伺服阀耐久性试验检测
概述
伺服阀是现代化液压和气动系统中关键的控制元件,其性能和可靠性直接影响到整个系统的正常运行。在许多工业和航空应用中,伺服阀的工作环境复杂且要求严苛,因此对其耐久性提出了很高的要求。为了确保伺服阀在实际使用过程中能够长期稳定地工作,对其进行耐久性试验检测是至关重要的。这不仅有助于识别潜在的故障模式,也能为产品的研发和改进提供数据支持。
伺服阀的功能与作用
伺服阀是一种由电信号驱动的液压或气动控制阀。其主要功能是精确控制流体的流量、方向和压力,进而实现对执行机构的精确控制。伺服阀广泛应用于飞机的飞行控制系统、工业自动化、机器人以及其他需要高精度运动控制的领域。在这些领域中,伺服阀的性能直接决定着整个系统的响应速度、精度和稳定性。
耐久性试验的必要性
伺服阀的使用环境通常极为复杂,不仅要承受高温、高压,还可能面临频繁的动态负载变化。这就要求伺服阀必须具备高水平的耐久性。耐久性试验旨在模拟伺服阀在真实工作环境中的长期运行状况,借助试验来评估和验证伺服阀在长时间运行后仍能保持可靠性的能力。通过这样的检测可以提前发现潜在的问题和缺陷,从而在设计和制造过程中加以改进。
耐久性试验的类型
伺服阀耐久性试验通常包括以下几种类型:
- 循环加载试验:模拟伺服阀在实际应用中所经历的循环载荷,以检测其在长期工作中的耐疲劳能力。
- 环境试验:评估伺服阀在极端环境条件(如高温、低温、湿度、腐蚀性环境等)下的可靠性。
- 老化试验:加速伺服阀的材料老化过程,观察其在长时间使用后材料性能的变化。
- 性能退化试验:记录伺服阀在长时间工作后性能指标(如响应时间、泄漏量、压力控制精度等)的变化趋势。
- 振动和冲击试验:通过模拟真实环境下的机械振动和冲击,检测伺服阀的机械结构和连接件的稳定性。
试验方法与设备
