给水管材/管件检测的重要性
给水系统是城市基础设施的重要组成部分,其安全性直接关系到居民生活用水质量和公共卫生安全。作为输水载体的管材及管件,需长期承受水压、温度变化、化学腐蚀等复杂工况,一旦出现质量问题可能导致爆管、渗漏或水质污染等严重后果。因此,依据国家标准(如GB/T 17219、GB/T 6111)和行业规范,对给水管材/管件开展系统化检测是保障供水安全、延长管网寿命的核心环节。检测范围涵盖物理性能、化学稳定性、卫生安全指标等八大类项目,贯穿产品生产、施工安装及运维全周期。
关键检测项目解析
1. 物理力学性能检测
通过万能材料试验机测定拉伸强度、弯曲强度和冲击韧性,验证管材在高压水流冲击下的抗变形能力。环刚度测试模拟地下敷设时承受的外部载荷,落锤冲击试验则评估低温环境下的脆性断裂风险。
2. 耐压与密封性检测
采用液压试验台进行短期静液压强度测试(GB/T 6111),在2.5倍公称压力下保压1小时检测管体渗漏情况。气密性试验通过0.6MPa气压检测管件连接处的密封可靠性,同时运用超声波探伤技术排查焊接缺陷。
3. 化学稳定性验证
将试样浸泡于模拟水体(pH 6.5-8.5)中30天,检测铅、镉等重金属析出量(GB/T 17219)。耐酸碱试验采用10%硫酸/氢氧化钠溶液进行168小时腐蚀测试,计算质量变化率需≤1.5%。
4. 卫生安全指标检测
