钢构件防腐层质量检测的重要性
钢构件在工业、建筑、桥梁等领域的应用广泛,但其长期暴露于潮湿、盐雾、化学介质等腐蚀性环境中,易发生锈蚀问题,导致结构强度下降、使用寿命缩短甚至安全隐患。防腐层作为保护钢构件的第一道防线,其质量直接决定了抗腐蚀效果。因此,钢构件防腐层质量检测是工程验收、日常维护及安全评估的关键环节。通过系统化的检测项目,可有效评估涂层的完整性、附着力、厚度等性能,确保防腐层满足设计要求并适应实际工况。
主要检测项目及方法
1. 防腐层外观检查
外观检测是防腐层质量的基础评估项目。通过目视或放大镜观察防腐层表面是否存在气泡、裂纹、剥落、流挂、橘皮等缺陷。同时需检查涂层是否均匀覆盖基材,特别是焊缝、边角等易漏涂区域。对于热镀锌层,还需关注锌瘤、漏镀等问题。
2. 防腐层厚度测量
厚度是防腐层性能的核心指标,直接影响防护年限。检测工具包括磁性测厚仪(适用于磁性基材)、超声波测厚仪(非磁性基材)或涂层剖面显微镜。依据标准(如ISO 19840、GB/T 4956),需在不同位置取点测量,计算平均厚度及最小局部厚度。例如,C3环境下环氧富锌底漆厚度需≥60μm,C5环境则需≥120μm。
3. 附着力测试
评估防腐层与基材的结合强度,常用方法包括划格法(ASTM D3359)、拉拔法(ISO 4624)。划格法通过划出网格并贴胶带剥离,观察涂层脱落面积;拉拔法则用专用仪器垂直拉拔,记录破坏时的拉力值(如≥5MPa为合格)。附着力差易导致涂层提前失效。
