锂离子蓄电池及蓄电池组检测的重要性及核心项目解析
随着新能源产业的快速发展,锂离子蓄电池作为电动汽车、储能系统及消费电子领域的核心动力源,其安全性、稳定性和循环寿命备受关注。据行业统计,2023年锂离子电池市场规模已突破1200亿美元,但与之相关的质量事故发生率仍呈现上升趋势。在此背景下,专业的锂离子蓄电池及蓄电池组检测已成为保障产品性能、预防安全隐患的关键环节,检测结果直接影响着终端产品的市场竞争力和用户信任度。
核心检测项目体系
1. 电性能测试
通过充放电测试系统模拟实际使用场景,精确测量容量保持率(循环500次后≥80%)、能量密度(≥150Wh/kg)、内阻值(<30mΩ)等关键指标。采用恒流恒压(CC-CV)充电法和脉冲放电法评估电池动态响应特性,确保电池组在快速充放电条件下的稳定性。
2. 安全性能测试
依据GB 31241-2022强制标准,执行包括过充/过放测试(1.5倍额定电压)、短路试验(<5mΩ)、针刺试验(钢针直径3mm)等极端工况模拟。特别针对热失控传播特性,要求电池组在单体故障时具备1小时以上的热扩散防护能力。
3. 环境适应性测试
