金属结构材料检测的重要性与应用领域
金属结构材料作为工业制造、建筑工程、航空航天等领域的基础材料,其性能直接关系到设备安全性、使用寿命和工程可靠性。随着现代工业对材料强度、耐腐蚀性及加工精度的要求不断提高,金属材料的检测成为质量控制的核心环节。检测项目需覆盖从原材料到成品的全生命周期,通过科学分析确保材料成分、力学性能和微观结构的合规性,防范因材料缺陷引发的安全隐患。
核心检测项目分类与技术要求
1. 化学成分分析
通过光谱分析(OES)、X射线荧光光谱(XRF)或化学滴定法,检测金属材料中碳、硅、锰、铬等元素的含量。例如,不锈钢中铬含量需≥10.5%以满足抗腐蚀要求,而合金钢的微量元素配比直接影响其热处理性能。
2. 力学性能测试
包含拉伸试验(测定抗拉强度、屈服强度、延伸率)、硬度测试(布氏/洛氏/维氏硬度计)、冲击韧性试验(夏比冲击试验)。如Q345B钢材要求屈服强度≥345MPa,冲击功需满足-20℃低温环境下的使用需求。
3. 微观组织分析
采用金相显微镜、扫描电镜(SEM)观察晶粒度、夹杂物分布及相组成。例如,轴承钢需控制碳化物颗粒尺寸≤3μm,铝合金需避免枝晶偏析现象。
