聚烯烃注塑包装桶检测的重要性
聚烯烃注塑包装桶以其耐腐蚀、重量轻、机械强度高、密封性好等特性,广泛应用于化工、食品、医药等行业的液体和粉状物料储存与运输。作为直接接触产品的容器,其质量直接影响内容物的安全性和稳定性。因此,严格的检测流程是确保包装桶符合相关国家标准(如GB/T 13508-2011《聚乙烯吹塑容器》)和行业规范的关键环节。检测项目需覆盖原材料性能、成型工艺、成品物理化学特性及使用安全性等多个维度,以保障其在极端环境下的可靠性和长期使用寿命。
主要检测项目及方法
1. 外观与尺寸检测
通过目视检查和量具测量,评估包装桶表面是否存在气泡、凹陷、毛刺等缺陷,同时验证桶体高度、直径、壁厚等关键尺寸是否符合设计公差(通常要求±2%以内)。重点检查注塑口平整度及合模线对齐情况,防止渗漏风险。
2. 密封性能测试
采用气压试验(0.03-0.05MPa保压5分钟)或水压试验,检测桶身与桶盖的密封性。合格标准为无泄漏、无永久变形,对于危化品包装还需通过气密性试验(I类包装要求≥30kPa)。
3. 物理机械性能检测
包括跌落试验(从1.2-1.8m高度自由跌落至刚性平面)、堆码试验(施加相当于3倍满载重量的压力持续24小时)、抗压试验(≥50kN载荷)等,评估包装桶在运输和仓储过程中的抗冲击、抗变形能力。
4. 化学稳定性测试
通过浸泡试验(如65%硝酸、40%氢氧化钠溶液浸泡7天)检测材料耐化性,测定质量变化率需≤1%。同时进行重金属迁移量检测(铅≤1mg/kg、镉≤0.5mg/kg),确保符合食品级包装GB 4806.7标准。
