粉末材料洛氏硬度试验检测
粉末材料洛氏硬度试验检测的背景与意义
在现代工业中,粉末冶金技术已经被广泛应用于制造各种复杂形状以及具有特殊性能的材料和零部件。随着粉末材料应用范围的不断扩大,对其性能检测的需求也在不断增加,其中洛氏硬度作为一种常见的硬度检测方法,受到了广泛的关注。洛氏硬度检测能够快速、准确地评估材料的硬度特性,这对于生产过程中的质量控制以及产品的性能优化具有重要意义。
粉末材料的性能受多种因素影响,包括粉末粒度、成型压力、烧结温度和时间等。这些因素不仅影响材料的致密性和强度,还直接决定了材料的硬度。与传统的实心材料不同,粉末材料在硬度测试中可能表现出更为复杂的特性,因此,针对粉末材料进行洛氏硬度试验检测有助于更好地理解其结构与性能之间的关系,从而指导生产工艺的优化。
洛氏硬度试验的基本原理
洛氏硬度试验是一种压入式硬度测试方法,通过测量一个硬质压头在样品表面产生压痕的深度来评定材料的硬度。试验过程分为两个阶段:首先,试验力(初始载荷)作用于材料以消除表面粗糙度的影响;然后,在初始载荷的基础上,施加一个主载荷以形成永久性压痕。在去除主载荷后,保留初始载荷并测量压痕的深度。根据压痕深度,使用洛氏硬度标尺转化为硬度值。
洛氏硬度标尺多种多样,常用的标尺包括A、B、C标尺等,其中标尺的选择主要取决于材料的性质和硬度范围。对于粉末材料的检测,通常需要考虑其独特的微观结构和压缩特性,选择合适的压头和载荷组合,以便得到准确的硬度测量结果。
粉末材料洛氏硬度试验的挑战
检测粉末材料洛氏硬度的过程中,面临着许多挑战。首先,粉末材料通常具有多孔结构,这使得在压入时产生的塑性变形和弹性恢复行为与密实材料有所不同。此外,材料内部的孔隙可能导致压痕形状和深度不均匀,从而影响测量结果的稳定性和可重复性。
其次,粉末材料在制样和测试过程中可能受到环境条件的影响,如湿度和温度的变化,可能导致材料性能的不稳定。因此,在进行洛氏硬度试验时需要严格控制试验环境,以减少外部因素对硬度值的影响。同时,还需要针对不同类型的粉末材料,研究适合的制样方法,以减少制样引入的误差。
