汽车用聚氨酯合成革检测
实验室拥有众多大型仪器及各类分析检测设备,研究所长期与各大企业、高校和科研院所保持合作伙伴关系,始终以科学研究为首任,以客户为中心,不断提高自身综合检测能力和水平,致力于成为全国科学材料研发领域服务平台。
立即咨询汽车用聚氨酯合成革检测的重要性
随着汽车工业对轻量化与环保性要求的提升,聚氨酯合成革因其优异的耐磨性、耐候性和仿真皮质感,已成为汽车座椅、门板、仪表盘等内饰的主流材料。据统计,2022年汽车内饰合成革市场规模已突破50亿美元,其中聚氨酯材质占比达72%。然而,汽车内饰材料需要承受长期机械载荷、温度变化、紫外线辐射等严苛工况,任何性能缺陷都可能引发安全隐患或用户体验问题。
为确保汽车用聚氨酯合成革的全生命周期可靠性,必须建立完整的检测体系。从原材料筛选到成品验收,需通过物理机械性能、环境耐受性、化学安全性等20余项专业检测,严格遵循ISO 3795、SAE J369等国际标准及GB/T 4689等国家强制规范。专业检测不仅能验证材料性能,更能为产品研发提供关键数据支撑。
核心检测项目体系
物理机械性能检测
通过万能材料试验机进行拉伸强度(≥15MPa)、撕裂强度(≥40N/mm)测试,模拟材料在装配和使用中的受力状态。采用Martindale耐磨仪执行10万次摩擦试验,检测表面磨损等级(≥4级)。使用邵氏硬度计测量材料硬度(A型70-90),确保触感舒适性与支撑性的平衡。
环境耐受性检测