针对饮用水接触材料,重点检测挥发性有机物(VOC)、酚类化合物及三氯甲烷迁移量。微生物指标须符合《生活饮用水输配水设备卫生安全评价规范》,抗菌型管材还需通过QB/T 2591抗菌率试验(≥90%)。
5. 热稳定性试验
对PPR、PB等热塑性管材进行135℃±2℃纵向回缩率测试,要求形变量≤2%。冷热水循环试验模拟实际使用工况,2000次循环后检测管体开裂、分层等失效现象。
6. 连接部件专项检测
管件需通过5000次机械连接疲劳试验,螺纹接口进行扭矩-密封相关性分析。电熔管件的熔接界面需进行金相检验,确保熔合深度≥管材壁厚的90%。
质量控制关键点
检测过程需严格执行ISO/IEC 17025体系要求,重点监控原材料树脂的熔融指数(MFI)波动,采用差示扫描量热仪(DSC)分析聚乙烯管材的氧化诱导时间(OIT),确保≥20分钟。出厂检验须100%进行外观尺寸检查和涡流探伤,每批次抽样开展型式试验。
结语
完善的给水管材/管件检测体系可有效预防管网渗漏率(控制在12%以下),降低输水损失,同时保障饮用水质符合GB 5749要求。随着智能检测技术的发展,分布式光纤压力监测、管壁厚度在线超声检测等新方法正在推动行业质量控制水平持续提升。
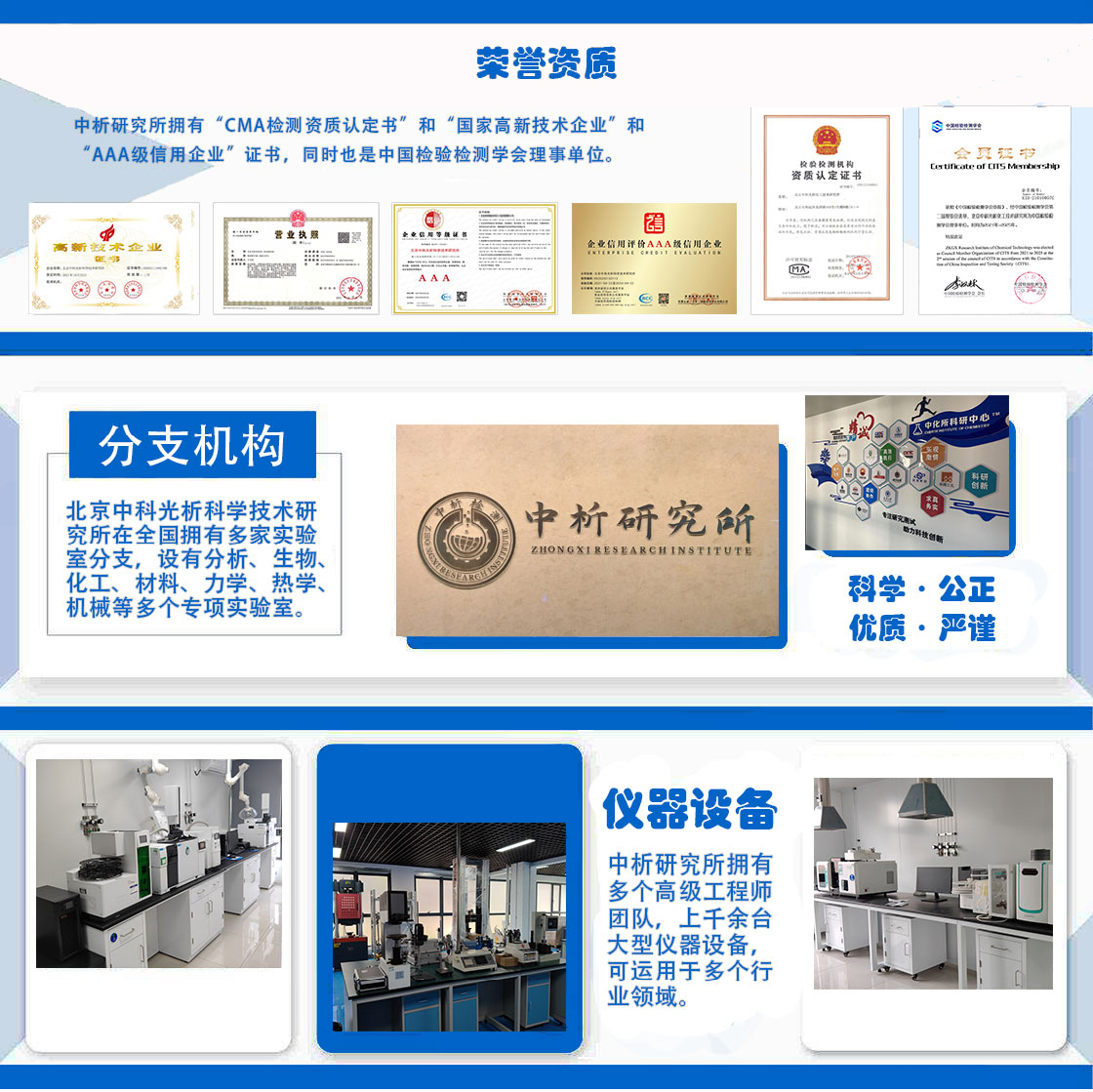
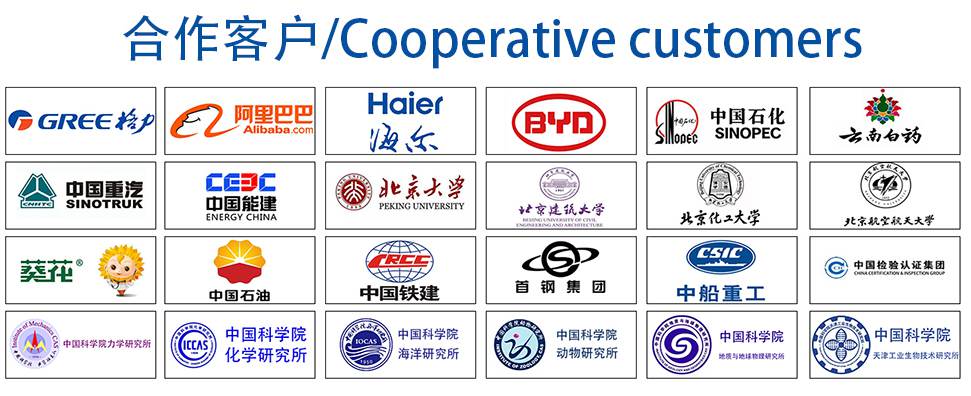