固定电容器检测的重要性与应用场景
固定电容器作为电子电路中的核心被动元件,广泛应用于电源滤波、信号耦合、能量存储等领域。其性能直接影响设备稳定性与安全性,因此检测工作成为生产和使用环节的关键步骤。根据IEC 60384、GB/T 6346等国际国内标准,完整的固定电容器检测体系包含物理特性、电气性能、环境适应性三大类共20余项指标,确保元件在全生命周期内满足设计要求。
核心检测项目与技术指标
1. 基础电气参数检测
使用LCR测试仪在1kHz标准频率下测量标称电容量,误差需控制在±5%以内(通用型)或±1%(精密型)。直流耐压测试采用逐步升压法,陶瓷电容需承受2.5倍额定电压60秒无击穿,电解电容则要求1.5倍额定电压测试。
2. 介质性能评估
绝缘电阻测试使用500V兆欧表,铝电解电容绝缘值需>1000MΩ·μF,薄膜电容要求>50000MΩ。损耗角正切(tanδ)检测通过高频电桥实现,C0G材质MLCC应≤0.15%,X7R型≤2.5%。
3. 环境适应性验证
温度循环测试包括-55℃~+125℃范围内5次循环,容量变化率应<±5%。85℃/85%RH高温高湿测试1000小时后,漏电流增加不得超过初始值2倍。机械振动测试执行10~2000Hz扫频振动,参数漂移需<3%。
