盐雾检测:材料耐腐蚀性能的关键评估手段
盐雾检测(Salt Spray Test)是一种通过模拟含盐潮湿环境,评估材料或表面涂层抗腐蚀能力的标准化测试方法。其核心原理是利用含氯化钠的雾化溶液持续喷洒样品,加速金属、合金及防护涂层的腐蚀过程,从而预测产品在真实海洋气候、工业污染或多盐环境中的耐久性。该测试广泛应用于汽车、船舶、航空航天、电子元器件、建筑五金等领域,尤其对暴露于恶劣环境的产品质量验证至关重要。通过盐雾检测,企业能有效优化材料选择、改进防护工艺并延长产品使用寿命。
盐雾检测的主要项目分类
1. 中性盐雾试验(NSS)
依据标准:ISO 9227、ASTM B117
测试条件:5% NaCl溶液,pH值6.5-7.2,温度35±2℃
适用对象:金属基材、电镀件、普通涂层
测试周期:24-1000小时不等
2. 醋酸盐雾试验(AASS)
依据标准:ISO 9227、DIN 50021
测试条件:在NaCl溶液中添加冰醋酸,pH值3.1-3.3
适用对象:铜+镍+铬或镍+铬装饰性电镀层
3. 铜加速醋酸盐雾试验(CASS)
依据标准:ISO 9227、ASTM B368
测试条件:添加氯化铜,pH值3.1-3.3,温度50±2℃
适用对象:铝合金阳极氧化层、汽车零部件涂层
4. 循环腐蚀试验(CCT)
依据标准:SAE J2334、GB/T 20853
