无损检测技术:现代工业的安全卫士
无损检测(Non-Destructive Testing, NDT)作为现代工业质量控制的基石,通过对材料、零部件或结构进行非破坏性检查,在确保工程安全性与可靠性的同时,避免了传统破坏性检测带来的资源浪费。从航空航天到石油化工,从桥梁建筑到精密制造,无损检测技术的应用贯穿于产品全生命周期,成为预防事故、降低维护成本的核心手段。
核心检测项目与技术解析
无损检测包含多种技术手段,每种方法针对不同的缺陷类型和材料特性,形成了一套完整的检测体系:
超声波检测(UT)
通过高频声波在材料内部的反射与传播特性,精准定位裂纹、气孔等内部缺陷。适用于金属、复合材料及焊接接头检测,分辨率可达毫米级,但对操作人员技术要求较高。
射线检测(RT)
利用X射线或γ射线穿透物体形成影像,直观显示铸件缩孔、焊缝未熔合等体积型缺陷。常用于压力容器、管道焊缝检测,需严格遵循辐射安全规范。
磁粉检测(MT)
对铁磁性材料表面及近表面缺陷具有极高灵敏度。通过磁化后磁粉在漏磁场处的聚集现象,可快速发现疲劳裂纹、折叠等线性缺陷,广泛应用于轨道交通部件检测。
渗透检测(PT)
通过显像剂与渗透液的毛细作用,凸显材料表面开口缺陷。适用于非多孔性材料的裂纹检测,操作简单但仅限表面缺陷识别。
涡流检测(ET)
