阻火器检测的重要性与核心目标
阻火器作为工业装置中防止火焰传播的关键安全设备,广泛应用于石油化工、天然气输送、储罐系统等易燃易爆场所。其核心功能是通过金属波纹板、陶瓷蜂窝等特殊结构阻断火焰蔓延并维持气体流通。为确保设备在紧急工况下的可靠性,定期阻火器检测成为安全生产管理中不可或缺的环节。检测不仅涉及外观状态评估,更需验证阻爆性能、耐压强度等关键指标,以消除因腐蚀、堵塞或机械损伤引发的安全隐患。
阻火器检测核心项目与标准规范
1. 结构与外观完整性检测
通过目视检查与精密测量仪器,重点验证壳体是否存在裂纹、变形,阻火芯体是否完整无缺损,法兰密封面平整度是否符合GB/T 13347标准要求。使用内窥镜探查内部积碳或异物沉积情况,沉积物厚度超过芯体通道直径20%时需立即清洁。
2. 阻火性能验证试验
依据API 2210标准,在防爆实验室模拟真实工况进行火焰穿透试验。采用丙烷/空气混合气体作为测试介质,通过高速摄像与压力传感器记录火焰传播速度、压力波动数据。合格判定标准为:连续10次试验中阻火器均能有效阻断火焰且未发生结构性破坏。
3. 压力降与流通能力测试
使用差压变送器测量气体通过阻火器前后的压力差值,对比出厂参数验证流通效率。根据ISO 16852规定,在最大设计流量下,压力损失不应超过初始值的15%。同步检测不同流量工况下的阻力特性曲线,确保设备在全流量范围内满足工艺需求。
特殊环境适应性检测要求
针对海洋平台、高寒地区等特殊应用场景,需增加盐雾腐蚀试验(ASTM B117标准)、低温冲击测试(-40℃环境持续48小时)以及振动疲劳测试(模拟5年使用周期的机械振动负荷)。检测后需复核阻火芯体结构稳定性与密封性能,确保极端条件下的防护可靠性。
检测周期与结果处理规范
常规工业环境建议每12个月进行定期检测,腐蚀性环境缩短至6个月。检测中发现芯体破损率超过5%、壳体壁厚减薄量达10%或压力降超标时,必须强制更换阻火单元。所有检测数据需录入设备管理台账,并依据NB/T 47003.1标准出具分级评估报告,作为设备维护或报废的技术依据。
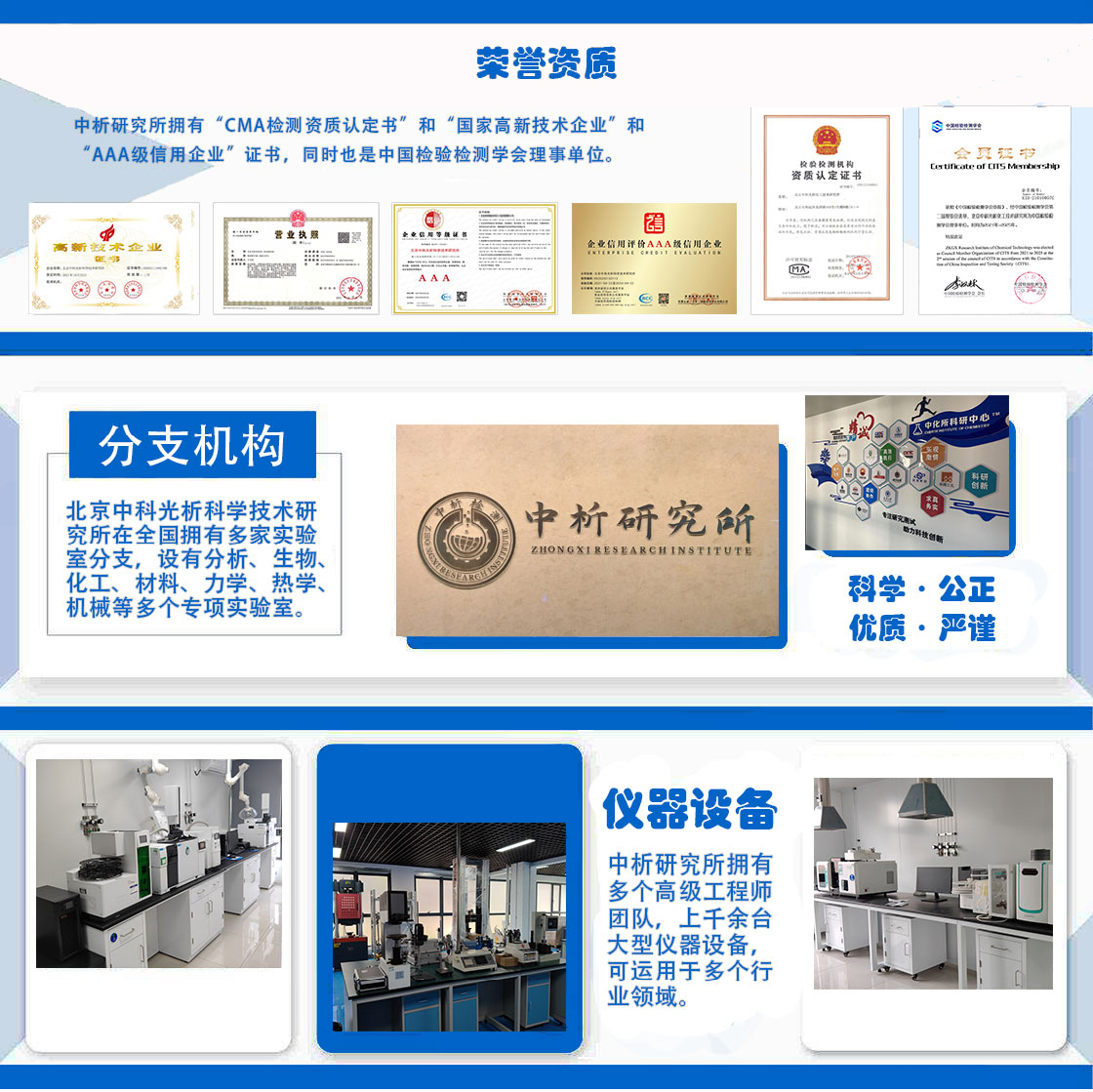
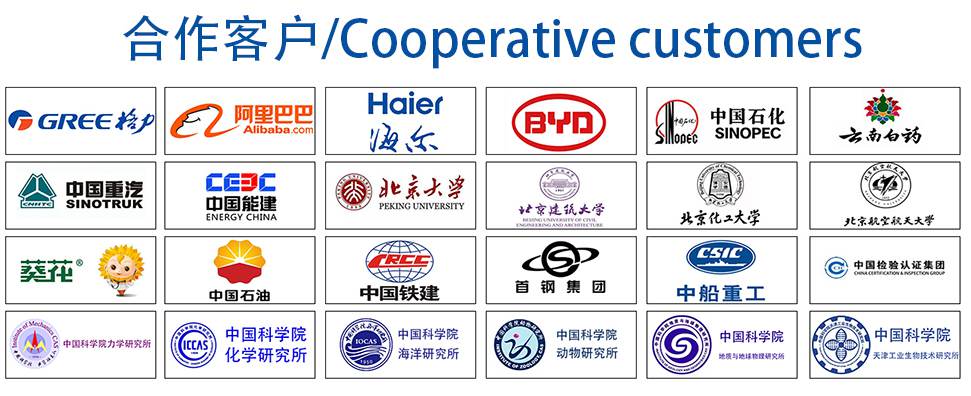