测试特点:交替进行盐雾、干燥、湿热等多环境模拟
优势分析:更接近真实环境,检测精度提升30%-50%
测试流程与结果评估
完整检测流程包含:样品预处理(清洁、划痕处理)→设备参数校准→连续喷雾→定期观察记录→腐蚀等级判定。结果评估采用ISO 10289标准,通过计算腐蚀面积占比、气泡等级、附着力变化等指标,划分0-10级保护评级(RP)和外观评级(RA)。
关键影响因素解析
• 材料特性:不同金属的氧化电位差异显著
• 涂层工艺:电镀层厚度需≥20μm才能通过72小时测试
• 环境参数:温度每升高10℃,腐蚀速率提高2-3倍
• 喷雾均匀性:沉降量应稳定在1-2ml/80cm²·h范围内
行业应用实例
汽车制造
底盘件、紧固件需通过720小时NSS测试,满足QC/T 625标准
电子电器
PCB板三防涂层需通过48小时CASS测试,盐雾后绝缘电阻>100MΩ
海洋工程
船用钢构件涂层体系要求通过2000小时循环测试,腐蚀宽度<1mm
随着新型复合材料和纳米涂层技术的应用,现代盐雾检测正向多因素耦合测试、数字化腐蚀监测方向发展,为提升工业产品环境适应性提供更精准的技术支撑。
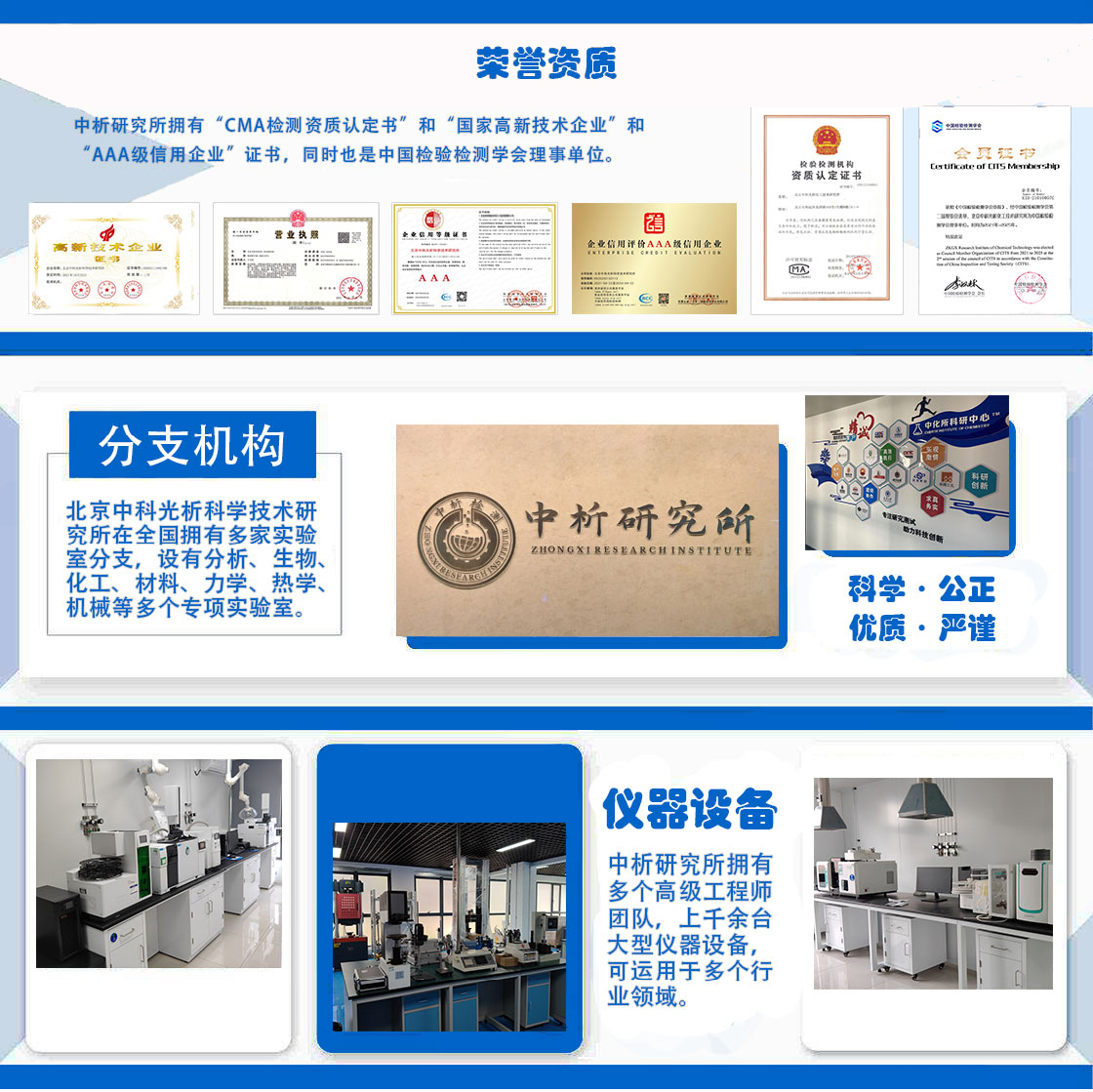
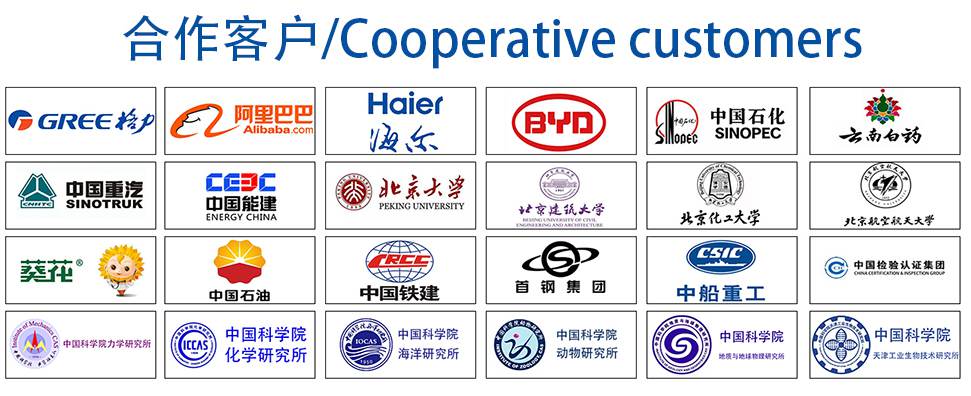