飞机刹车装置湿热试验检测
飞机刹车装置湿热试验检测
作为现代航空器关键部件之一,飞机刹车装置在保障飞行安全、提高操作性能方面起着不可替代的作用。在飞机运行过程中,刹车装置不仅需要适应高强度的制动需求,还需面对各种极端环境因素,如高温、低温、湿度、振动等挑战。其中,湿热环境是一个经常被忽视但却不可低估的因素。因此,对飞机刹车装置进行湿热试验检测显得尤为重要。
湿热环境对飞机刹车装置的影响
湿热试验检测指的是在一定温度和湿度条件下,对飞机刹车装置的性能进行测试。普通的飞行环境中,飞机需要在不同的气候条件下运营。例如,在热带地区,空气湿度往往较高且温度较高,而在冷温带地区则是另外一种情况。湿热环境可能会导致刹车装置部件材料老化、腐蚀加速、性能下降,这对飞行安全有直接影响。
湿热条件下,以下几个关键方面可能对飞机刹车装置的性能造成威胁:
- 材料腐蚀:刹车装置由多种不同金属和复合材料组成,在湿热环境中,材料可能发生氧化、腐蚀,降低装置的强度。
- 润滑剂失效:刹车装置中使用的润滑剂可能因湿度过高发生乳化或失效,进而影响活动部件的灵活性。
- 电气元件的故障:现代刹车装置通常包含电气组件(如传感器、控制模块等),湿气可能引起电气元件短路或失灵。
- 机械部件磨损加剧:湿热环境会加速刹车装置中机械部件的磨损,降低整体使用寿命。
综上所述,湿热环境对刹车装置的可靠性影响不可小觑。通过科学的湿热试验检测,可以有效验证设备的性能并发现潜在问题,为更好地提高安全性提供保障。
湿热试验检测的主要目标
湿热试验检测旨在评估飞机刹车装置的整体质量和性能,确保其能够满足各种使用场景的需求。具体来说,湿热试验的目标包括以下几个方面:
- 评估刹车装置在高度湿热环境下的长期工作能力,确保可靠性。
- 发现设备可能存在的设计缺陷或材料问题,为改进提供依据。
- 验证刹车装置的长期耐久性和性能稳定性。
- 测试不同环境下润滑剂、电气元件以及传感器的可用性。
- 确定设备是否满足航空行业中相关质量标准的要求。
通过试验数据的积累和分析,湿热试验不仅能帮助厂商优化产品设计,还能为监管机构和航空公司提供科学依据,制定使用及维护改进策略。
湿热试验检测的操作流程
湿热试验检测遵循一套标准化的测试流程,以确保试验数据的准确性和可重复性。以下是湿热试验检测的关键步骤:
1. 样品准备与安装
