气现象。数据链系统满足MIL-STD-1553B总线协议,与飞机健康管理系统无缝对接。
检测技术发展趋势
当前军用航空轮胎检测正朝着智能化、原位化方向发展。基于太赫兹波的复合材料内部成像技术可穿透30mm橡胶层实现三维缺陷重构,量子点示踪剂可标记微观裂纹扩展路径。未来将建立涵盖材料基因库-服役大数据-数字孪生的全要素检测生态系统,将内胎可靠性指标提升至99.999%级。
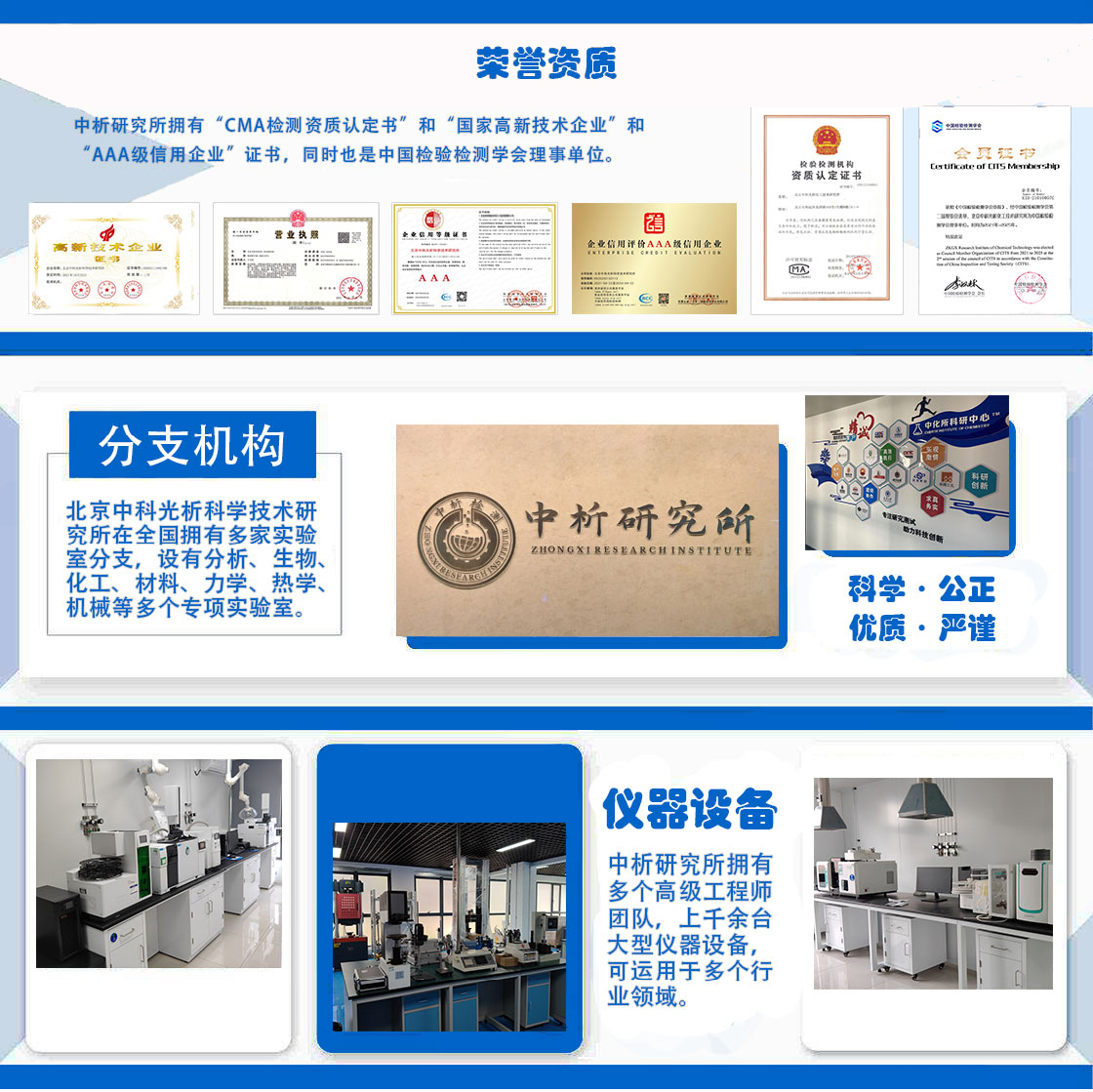
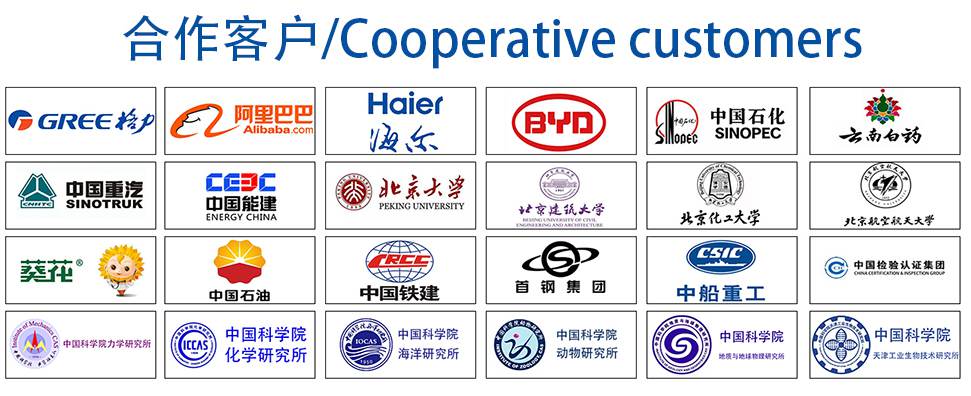