钢构件材料检测的重要性与核心项目
在建筑工程、桥梁工程及工业设备制造领域,钢构件作为承重结构的关键材料,其性能直接影响工程安全性与耐久性。钢构件材料检测通过科学手段验证材料的物理化学特性,确保其符合设计规范与国家标准。随着现代工程对材料性能要求的提升,检测项目已从常规力学性能测试扩展至微观组织分析、环境适应性评估等精细领域。
核心检测项目分类
1. 化学成分分析:
采用光谱分析仪(OES)和碳硫分析仪,检测C、Si、Mn、P、S五大基础元素及合金元素含量,验证是否符合GB/T 700(碳素结构钢)或GB/T 1591(低合金高强度钢)等标准要求。
2. 力学性能测试:
• 拉伸试验:测定屈服强度、抗拉强度、断后伸长率(依据GB/T 228.1)
• 冲击试验:-20℃低温夏比冲击功检测(参照GB/T 229)
• 硬度测试:布氏硬度(HBW)或洛氏硬度(HRC)检测
3. 无损检测:
• 超声波探伤(UT):检测内部裂纹、夹渣等缺陷
• 磁粉探伤(MT):发现表面及近表面缺陷
• 射线检测(RT):适用于焊缝质量评估
4. 金相分析:
通过显微镜观察晶粒度(ASTM E112)、非金属夹杂物(GB/T 10561)及显微组织形态(如铁素体/珠光体分布),判断材料热加工工艺的合理性。
5. 尺寸与几何公差检测:
使用三坐标测量仪、激光轮廓仪等设备,验证构件加工精度是否符合GB/T 1804(一般公差)或特定工程图纸要求。
6. 腐蚀性能检测:
开展盐雾试验(GB/T 10125)、电化学阻抗谱分析,评估镀锌层厚度或防腐涂层的耐久性。
检测流程与标准体系
典型检测流程包含:取样→预处理→设备校准→参数测试→数据比对→报告签发。检测机构需同时遵循国家标准(GB)、行业标准(JGJ/T)及国际通用标准(如ASTM、ISO),对于出口构件还需满足EN 10025(欧标)或JIS G 3106(日标)等特定区域标准。
通过系统化的检测体系,可精准识别材料批次异常、工艺缺陷及环境劣化风险,为工程质量控制提供关键数据支撑。随着智能检测技术的应用,基于机器视觉的缺陷自动识别、大数据质量追溯系统正在推动钢构件检测进入数字化新阶段。
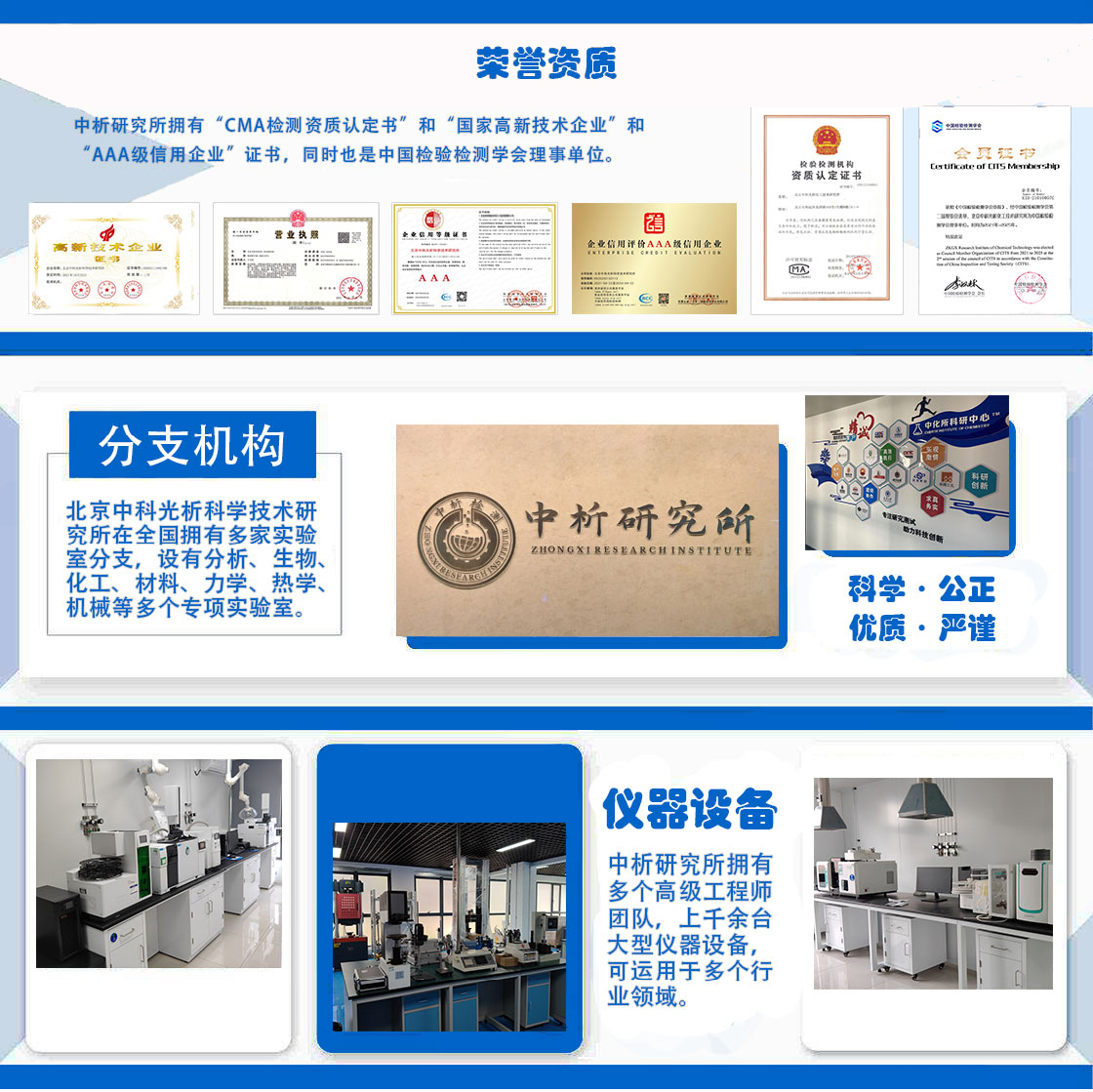
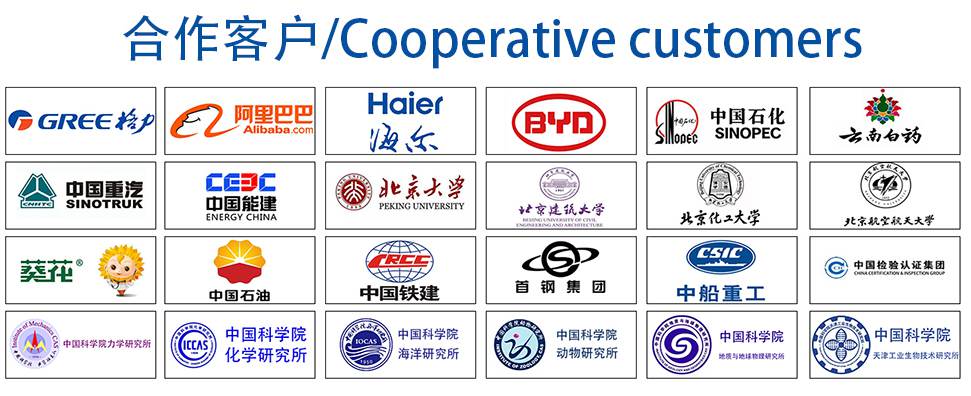