4. 结构完整性检查
采用X射线检测仪观察内部结构,要求电极对齐度偏差<10μm。密封性测试将电解电容浸入85℃防爆电解液中,施加额定电压2小时无泄漏。引脚强度需承受3N拉力60秒无松动。
检测设备与标准体系
现代化检测实验室配备TH2817D自动分选机、Chroma 19032耐压测试仪、ESPEC温箱等设备,检测流程符合ISO/IEC 17025体系要求。测试数据需记录批次号、测试时间、环境参数,建立完整的质量追溯系统。
行业发展趋势与检测技术革新
随着车规级AEC-Q200认证要求普及,检测项目新增2000小时高温反偏(HTRB)试验。第三代半导体应用推动100kHz高频损耗检测成为标配,纳米级X射线CT技术可实现3μm级内部缺陷检测,AI视觉系统使外观检测效率提升300%。
通过系统化的检测流程,固定电容器的失效率可从常规0.5%降至50ppm级别,为5G基站、新能源汽车等高端应用提供可靠保障。建议生产企业建立从原材料检验到成品测试的全流程质控体系,定期参与ILAC互认实验室的能力验证。
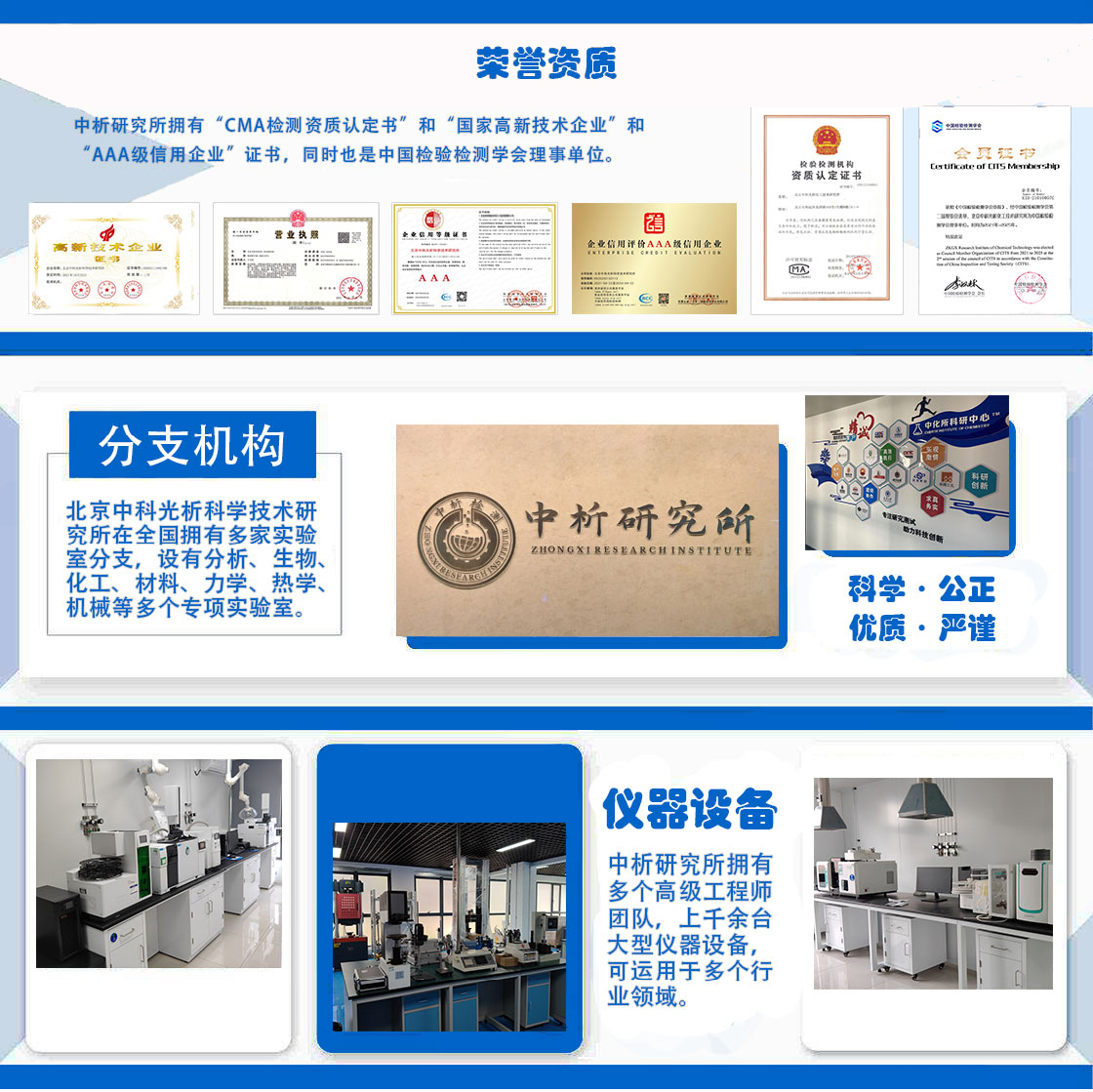
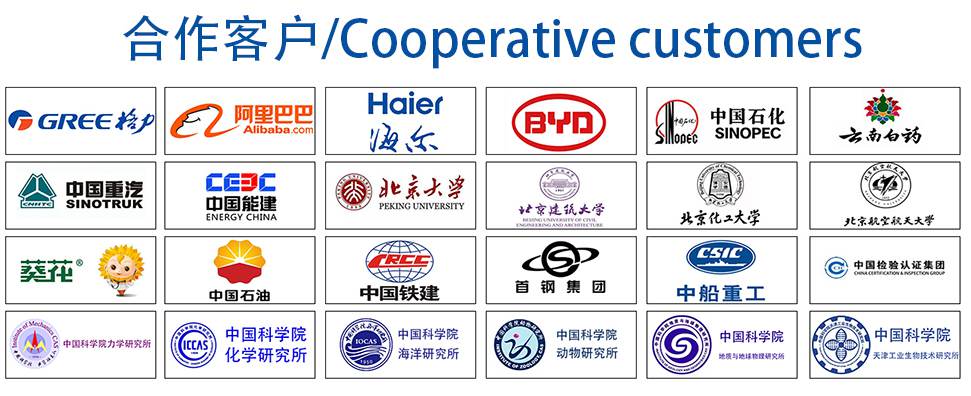