机械采油系统、油田注水系统、集输系统及机泵节能监测与测试检测
在油田生产全流程中,机械采油系统、油田注水系统、集输系统及配套机泵设备构成了能源消耗的主体单元。随着"双碳"目标的深入推进,开展系统性节能监测与测试检测已成为提升油气田能效水平的核心技术手段。通过专业化的检测评估,不仅能精准定位能耗异常点,更能为设备优化运行、工艺参数调整提供科学依据,最终实现年节能率5%-15%的技术经济目标。本文重点针对四大系统的关键检测项目展开技术解析。
一、机械采油系统检测项目
1. 抽油机平衡度测试:采用智能电参仪连续采集电流波形,通过峰谷差值法计算平衡度指标。当平衡度偏差超过±15%时,需调整平衡块配置,可降低系统能耗8%-12%。
2. 井下泵效分析:应用示功图诊断技术,结合液面回声仪数据,计算有效冲程比与容积效率。重点检测气体影响、泵漏失等问题,泵效每提升1%,单井日节电可达20kWh。
3. 传动系统效率测试:对皮带传动、齿轮箱等环节进行机械效率测试,采用红外热像仪监测轴承温升,发现传动效率低于92%时需立即检修。
二、油田注水系统检测项目
1. 注水泵组效率测试:运用流量-压力联测装置,绘制泵组特性曲线,计算机组运行效率。当效率低于设计值5个百分点时,需检查叶轮磨损或流道结垢情况。
2. 管网压损分析:通过分布式压力监测系统,建立管网压力分布模型,重点检测滤网、阀门等局部阻力部件,压损每降低0.5MPa可节省注水能耗7%。