基于电磁感应原理,通过探头阻抗变化检测导电材料的表面及近表面缺陷。特别适用于薄壁管材、航空发动机叶片的自动化快速检测。
检测项目的实施与标准体系
规范的检测流程包含三个关键阶段:
1. 前期准备:根据材料特性、服役环境选择检测方法,制定检测方案
2. 数据采集:使用校准合格的设备按标准操作程序实施检测
3. 结果判定:依据ASTM、ISO或GB/T等标准对缺陷进行分级评价
国际标准与行业规范
主要检测标准包括:
- ISO 9712 无损检测人员资格认证
- ASME BPVC 第V卷 锅炉压力容器检测规范
- GB/T 9445 中国无损检测人员资格鉴定标准
企业需根据产品特性选择适用标准,并定期进行检测系统验证。
技术创新与发展趋势
随着人工智能与物联网技术的融合,数字射线成像(DR)、相控阵超声(PAUT)、导波检测等新技术正在推动NDT向智能化方向发展。工业4.0时代,在线监测与大数据分析将进一步扩展无损检测的应用边界。
通过科学选择检测项目、严格执行标准流程,无损检测技术将持续为工业安全保驾护航,在质量控制领域发挥不可替代的作用。
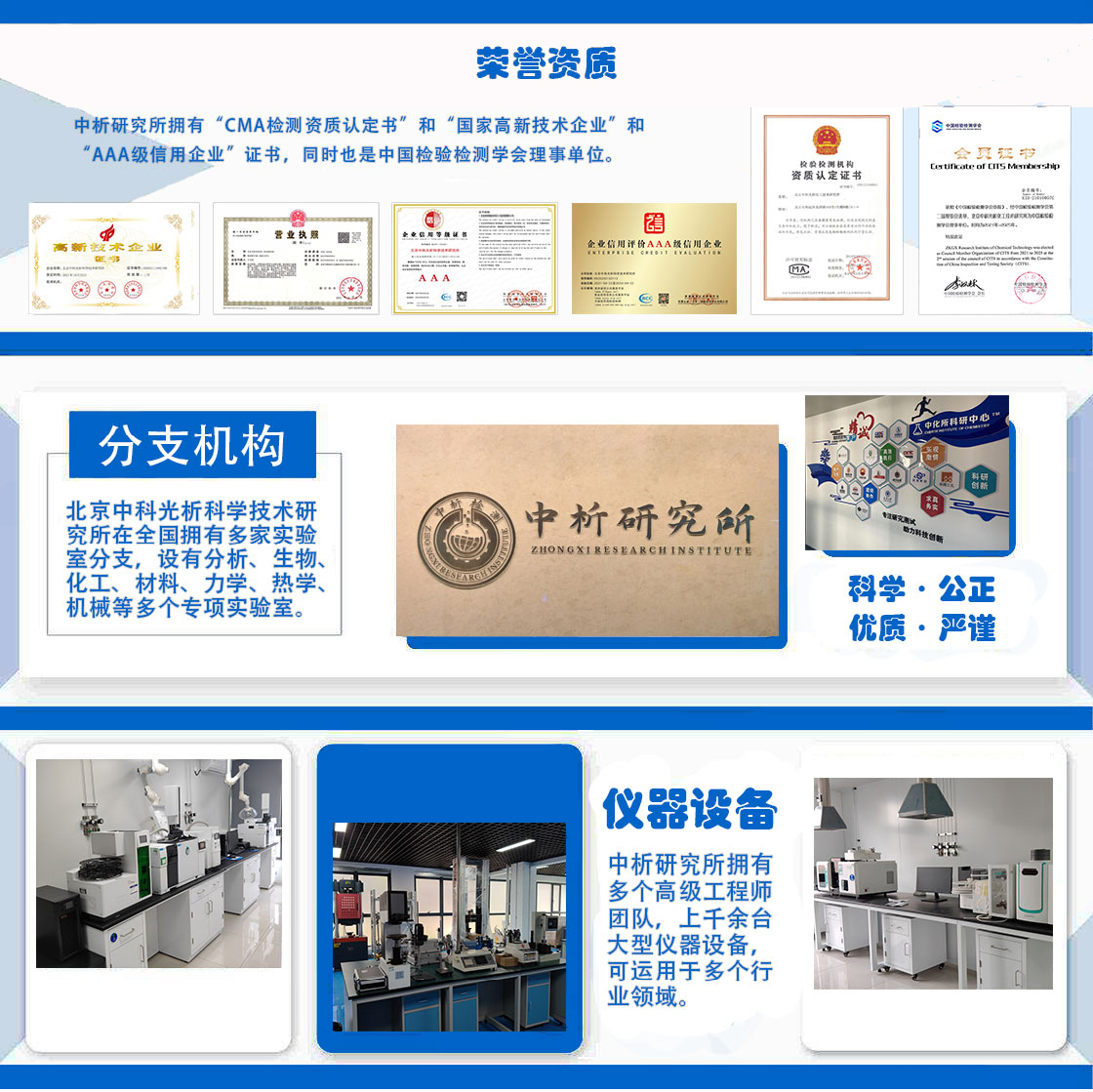
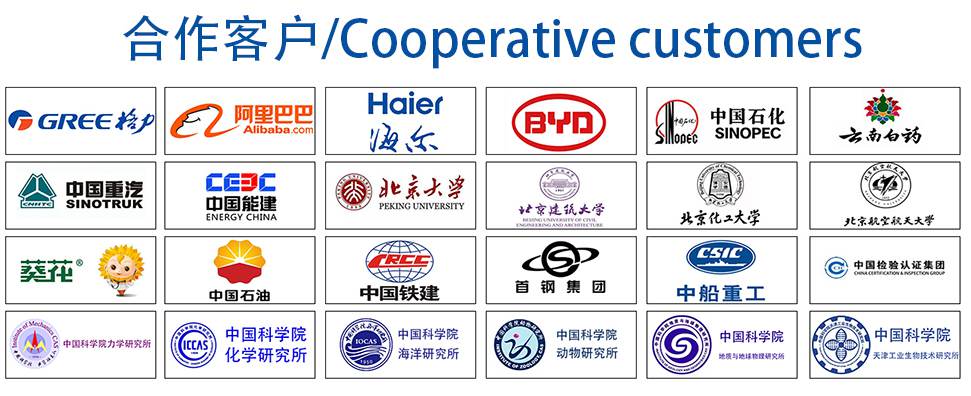