熔断体与熔断器检测的重要性
熔断体和熔断器作为电路保护系统的核心元件,在电力设备、工业控制系统及家用电器中承担着过载和短路保护的关键作用。随着电气设备功率密度不断提升和用电环境复杂化,相关产品的质量检测已成为保障电力系统安全运行的重要环节。专业检测机构通过系统化的测试流程,可验证熔断器分断能力、时间-电流特性、温升性能等20余项关键指标,确保其符合IEC 60269、GB 13539等国际国内标准要求。
核心检测项目解析
1. 电气性能测试
该测试涵盖额定电流验证、分断能力测试、电压降测量等核心参数。采用可编程负载系统模拟不同故障电流场景,精确记录熔断时间,确保在标称分断能力范围内能可靠切断电路。其中高压熔断器需额外进行工频耐压试验,验证10kV级产品能承受42kV/1min的耐压考验。
2. 机械结构检测
通过三维测量仪对熔断体尺寸进行0.01mm级精度检测,重点核查接触端子的配合公差。对熔管类产品进行200N轴向拉力测试,模拟长期振动环境下的结构稳定性。跌落试验采用1.2m自由落体冲击,验证产品外壳防护等级是否符合IP20标准。
3. 环境适应性试验
在温湿度交变箱中进行-40℃至+125℃的极限温度循环测试,评估材料热膨胀系数匹配性。盐雾试验按照GB/T 2423.17标准进行96小时连续喷雾,检测金属部件防腐性能。振动测试模拟运输工况,进行XYZ三轴各2小时扫频振动。
4. 安全防护验证
建立电弧能量数学模型,通过高速摄像系统(100000帧/s)捕捉分断过程的电弧特性。采用红外热像仪监测熔断过程中外壳表面温升,确保最高温度不超过125℃。绝缘电阻测试要求产品在500VDC下保持>100MΩ的阻值。
5. 寿命与可靠性评估
设计加速老化试验方案,通过2000次通断循环验证机械寿命。建立蒙特卡洛模型预测不同负载率下的失效率,对汽车用熔断器还需进行机械冲击(50g/11ms)和随机振动(0.04g²/Hz)专项测试。
检测技术发展趋势
当前检测领域正朝着智能化方向发展,基于数字孪生技术的虚拟测试系统可将检测周期缩短40%。采用AI图像识别技术可实时分析熔断后灭弧室状态,X射线断层扫描(CT)技术实现非破坏性内部结构检测。这些创新方法显著提升了检测精度和效率,为新型半导体熔断器的开发提供有力支撑。
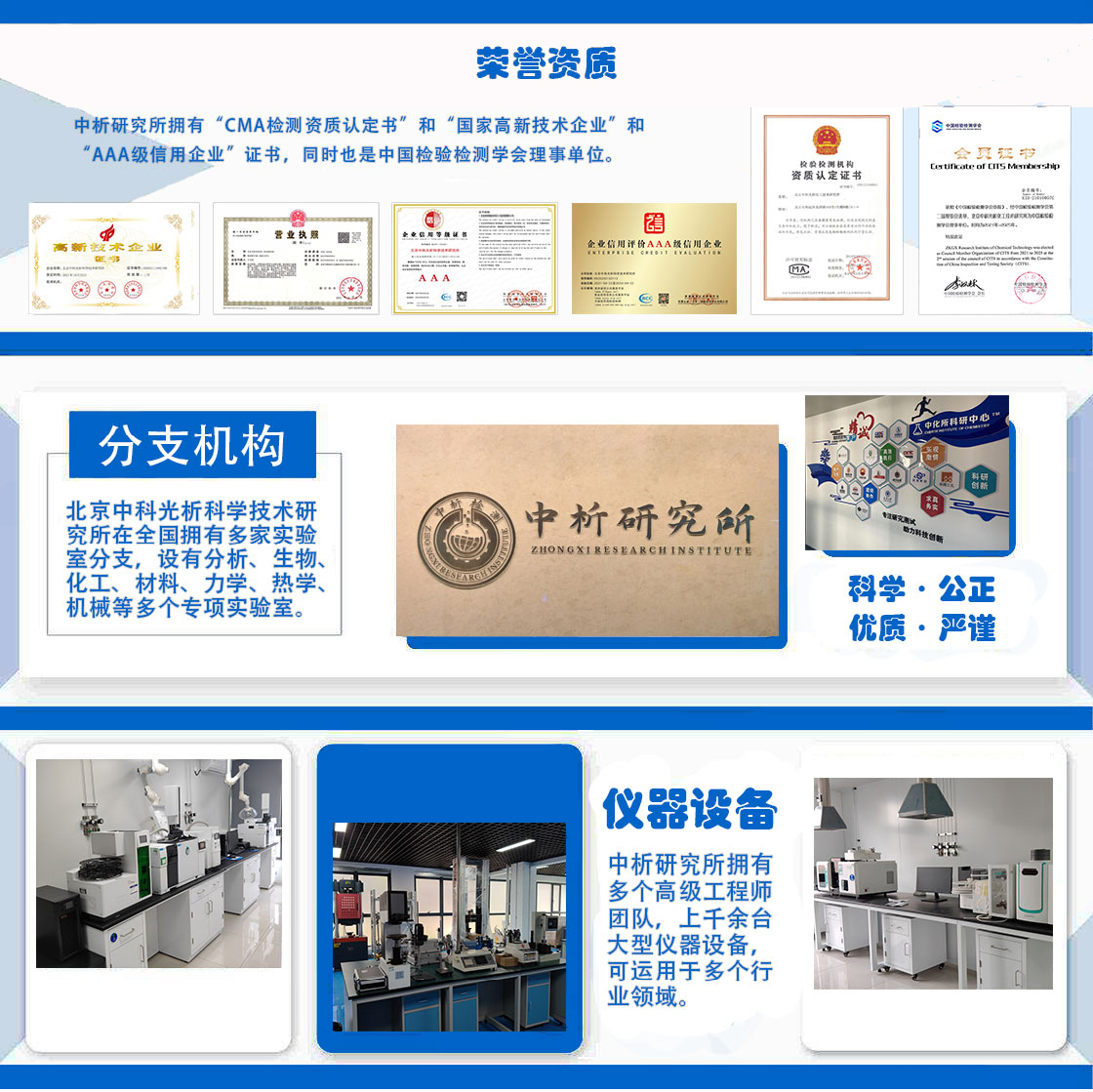
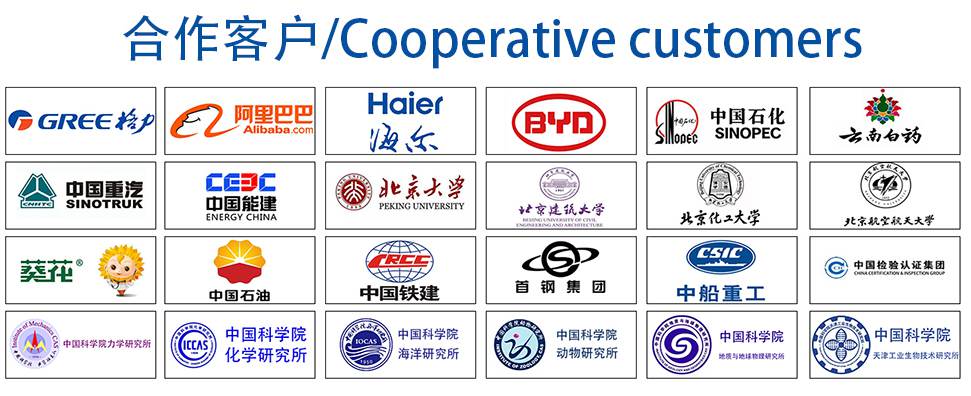