4. 无损检测技术
应用超声波探伤(UT)检测内部裂纹、磁粉探伤(MT)发现表面缺陷、渗透检测(PT)验证焊接质量。按ISO 5817标准,承压容器焊缝缺陷需控制在B级验收范围内。
5. 耐腐蚀性评估
通过盐雾试验(ASTM B117)、晶间腐蚀试验(GB/T 4334)等验证材料抗环境侵蚀能力。海洋平台用钢需通过720小时中性盐雾测试无红锈产生。
检测标准与质量控制体系
检测过程需严格遵循GB/T、ASTM、ISO、EN等国内外标准体系。实验室应取得 /CMA认证,使用经计量校准的设备,并建立完整的质量管理追溯系统。例如,钢结构检测需同步执行GB 50205(验收规范)与JGJ 81(焊接规程)。
结语
金属结构材料检测是保障工业安全的重要技术屏障。通过多维度的检测项目组合与智能化检测设备应用,可精准识别材料潜在缺陷,为材料选型、工艺优化提供数据支撑,助力实现"中国制造2025"对高端材料性能的突破性要求。
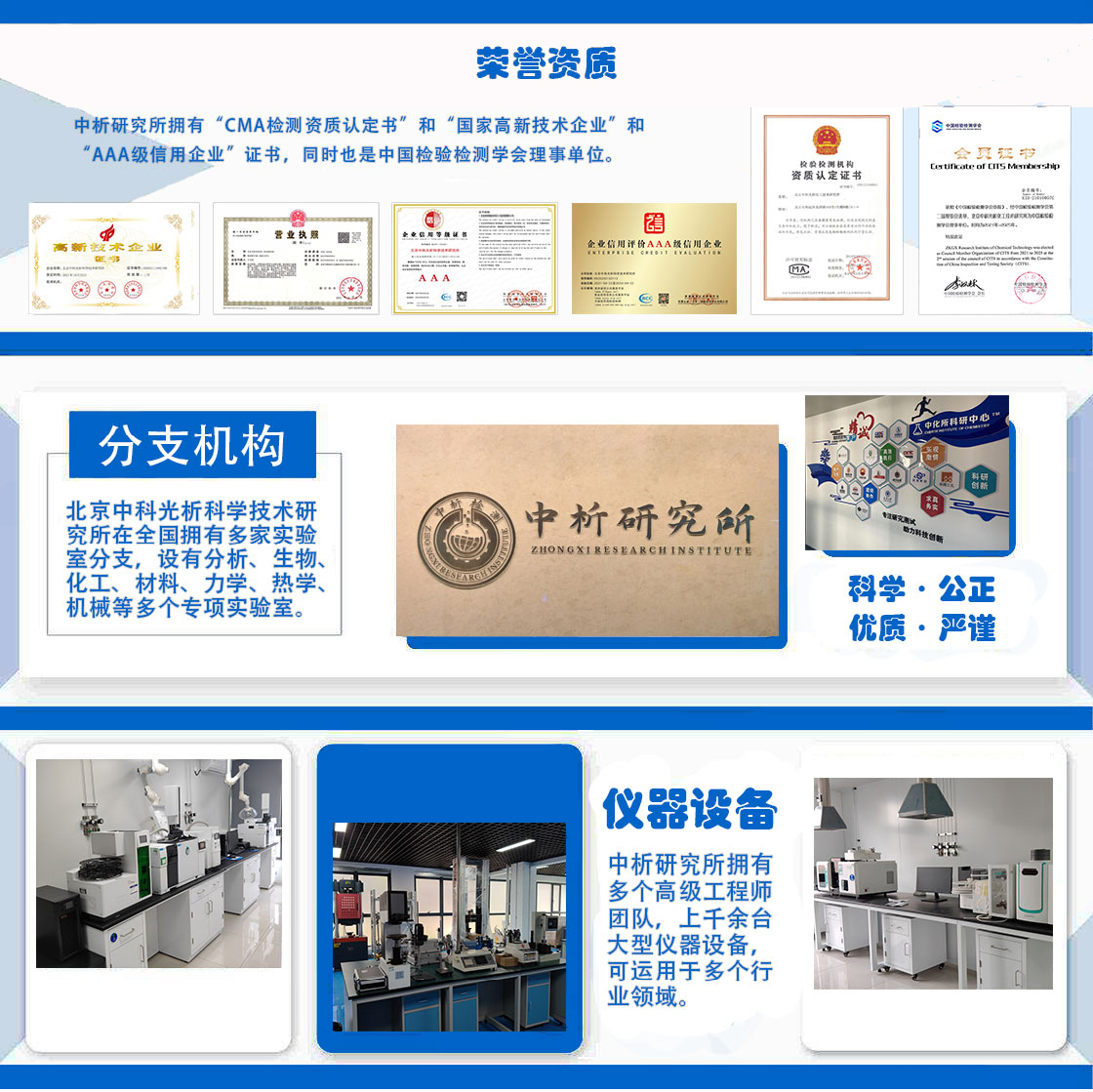
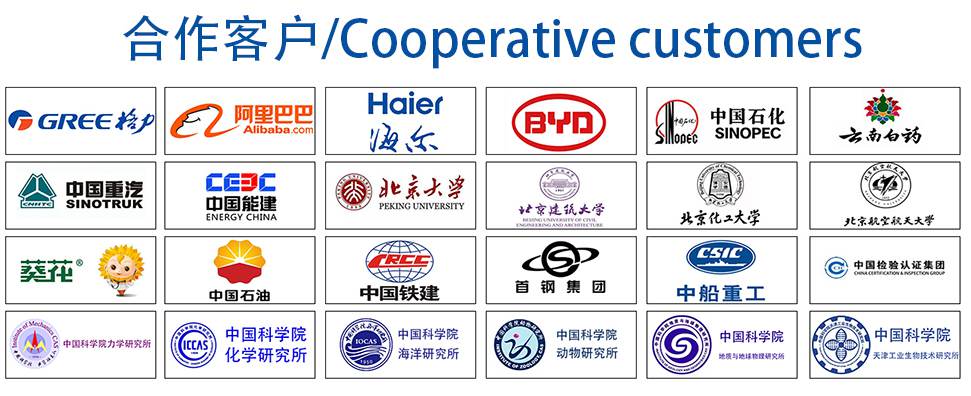