在氙灯老化箱中进行1000小时光照老化测试,评估色差(ΔE≤3.5)和表面开裂情况。高温高湿试验(85℃/85%RH,240h)验证材料尺寸稳定性(形变率≤2%)。-40℃至100℃冷热循环测试需通过20次循环无龟裂,确保极端气候下的可靠性。
环保与安全检测
采用GC-MS联用技术检测VOC排放,苯系物含量需<50μg/m³,甲醛释放量≤30mg/kg。依据FMVSS 302标准进行垂直燃烧测试,燃烧速率须<100mm/min。通过皮肤致敏试验(OECD 406)确认材料生物安全性,确保符合ELV指令等环保法规。
功能性验证检测
使用耐刮擦测试仪(1N载荷)进行20次往复划擦,表面不可见明显划痕。耐汗渍测试需模拟人体汗液(PH4.7)浸泡48小时后无变色、无分层。抗静电性能检测要求表面电阻<1×10^9Ω,避免冬季静电吸附灰尘。
全流程质量控制价值
现代汽车制造企业已建立从粒子原料到成品革的全链条检测体系。某合资品牌2023年质量报告显示,通过加强涂层附着力(划格法≥4B级)和耐水解(70℃/95%RH,7天)等专项检测,使内饰件售后投诉率下降37%。定期校准检测设备(如分光测色仪精度±0.1ΔE)、建立检测数据追溯系统,已成为主机厂准入的必备条件。
随着智能座舱概念的普及,汽车用聚氨酯合成革检测正朝着智能化方向发展。采用机器视觉自动识别表面瑕疵,应用大数据分析预测材料老化趋势,这些创新技术将推动检测效率提升40%以上,为汽车内饰材料的品质升级提供更强有力的技术保障。
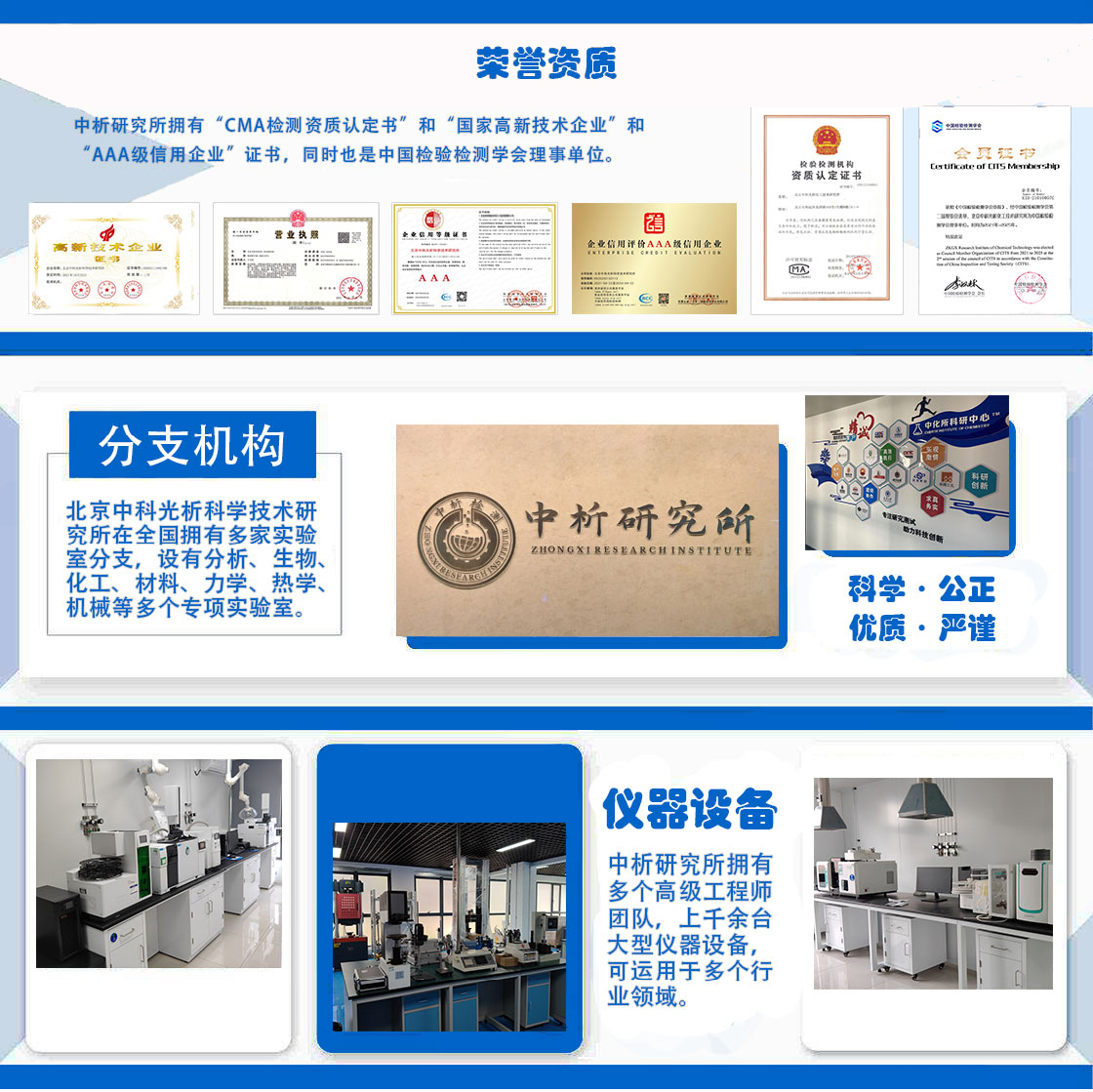
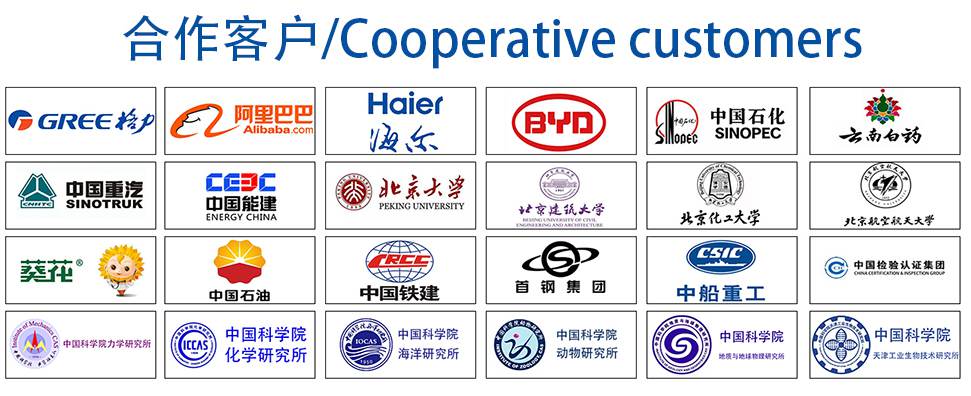