耐热管路涂料作为工业设备防护体系中的重要组成部分,广泛应用于石油化工、电力能源、冶金制造等高温工况环境。其核心功能是保护金属管道在极端温度下(通常为200℃~1200℃)抵抗氧化腐蚀、热应力冲击及化学介质侵蚀,从而延长设备使用寿命并保障运行安全。随着工业技术对材料性能要求的不断提升,耐热涂料的质量控制与性能检测成为生产商、使用单位及第三方检测机构关注的重点。通过科学系统的检测项目,可有效评估涂料的综合性能,确保其在实际应用中的可靠性与稳定性。
一、耐热性能检测
耐热性作为核心指标,通过高温循环试验模拟实际工况。测试时将涂层样品置于程序控温箱中,在设定温度(如800℃)下持续加热并冷却至室温,循环多次后观察涂层表面是否出现开裂、剥落或颜色变化。同时结合热重分析(TGA)检测涂料在升温过程中的质量损失率,评估其热稳定性。部分标准要求测试涂层在高温下的导热系数变化,以验证其隔热性能是否符合设计要求。
二、附着力测试
涂层与基材的附着力直接影响其防护效果。采用划格法(ASTM D3359)或拉拔法(ISO 4624)进行定量检测:划格法通过网格划割涂层后观察脱落面积,拉拔法则通过专用仪器测量剥离涂层所需的拉力值。对于高温环境,还需进行高温附着力测试,即在加热状态下评估涂层与金属管道的结合强度,避免因热膨胀系数差异导致失效。
三、耐腐蚀性检测
通过盐雾试验(GB/T 1771)模拟海洋或化工环境中的腐蚀条件,将试样置于35℃、5% NaCl溶液喷雾环境中持续720小时,观察涂层起泡、锈蚀情况。针对酸碱介质环境,需进行化学试剂浸泡试验,测定涂层在特定浓度酸碱液中的耐蚀等级。电化学阻抗谱(EIS)技术可更精准地分析涂层在腐蚀介质中的防护性能衰减趋势。