在试验开始之前,需要从生产线或实际运行的飞机上获取刹车装置样品。样品应具有代表性,避免因个体差异影响试验结果。随后,技术人员将样品安装在试验设备上,同时记录相关参数,如尺寸、重量和主要性能指标。
2. 模拟湿热环境
试验设备会创建一个模拟的湿热环境,包括温度控制(比如40℃~70℃范围)和湿度调节(通常达到80%以上),以逼近飞机在热带或高湿地区运行时的真实条件。测试过程可能持续数十小时甚至数天不等。
3. 运行测试
在湿热环境下,刹车装置将按照一定的工况进行运行测试。例如,重复制动、快速刹停和最大负载操作等。测试人员会监测运行过程中温度变化、机械运动阻力、电流变化等数据。
4. 数据记录与分析
试验过程中,检测系统将实时记录各项指标,如制动响应时间、刹车力矩、材料表面状态等。技术团队会综合分析这些数据,以评估设备的性能稳定性和耐用性。
5. 后续观察与故障分析
试验完成后,刹车装置样品将进行详细检查,以观察是否存在如腐蚀、变形、裂纹等问题。如果发现故障,还需要进一步分析是由设计问题、材料问题还是环境因素所导致。这一步骤对于整改和优化设计具有重要意义。
湿热试验检测的技术保障
进行湿热试验检测需要依靠齐全的技术设备和科学的试验方法,包括以下几个方面的技术支撑:
- 环境模拟设备:如恒温恒湿箱,可以精确控制温度和湿度,模拟各种复杂气候条件。
- 传感器和监测系统:实时监测刹车装置的性能变化,例如温度传感器、应变传感器等。
- 高效的数据分析工具:利用分析软件处理和解读试验数据,筛选关键参数,发现潜在问题。
- 专业技术团队:试验背后需要机械、材料、电气等多学科技术人员的协同配合,以确保检测的全面性和准确性。
湿热试验检测的意义和未来展望
湿热试验检测对于提升飞机刹车装置的性能和可靠性具有重要意义。不仅支持了航空安全性的发展,还推动了航空材料、机械技术和环境模拟设备的进步。在未来,随着航空航天技术的不断进步,湿热试验检测将继续向更加智能化、自动化方向发展。通过引入人工智能、大数据和物联网等新兴技术,试验过程将变得更加高效和精准。
总的来说,飞机刹车装置湿热试验检测不仅是一个技术过程,更是航空安全保障体系中的重要一环。只有通过不断检测和优化设备,航空领域才能在面对各种极端环境时应对自如,为乘客与货物提供更加安全可靠的飞行体验。
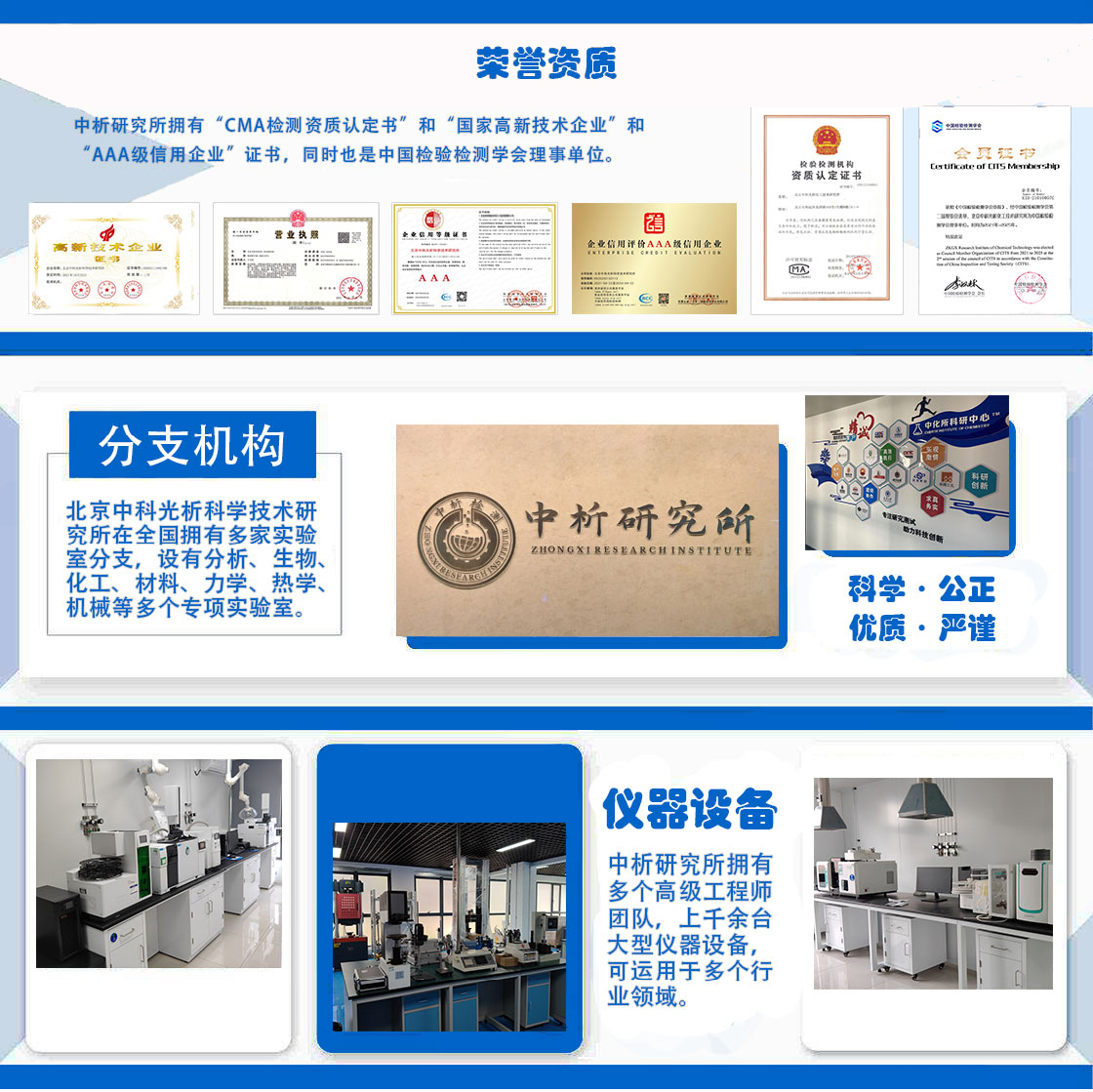
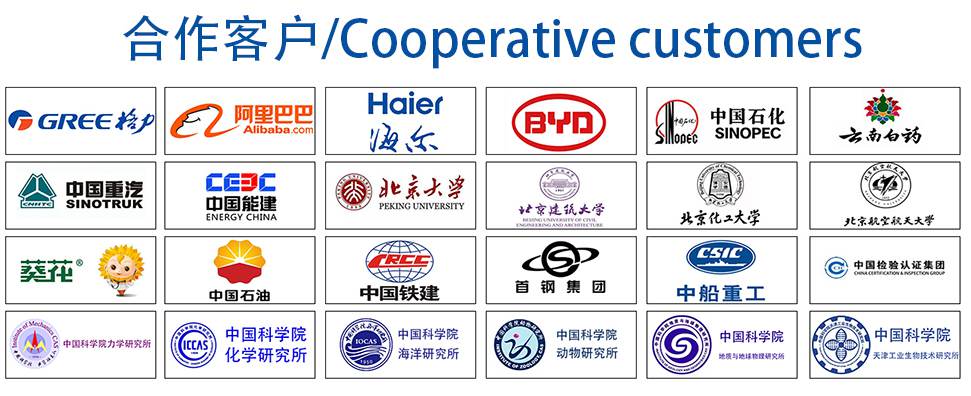