3. 注水水质能效影响检测:开展悬浮物含量、含油量、SRB菌群检测,验证水质对管效和泵效的影响系数,建立水质-能耗关联模型。
三、油气集输系统检测项目
1. 管道保温效能评估:采用表面温度法检测保温层热损失,结合气候补偿模型计算全年热损失量。当表面热流密度超过50W/m²时需进行保温改造。
2. 油气混输泵能效测试:应用多相流量计进行气液比动态监测,绘制不同工况下的泵效曲线,优化转速控制策略可提升能效3-5个百分点。
3. 压力容器散热检测:使用红外热成像仪扫描分离器、储罐等设备表面温度场,建立设备散热数据库,年散热损失超过设计值20%需启动节能改造。
四、机泵设备专项检测
1. 电机能效等级验证:执行GB/T 1032标准测试,通过空载试验、负载试验获取实际效率值,对比国家能效标准判定节能潜力。
2. 变频器谐波检测:使用电能质量分析仪检测THD值,当电流谐波畸变率超过8%时需加装滤波装置,避免额外能耗损失。
3. 润滑系统状态检测:通过油液光谱分析检测磨粒成分,结合粘度测试数据,建立润滑状态与机械效率的量化关系模型。
通过实施上述检测项目,企业可建立覆盖"采-注-输"全流程的能耗监测体系。建议配套建设数字化能管平台,将检测数据与生产控制系统联动,实现能耗指标的动态优化控制。实践表明,系统化检测与持续改进可使油田综合能耗降低10%-18%,具有显著的经济效益和环保价值。
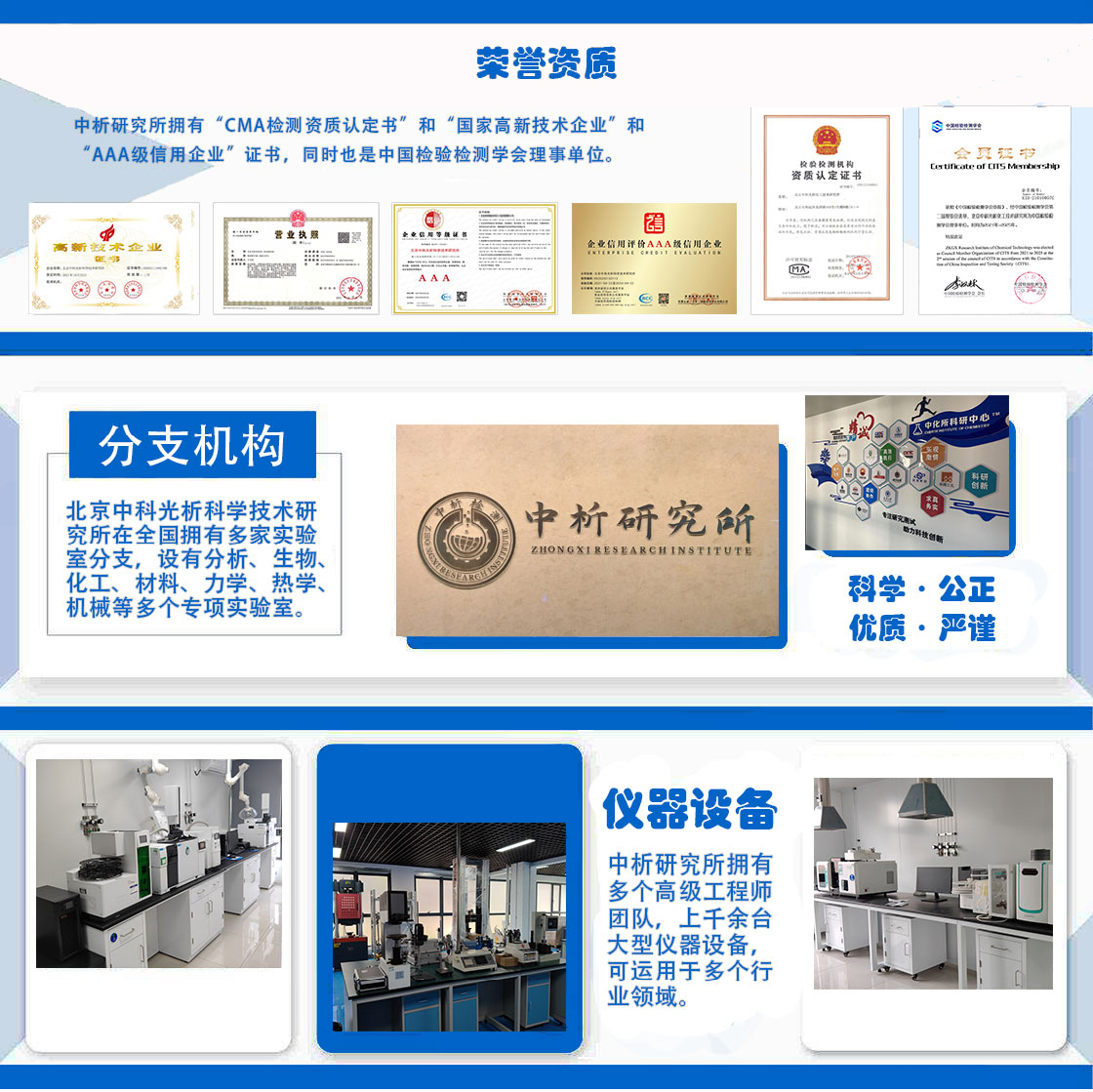
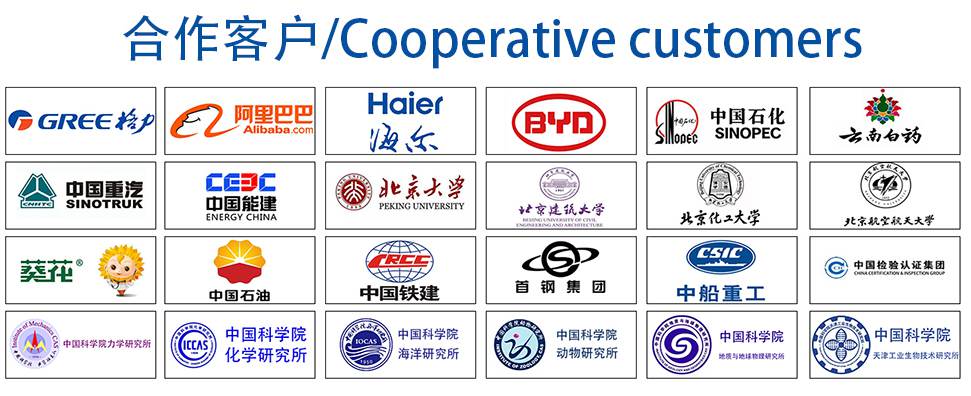