油田原油损耗检测技术体系构建与应用
在油田生产全生命周期中,原油损耗不仅造成直接经济损失,更可能引发环境污染和安全隐患。根据国际能源署统计数据显示,油田平均自然损耗率高达3.5%-5.2%,其中运输储存环节占比超40%。构建科学完善的原油损耗检测体系,已成为现代油田精细化管理的关键环节。通过多维度检测技术融合,能够精准定位损耗节点,为优化生产工艺提供数据支撑。
储运环节动态监测系统
采用高精度质量流量计(±0.1%测量精度)与在线密度计联用技术,实时监控输油管道中的质量流量变化。储罐配备三维激光扫描仪,定期进行液位立体测绘,结合温度补偿算法消除热胀冷缩影响。通过比对进料-出料动态平衡数据,可精确计算储存周期内的挥发损耗量。
生产装置密封性检测
运用红外热像仪(检测灵敏度0.03℃)进行设备表面温度场扫描,结合超声波检漏仪(检测范围20-100kHz)定位微渗漏点。针对阀门、法兰等关键连接部位,采用氦质谱检漏技术(最低检出限1×10⁻⁹ Pa·m³/s),建立全装置密封性评价数据库,年检覆盖率达100%。
逸散排放物定量分析
部署气相色谱-质谱联用系统(GC-MS)在线监测平台,实现对VOCs排放的组分识别和浓度测定。采用开放光路傅里叶变换红外光谱(OP-FTIR)技术,构建500米半径立体监测网络,精确测算无组织排放总量。配套建立排放因子数据库,支持损耗量的物料衡算模型优化。
自动化监测系统集成
整合物联网技术构建智能监测网络,部署500+个智能传感器节点,实现数据采集频率从小时级提升至分钟级。开发数字孪生平台,将实时监测数据与三维地质模型动态耦合,通过机器学习算法预测损耗趋势。系统具备自动预警功能,异常工况响应时间缩短至15分钟内。
通过构建"过程监测-泄漏检测-排放分析-智能管控"四位一体的检测体系,某大型油田应用后年损耗率从2.8%降至1.2%,相当于年挽回经济损失超2.3亿元。实践表明,系统化的检测技术应用可使设备检修效率提升40%,VOCs减排量达65%,为油田绿色可持续发展提供技术保障。
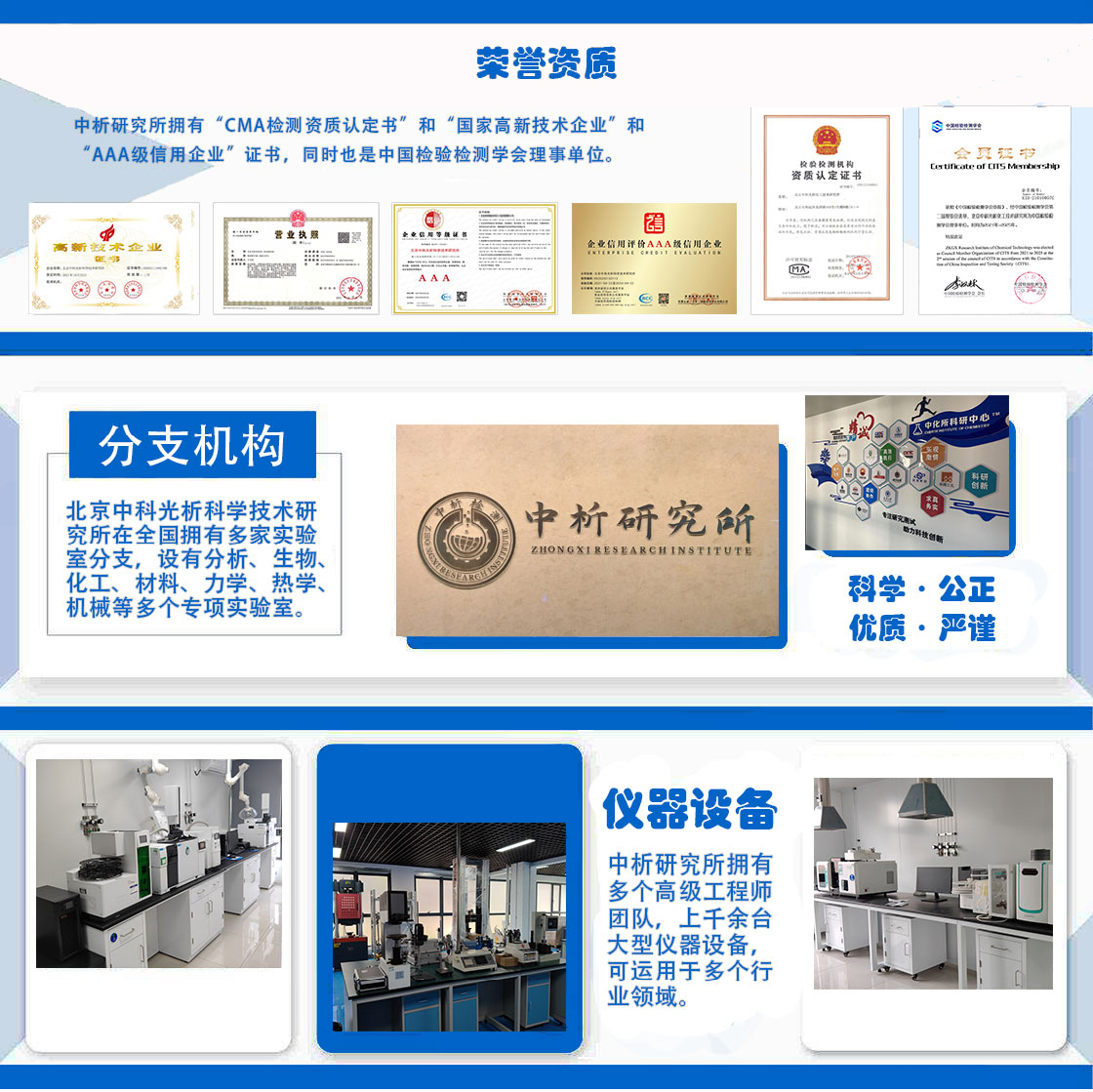
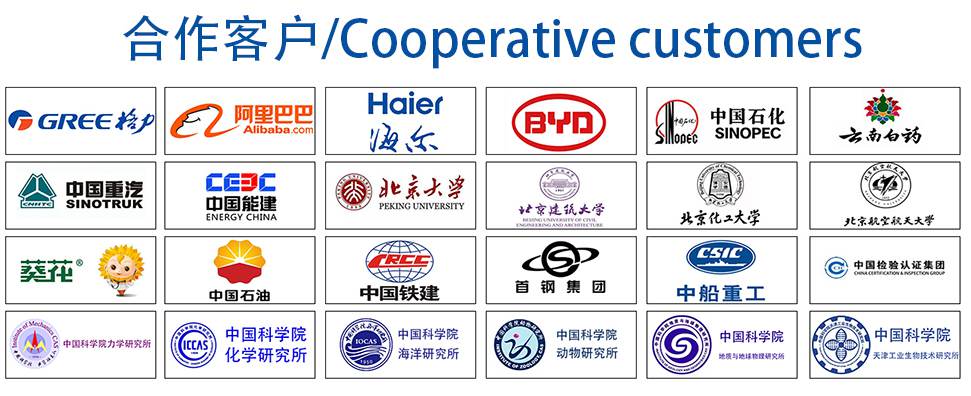