粉末材料洛氏硬度试验的技术要点
为了确保粉末材料洛氏硬度试验的准确性和可靠性,需要关注以下几个技术要点:
制样技术:选择合适的成型方法以获得均匀的试样密度,同时确保试样表面的平整度和光洁度,以消除表面粗糙度对硬度测量的影响。烧结工艺的优化也非常重要,以提高试样的致密性和硬度均匀性。
试验参数的选择:根据粉末材料的性质选择合适的压头(如金刚石锥或硬质合金球)和载荷,并根据试验标尺对压痕深度进行合理换算,以便正确评估硬度值。
试验环境的控制:在进行洛氏硬度试验时,需要严格控制环境温度和湿度,以减少其对硬度测量结果的干扰。此外,应定期校准硬度计,以确保测量的精度和稳定性。
粉末材料洛氏硬度试验的应用与展望
通过洛氏硬度试验,粉末材料的硬度特性能够被准确表征,这为材料的工艺优化和应用拓展提供了重要依据。在汽车、航天、电子等行业,粉末冶金技术生产的零部件,如齿轮、轴承、电子元器件外壳等,其硬度性能直接影响到产品的使用寿命和可靠性。借助于洛氏硬度试验,可以进行有效的质量控制,使产品性能达到设计要求。
随着检测技术的不断发展,现代材料检测中已开始引入自动化和智能化的手段,这也为粉末材料的洛氏硬度检测带来了新的机遇。通过结合计算机视觉、人工智能算法等技术,可以实时分析压痕图像,提升硬度测量的自动化水平和精度。此外,研究和开发适用于粉末材料的专用硬度检测仪器和标尺,也将为粉末冶金行业的发展带来更大的推动力。
总之,粉末材料洛氏硬度试验检测在材料科学和工程领域具有重要的应用价值。随着技术的不断进步,其在工业生产中的应用将更加广泛,并助力于新材料的开发和应用。
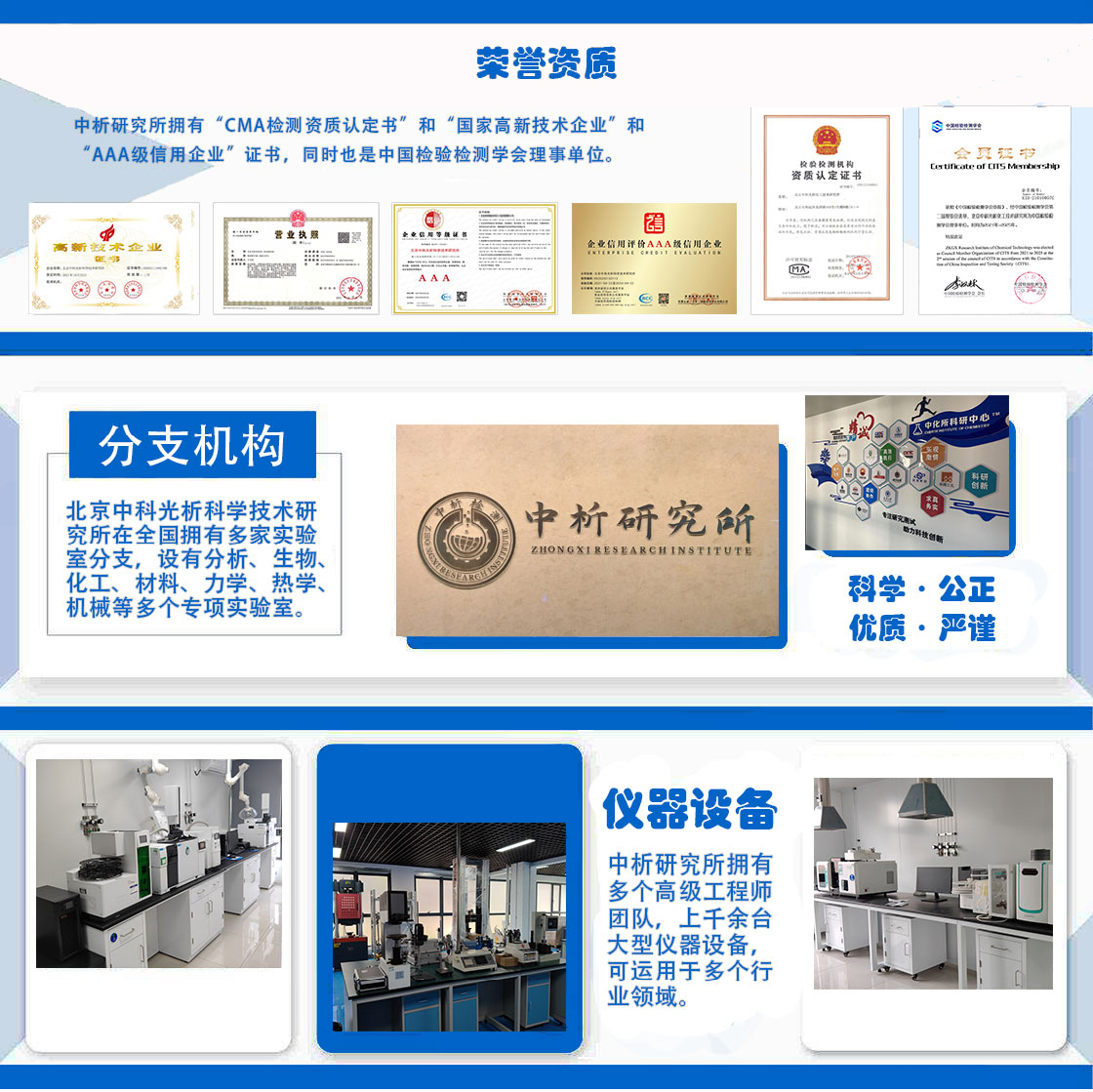
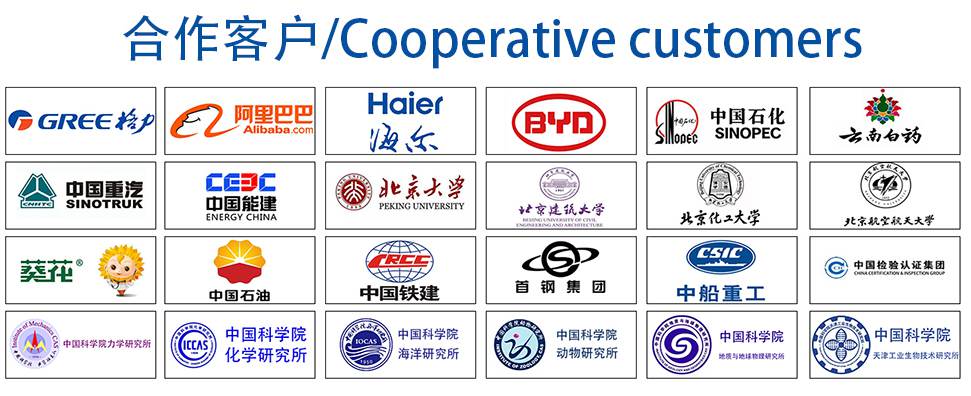