为了准确地进行伺服阀的耐久性试验,通常需要使用专业的试验设备和手段。测试系统中会采用高速数据采集设备,用于实时记录伺服阀性能指标的变化。此外,试验系统可以模拟多种实际工作环境,包括温度变化、压力波动和流体介质的变化。试验过程中,需严格按照预定的工况进行操作,同时不断监测阀门的性能和状态。
试验数据的分析
耐久性试验获得的数据极为关键,这些数据将为产品的改进和优化提供基础。在数据分析过程中,重点关注伺服阀的性能退化曲线、失效原因分析以及关键性能指标的变化趋势。通过一系列的数据分析,可以更好地了解伺服阀在不同操作条件下的使用寿命以及主要故障模式。
伺服阀耐久性试验的挑战
由于伺服阀涉及精密机械、电气控制以及流体动力学等多学科领域,其耐久性试验一直面临诸多挑战。首先,如何模拟真实环境下的多种复杂工况且保持测试的重复性和一致性,这是一个较为复杂的问题。其次,在高压、高温等苛刻条件下进行耐久性试验,涉及到设备的安全性和可靠性。另外,数据的准确记录与分析也对测试系统提出了很高的要求。
未来的发展方向
随着技术的不断进步,伺服阀的设计和制造水平也在不断提高,耐久性试验技术也在不断发展。未来的发展方向包括:
- 引入齐全的监测和诊断技术,实现对伺服阀运行状态的实时监控和故障预测。
- 开发更为智能化的试验系统,结合人工智能和大数据分析,提高试验的效率和数据分析能力。
- 应用新材料和新工艺,提高伺服阀的本身耐久性,从材料研究的角度提升系统整体水平。
总之,通过不断改进伺服阀的耐久性试验方法和技术,可以更好地保障这些关键部件在高要求应用中的稳定性和可靠性。这对于推动工业自动化、航空航天等领域的技术进步具有重要意义。
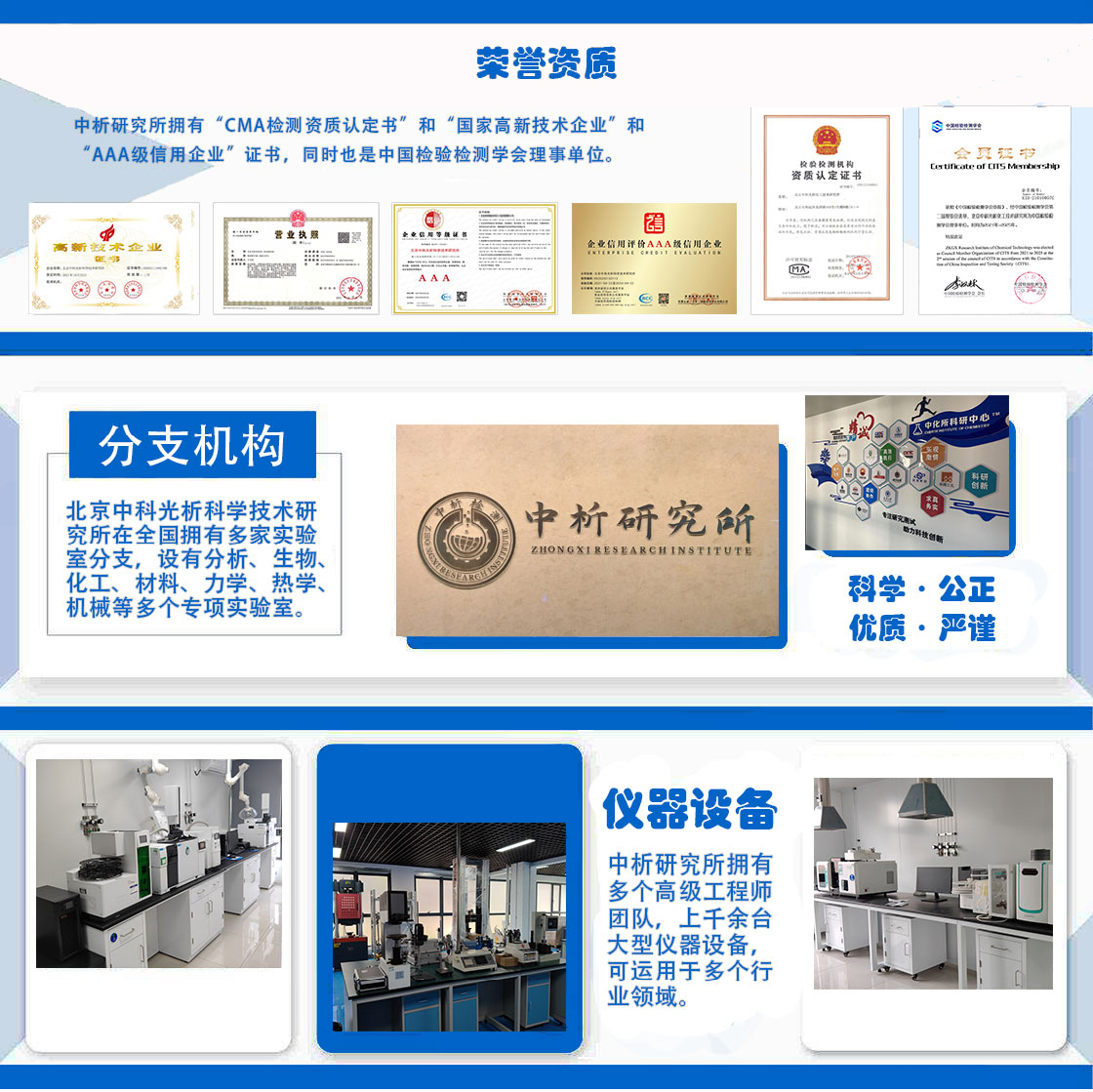
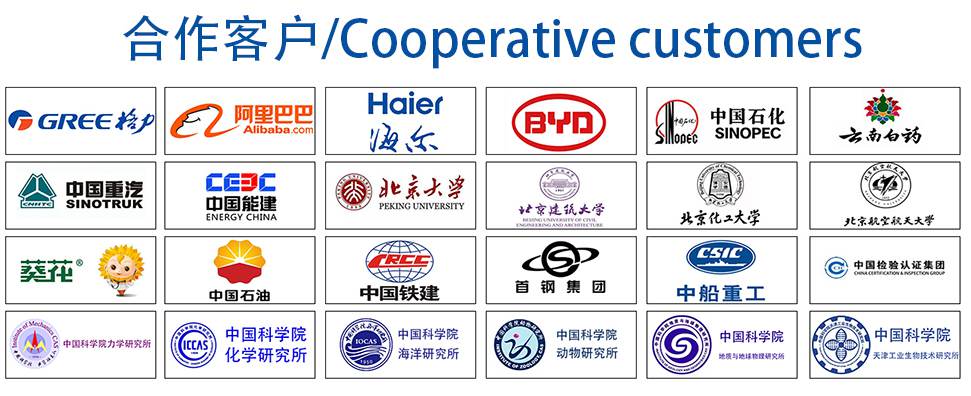