四、抗热震性测试
模拟管道系统频繁启停导致的温度骤变工况。将涂层试样在高温炉(如600℃)与冷水槽(25℃)之间进行快速交替,记录涂层出现裂纹或剥落前的循环次数。该测试需结合显微成像技术分析涂层微观结构变化,评估其抗热疲劳性能。
五、物理性能检测
包括硬度(铅笔硬度或邵氏硬度)、耐磨性(Taber磨耗试验)、柔韧性(轴弯试验)等基础指标。高温硬度测试需使用专用高温压痕仪,测定涂层在热态下的机械强度。此外,涂层厚度(磁性测厚仪)与孔隙率(电解法)直接影响其防护效果,需严格按GB/T 13452.2标准控制。
六、环保性能检测
依据GB 30981标准检测涂料中VOCs(挥发性有机物)含量,并采用GC-MS分析重金属(铅、镉、汞等)及有毒物质残留。对于高温分解产物,需通过热解吸-质谱联用技术评估其在受热时是否释放有害气体。
七、综合评估体系
建立包含加速老化试验(氙灯老化、紫外老化)、实际工况模拟测试及长期跟踪监测的多维度评价模型。通过大数据分析不同检测项目间的关联性,例如高温附着力与热震循环次数的相关性,为配方优化提供数据支撑。
耐热管路涂料的检测需贯穿研发、生产及验收全流程,通过标准化检测手段确保产品满足特定工况需求。随着智能检测技术的发展,红外热成像、声发射监测等无损检测技术将进一步推动行业质量管控水平的提升。
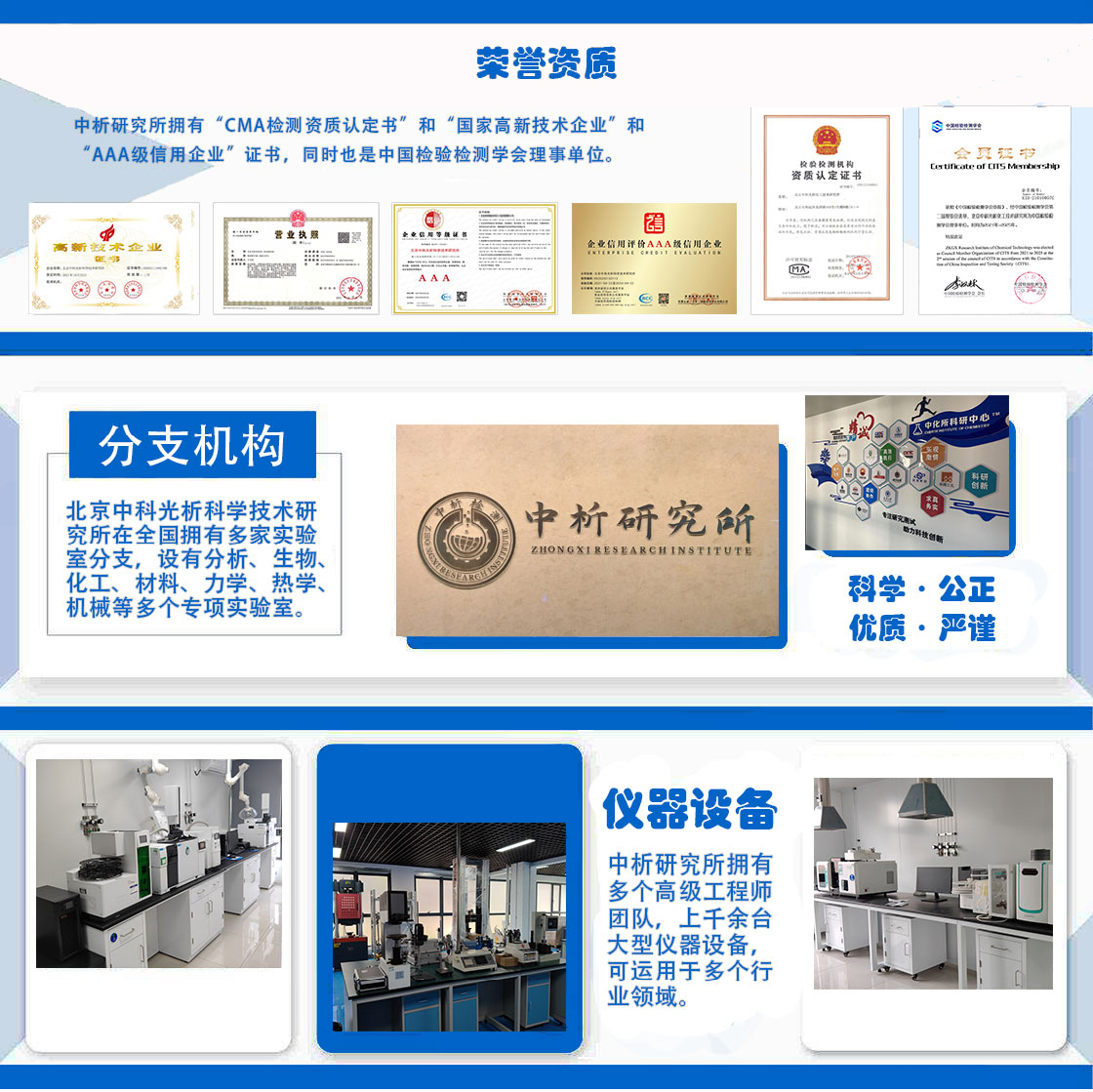
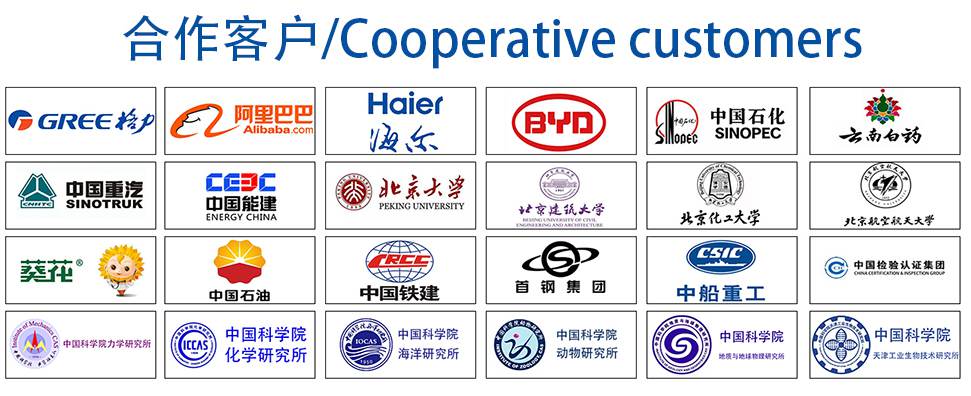