4. 孔隙率检测
检测防腐层是否存在针孔、微裂纹等缺陷。采用电火花检测仪(适用于导电基材)或湿海绵法(低电压法)。电火花检测通过高压探针对涂层扫描,遇孔隙时产生放电报警。对于环氧涂层,检测电压通常为1-5kV/mm涂层厚度。
5. 防腐层硬度测试
硬度反映涂层的耐磨性和抗机械损伤能力。巴氏硬度计(ASTM D2583)或铅笔硬度法(ASTM D3363)常用于现场检测。例如,聚氨酯面漆的巴氏硬度应≥40,氟碳涂层则需≥60。
6. 耐化学介质性能测试
通过实验室浸泡试验或现场模拟试验,评估防腐层在酸、碱、盐等介质中的稳定性。依据ISO 2812标准,将试样浸泡于3% NaCl溶液或5% H2SO4溶液中,观察72小时后的起泡、变色情况。
7. 加速老化试验
模拟长期环境影响的加速试验,包括盐雾试验(ASTM B117)、紫外线老化试验(ASTM G154)及循环腐蚀试验(ASTM D5894)。例如,盐雾试验中,合格涂层应在1000小时内无基材腐蚀。
检测结果分析与应用
检测数据需对照设计标准(如ISO 12944、NACE SP0169)进行综合判断。对于未达标项,需分析原因并提出修复方案,如局部打磨补涂或整体返工。定期检测报告可作为防腐层寿命预测和维修计划制定的依据,实现全生命周期管理。
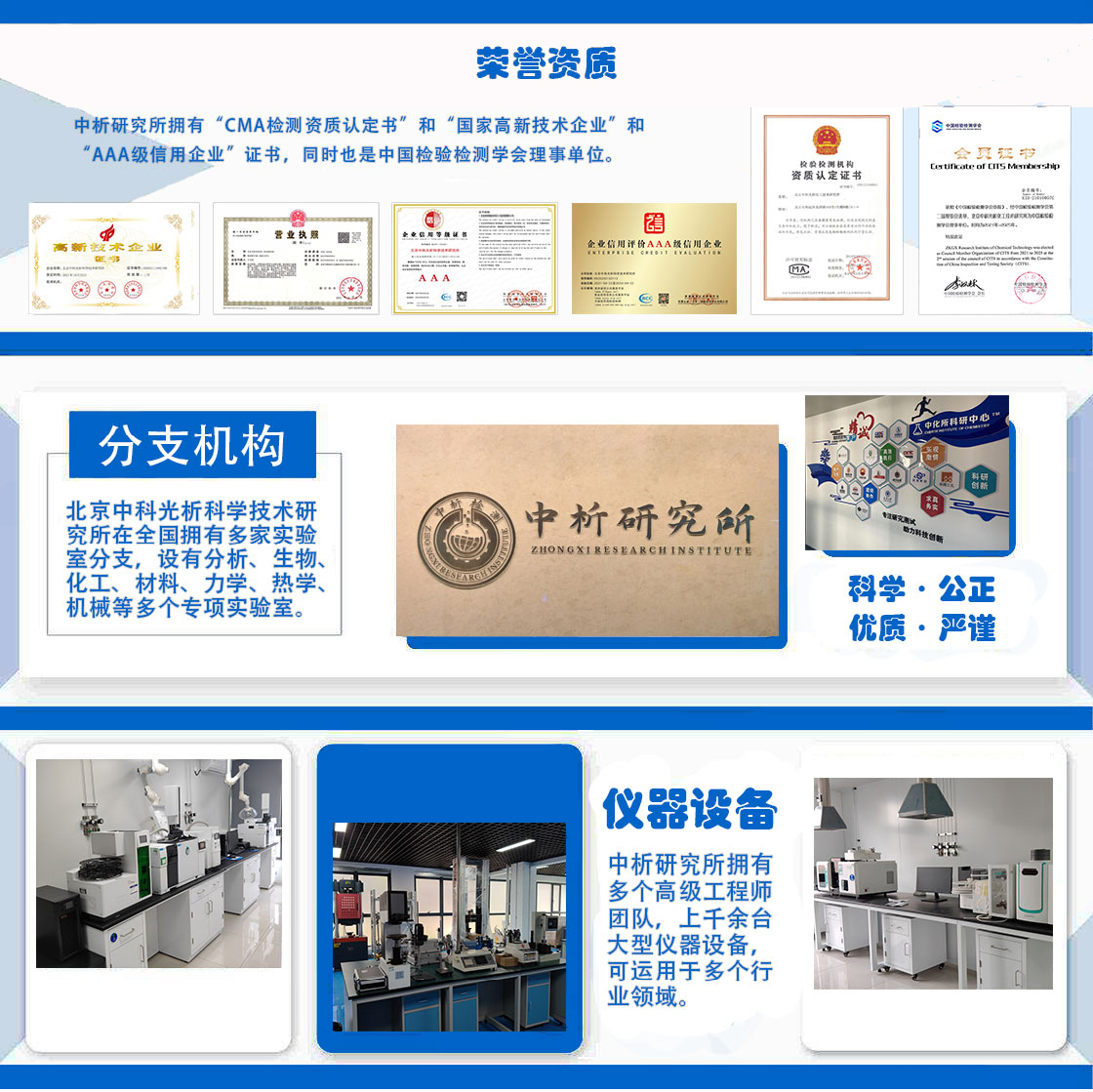
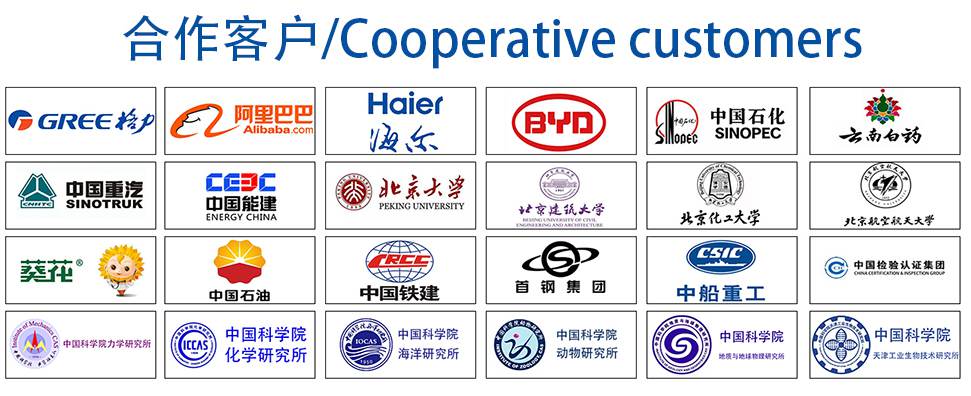