工业循环冷却水检测的重要性
工业循环冷却水系统是石化、电力、冶金等行业的核心配套单元,其水质状况直接影响设备运行效率与使用寿命。由于水中杂质、微生物及化学添加剂的动态变化,定期开展系统化检测成为预防管道腐蚀、结垢和生物黏泥堵塞的关键手段。通过精准的检测数据,企业可优化水处理方案,降低能耗成本约15%-30%,同时延长设备大修周期3-5年。当前国内约67%的工业设备故障与水系统管理失当存在关联,凸显了专业化检测的必要性。
核心检测项目解析
1. 基础理化指标检测
采用电化学法测定pH值(GB/T 6920),控制范围6.8-9.5;通过电导率仪检测含盐量(ASTM D1125),要求≤3000 μS/cm;采用EDTA滴定法测定总硬度(GB/T 7477),钙镁离子总量需<450 mg/L。这些指标超标会加速换热器结垢,降低热传导效率达40%以上。
2. 腐蚀控制参数检测
使用挂片失重法(GB/T 18175)测定碳钢腐蚀率,要求≤0.075 mm/a;铜合金腐蚀率需<0.005 mm/a。应用分光光度法检测缓蚀剂浓度(如HEDP、PBTCA),浓度波动应控制在±5%范围内。现场实践表明,精准的缓蚀剂投加可使管道寿命延长2.8倍。
3. 微生物污染监测
