集成电路检测:确保芯片性能与可靠性的关键环节
集成电路作为现代电子设备的核心组件,其性能直接决定了产品的质量和市场竞争力。随着制程工艺进入5纳米乃至3纳米时代,芯片内部结构复杂度呈指数级增长,这对检测技术提出了前所未有的挑战。集成电路检测贯穿于设计验证、晶圆制造、封装测试等全生命周期,涉及物理特性分析、电气性能验证、功能完整性测试等二十余项关键技术指标。
在半导体产业链中,检测环节的成本占比高达25%-30%。领先的检测机构采用X射线断层扫描、纳米探针、热成像等尖端技术,可精准定位0.1μm级的结构缺陷。特别是在汽车电子和医疗设备领域,芯片失效率要求低于0.1ppm,这需要建立多维度检测体系来保障产品可靠性。
核心检测项目体系
1. 结构完整性检测
采用扫描电子显微镜(SEM)和聚焦离子束(FIB)技术,对10nm以下制程的晶体管结构进行三维重建。通过对比设计版图与实际结构的匹配度,可发现0.01%的线宽偏差。最新TEM透射电镜已能实现原子级成像精度,可有效识别FinFET结构中的晶格缺陷。
2. 电气特性验证
在-55℃至150℃温区内,使用精密参数分析仪(PPA)执行DC/AC参数测试。关键指标包括:阈值电压漂移量≤3mV、漏电流波动控制在0.1nA级别。对于射频芯片,需在40GHz高频下测试S参数,确保阻抗匹配误差小于0.5dB。
3. 功能完整性测试
依托ATE自动测试设备构建百万级测试向量,覆盖99.99%的逻辑路径。采用IDDQ测试法检测静态电流异常,配合BIST内建自测试机制,可将测试覆盖率提升至6σ水平。齐全的可测试性设计(DFT)使故障检测率突破99.999%。
4. 可靠性加速试验
执行HTOL(高温寿命试验)、EM(电迁移测试)、HALT(高加速寿命试验)等严苛环境模拟。典型条件包括:150℃/85%RH环境下持续工作1000小时,动态电压波动±20%的电源完整性测试,确保芯片MTBF达到10^9小时等级。