5. 环境应力开裂(ESCR)试验
采用ASTM D1693标准方法,将试样浸入表面活性剂(如Igepal CO-630),在50℃下观察500小时内的开裂情况。高品质聚烯烃桶应达到F50>1000小时的标准。
6. 熔体流动速率(MFR)检测
使用熔体流动速率仪测定原料树脂的MFR值(通常要求2-7g/10min),控制注塑成型时的流动性参数,确保产品具有稳定的结晶度和机械强度。
7. 卫生性能检测
针对食品医药用包装,需进行微生物限度、荧光物质、蒸发残渣(水浸泡液≤30mg/L)、高锰酸钾消耗量(≤10mg/L)等指标检测,符合GB 9685食品接触材料卫生标准。
检测流程与质量控制
完整的检测体系应包含原材料入厂检验、生产过程巡检、成品出厂全检三个环节。企业需建立ISO 9001质量管理体系,配备熔融指数仪、电子万能试验机、气相色谱仪等设备,对关键指标如氧化诱导期(OIT≥20min)、碳黑分散度(≤3级)等进行全程监控。第三方检测机构每年应开展监督抽样,确保检测数据的客观性和权威性。
结语
随着环保法规趋严和行业标准升级,聚烯烃注塑包装桶的检测要求正朝着更高精度、更多维度的方向发展。通过科学的检测手段和完善的质量控制体系,不仅能规避渗漏、污染等风险,更能提升产品的市场竞争力和品牌信誉度,为下游行业提供安全可靠的包装解决方案。
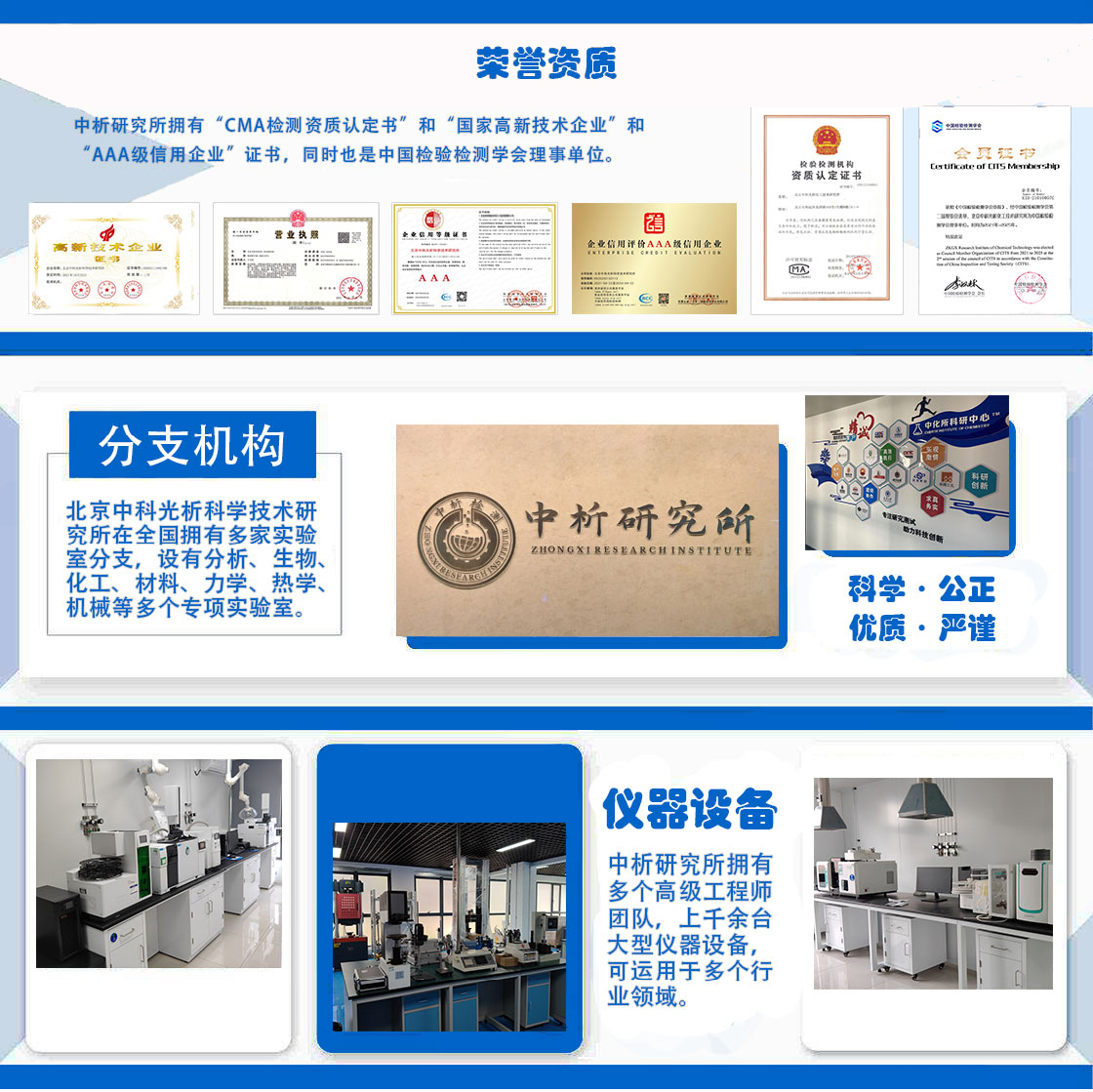
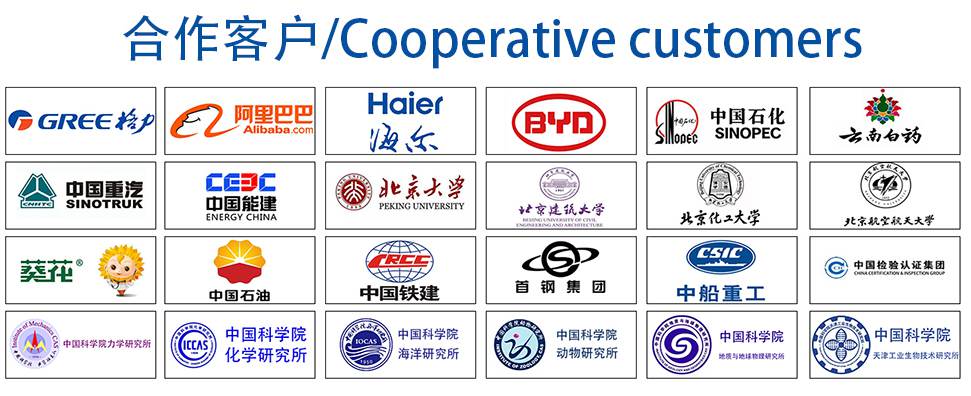