采用ATP生物荧光法快速检测异养菌总数(ASTM D4012),要求<1×10⁵ CFU/mL;每周进行硫酸盐还原菌(SRB)培养检测(API RP38),控制值<100 CFU/mL。某化工厂案例显示,生物黏泥导致的换热效率下降每年造成直接损失超200万元。
4. 结垢趋势分析
通过朗格利尔指数(LSI)和雷兹纳稳定指数(RSI)计算结垢倾向,结合XRD分析沉积物成分。当LSI>0.8时需调整阻垢剂配方,阻垢效率应达到90%以上。在线监测系统可实现CaCO₃过饱和度的实时预警,提前48小时预判结垢风险。
检测技术创新方向
新型快速检测装备集成光谱分析、微流控芯片技术,将传统3天的检测周期缩短至2小时。物联网水质监测平台可实现16项参数的远程传输与智能诊断,异常数据识别准确率达98.7%。2023年行业报告显示,采用智能检测系统的企业运维成本降低21%,非计划停机减少63%。
通过建立覆盖预处理、运行监控、效果评估的闭环检测体系,企业可构建科学的循环水管理系统。建议每季度开展全面检测,关键参数实施在线监测,结合大数据分析优化水处理药剂投加策略,最终实现节水15%、节能20%的绿色运行目标。
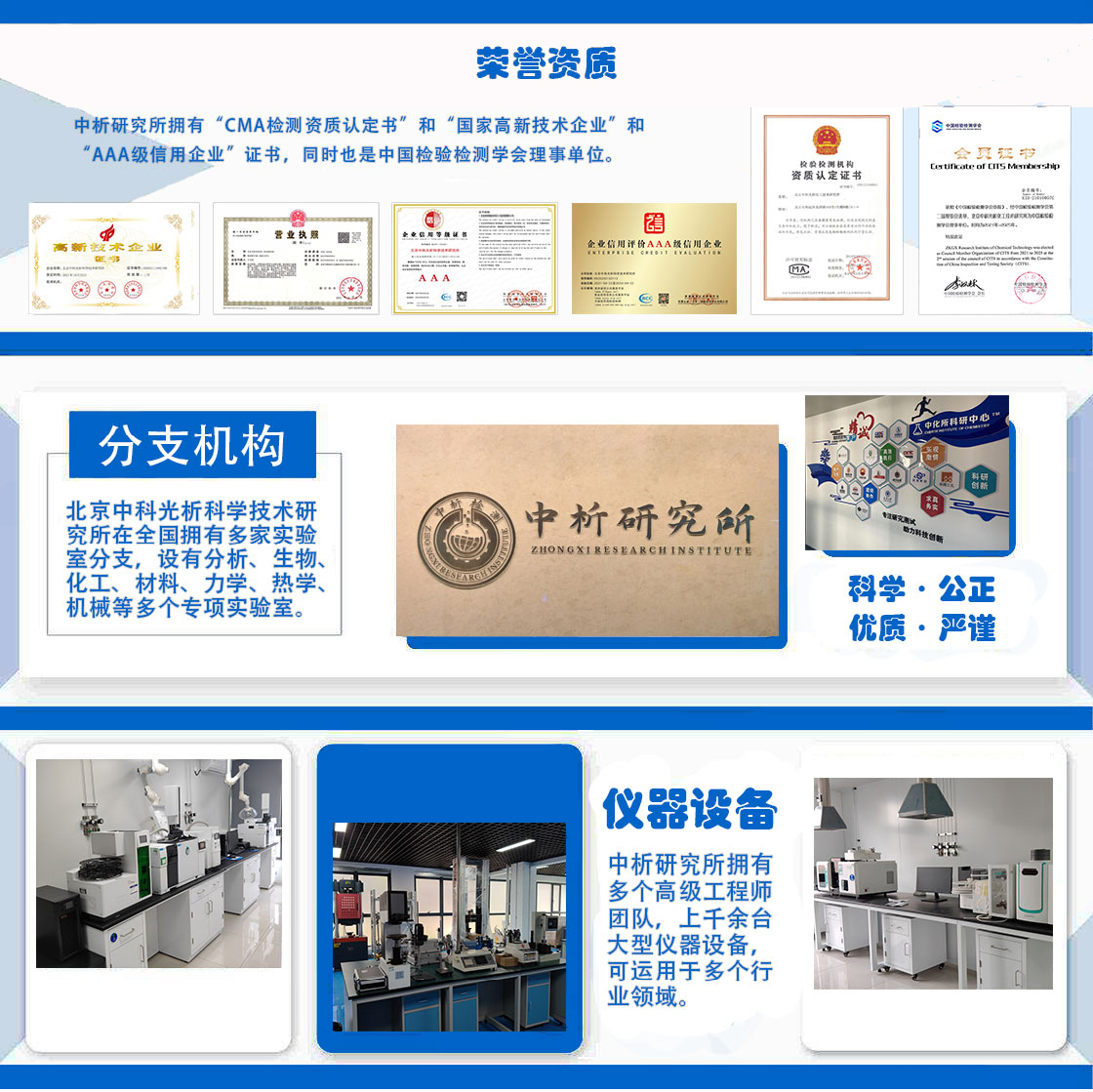
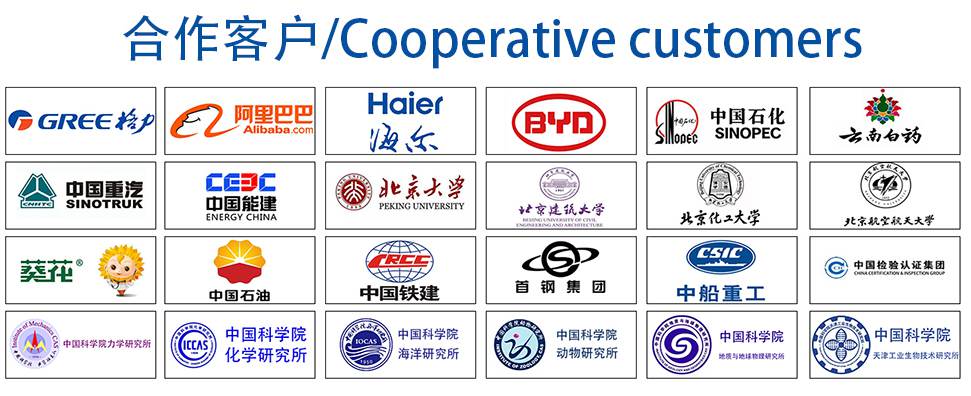