前沿检测技术演进
第三代半导体检测引入太赫兹波成像技术,可非破坏性检测GaN材料界面态密度。量子点标记法在故障定位中实现纳米级空间分辨率,AI驱动的异常检测算法将误判率降低至0.001%。2023年推出的光学光热检测(OCT)系统,可在1秒内完成10^6个接触点的阻抗测量。
随着异构集成技术的发展,3D封装检测需求激增。TSV硅通孔检测精度要求达到±0.15μm,混合键合界面的空洞检测需识别0.5μm³的微观缺陷。行业正在建立新的检测标准体系,以应对chiplet架构带来的多维检测挑战。
质量管控体系构建
完善的检测体系需要整合SPC统计过程控制、FMEA失效模式分析、6σ质量管理等方法。建立从晶圆允收测试(WAT)到最终封装测试(FT)的全流程数据追溯系统,通过大数据分析实现工艺参数优化。领先企业已将检测数据与AI模型深度耦合,实现实时缺陷预测准确率>98%。
在化供应链背景下,检测认证体系需要满足JEDEC、AEC-Q100、ISO 26262等多重标准。特别是汽车电子芯片必须通过Grade 0级认证,保证在-40℃至150℃环境下15年零故障运行。这要求检测方案具备跨温度、多应力耦合的复杂环境模拟能力。
集成电路检测技术的持续创新,正在重塑半导体产业的质量基准。从纳米级结构解析到系统级功能验证,检测体系已发展成为融合光学、电子、材料、算法的交叉学科。未来,随着量子传感技术和AI诊断平台的成熟,检测精度和效率将实现量级突破,为摩尔定律的延续提供关键保障。
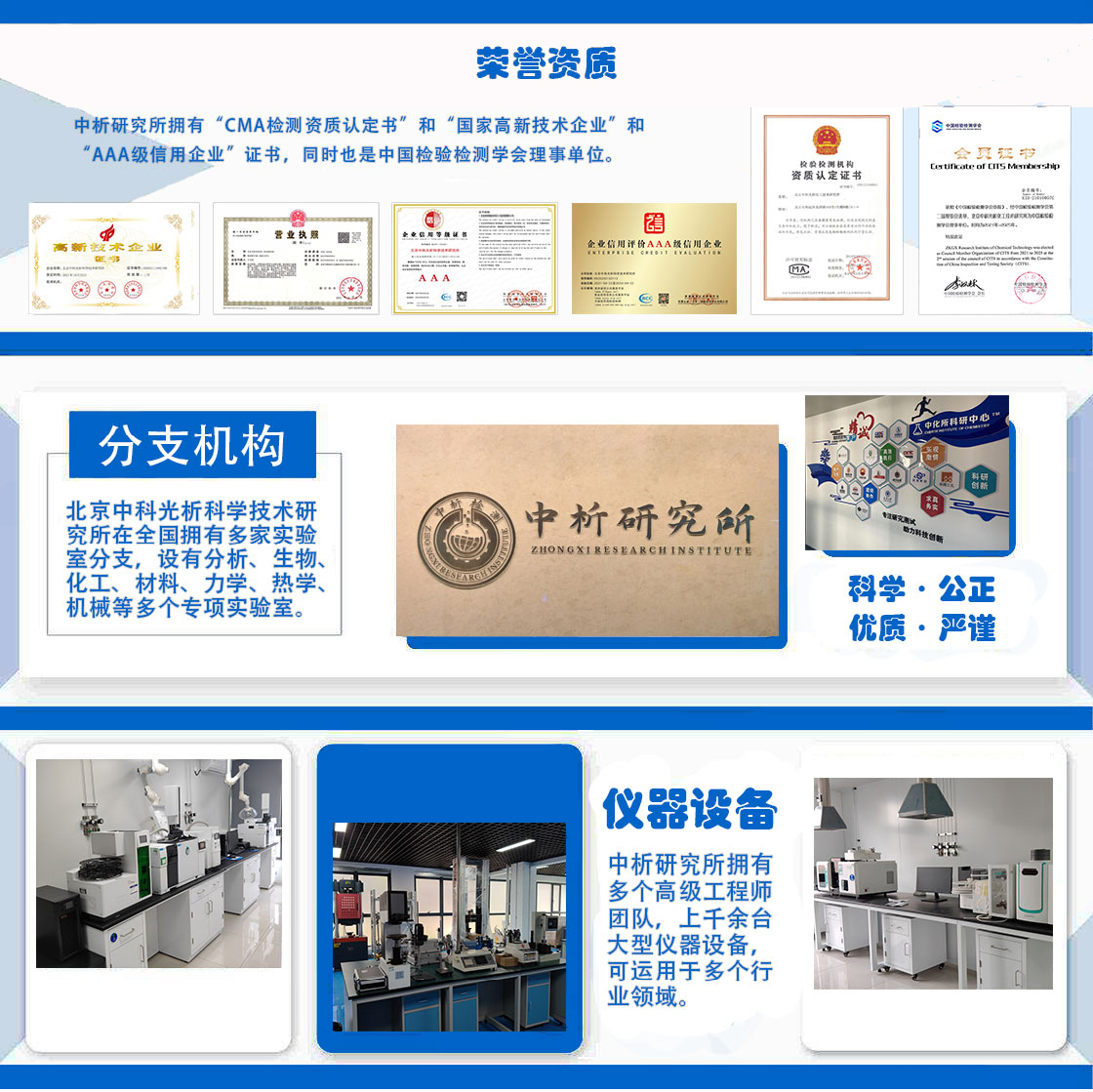
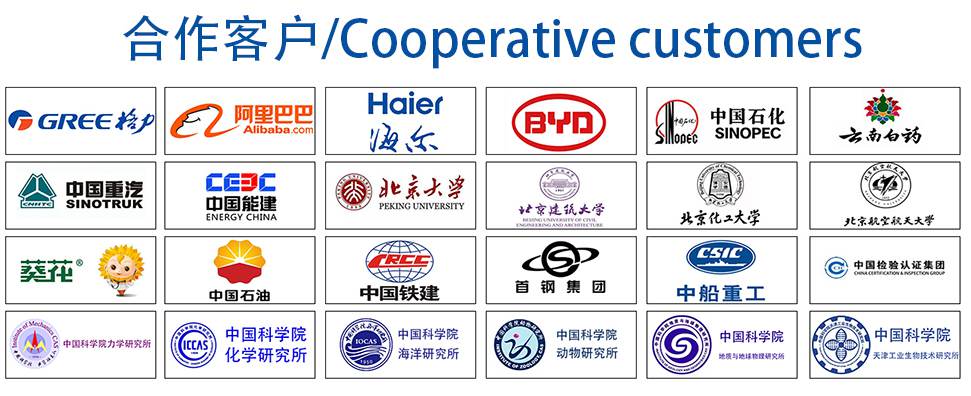