在温度冲击箱中执行-40℃至85℃循环测试,验证电解液低温结晶和高温分解特性。85%RH高湿环境下持续720小时,检测壳体密封性和极片腐蚀状况。振动测试模拟车辆实际工况,施加频率5-200Hz的随机振动,持续3小时无结构损伤。
4. 机械性能测试
5. 寿命评估测试
通过加速老化试验台,在45℃高温环境下进行1C倍率循环测试,建立容量衰减模型。采用电化学阻抗谱(EIS)分析界面SEI膜生长规律,预测电池组寿命衰减拐点。对于储能系统用电池,需满足>6000次循环(80%DoD)的使用要求。
检测技术发展趋势
随着AI诊断技术的应用,最新检测设备已实现云端数据比对和故障预判功能。X射线断层扫描(CT)技术可无损检测极片对齐度,精度达到微米级。国际电工委员会(IEC)最新发布的62660-3标准,已将硅基负极材料的膨胀率检测纳入强制项目,推动检测技术持续升级。
专业的锂离子蓄电池检测体系,不仅需要覆盖从单体到模组的全链条测试,更要结合应用场景建立差异化的评价标准。随着固态电池等新技术的产业化推进,检测项目将向着更高精度、更严苛条件的方向发展,为新能源行业的高质量发展提供技术保障。
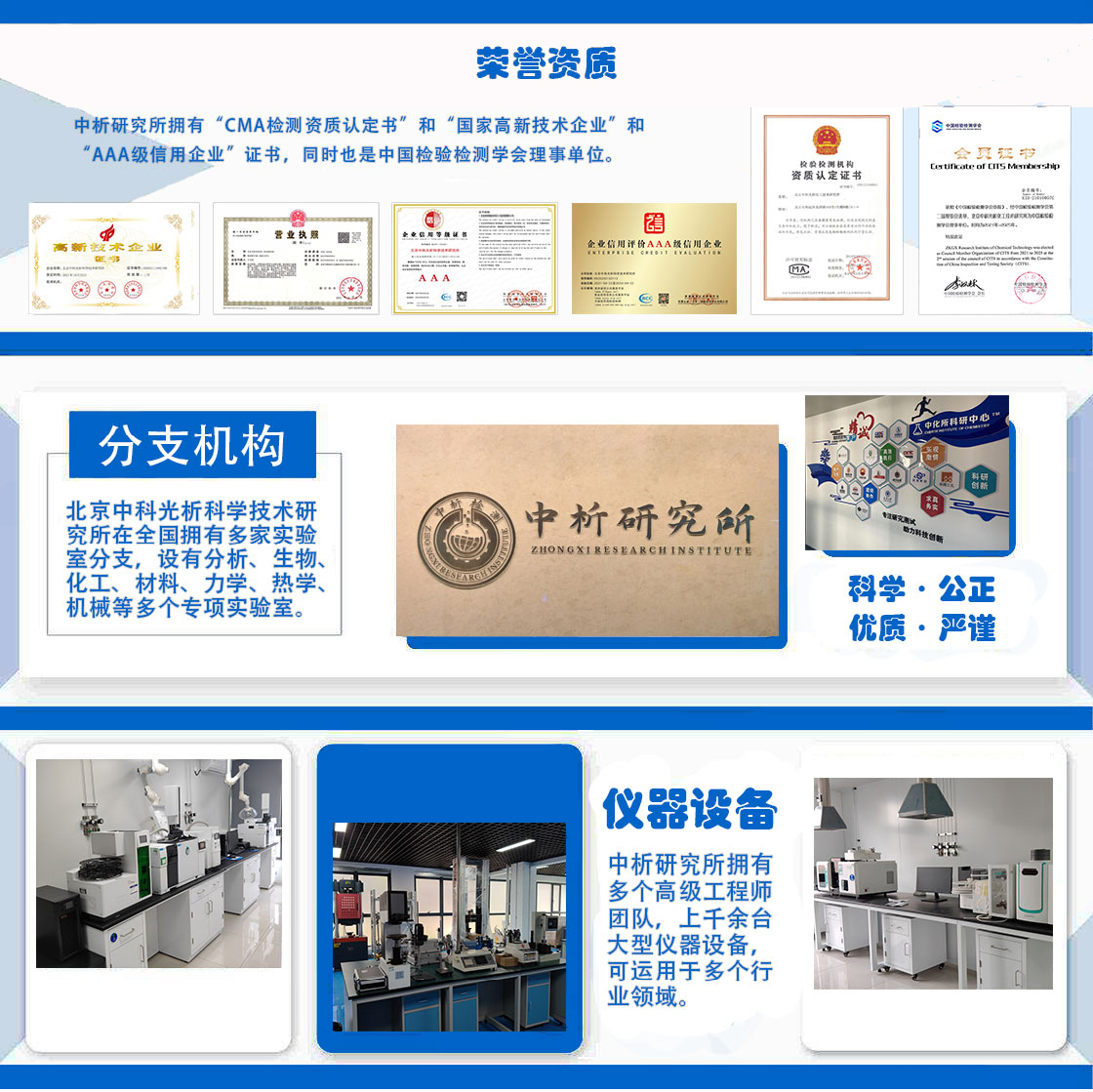
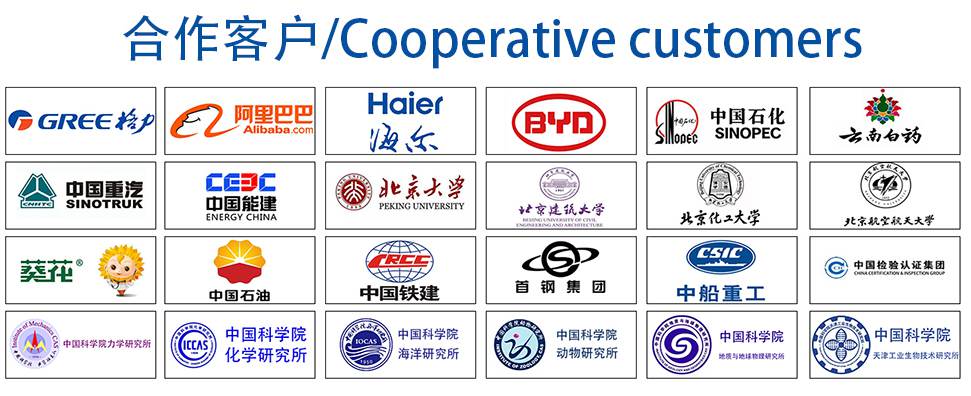