电连接器及组件温度冲击检测
引言
电连接器及其组件在现代电子设备中扮演着至关重要的角色,作为电信号传输的桥梁,它们的性能和可靠性直接影响到整个系统的稳定性和效率。随着电子产品应用的多样化和复杂化,电连接器面临的工作环境愈发苛刻,尤其是在汽车、航空航天和户外设备等领域,组件通常暴露于不同极端温度条件下。因此,温度冲击检测成为确保电连接器质量与可靠性的重要环节。
温度冲击检测的必要性
温度冲击检测旨在评估电连接器及组件在快速温度变化下的性能表现。由于不同材料在温度变化下的热膨胀系数不同,若受制于热应力,可能导致接触不良、材料龟裂或者损坏连接器壳体等问题。这种测试能及早识别潜在故障,并帮助设计者优化材料选择和结构设计,以提高整体的稳定性和可靠性。
检测标准与方法
国际上有多个组织制定了关于电连接器温度冲击检测的标准,诸如IEC(国际电工委员会)、MIL-STD(美国军用标准)和IPC(国际印制电路协会)等。这些标准规定了温度变化范围、循环次数、测试环境等方面的具体要求。
典型的温度冲击检测方法包括热循环法和热冲击箱法。热循环法涉及在高低温之间进行缓慢均匀的温度变化,着重于测试材料的耐久性。而热冲击箱法则通过在极高与极低温之间快速转换环境,从而更直接检验产品的抗热冲击能力。对于电连接器,热冲击箱法更适用,因为它更能模拟真实工况下的快速温度波动。
测试过程和步骤
电连接器温度冲击测试大致包括以下几个步骤:
1. **预处理**:在测试前对样品进行清洁,确保检测中的样品不包含任何污染物。
2. **温度冲击装置设置**:使用特定的温度冲击箱,提前设定温度范围和循环次数。例如,从-40°C到125°C,保持每个温度下5分钟并循环100次。
3. **样品安装**:将电连接器固定于温度冲击装置中,确保其能均匀地接受温度变化。
4. **实施检测**:开启温度冲击设备,按照设定的程序进行温度循环。
5. **后处理与评估**:测试完毕后,对样品进行功能性及外观检查,判断温度冲击后是否出现金属疲劳、接触不良或者材料破损。
温度冲击检测的挑战
即便温度冲击检测在许多方面能提供有效的质量控制手段,然而它也面临着一些挑战。诸如,在极端条件下对电子连接器进行测试可能导致耗时过长,并且对于某些特定材料,可能需要特别设计的测试程序。此外,成本因素也是实施温度冲击检测时需要考虑的重要方面,尤其是在大批量生产的情况下,需要确保检测不仅仅是有效的,而且是经济的。
创新与发展
为了应对这些挑战,业内不断探索更高效、更精确的温度冲击检测技术。利用人工智能与自动化技术的结合,未来的温度冲击检测或可实现智能监测与数据分析,从而大幅提升效率与检测的准确性。比如,机器学习可以通过分析以往测试的数据,预测某种设计或材料在温度冲击下的寿命与可靠性。
电连接器及组件的温度冲击检测是确保其在极端环境下发挥预期功能的关键手段。随着技术的不断进步和应用范围的不断扩展,检测方法和标准也在逐渐优化与更新。对于电连接器制造商而言,保持对温度冲击检测的重视,有助于提高产品质量和市场竞争力。通过标准化流程与齐全技术的集成,温度冲击检测不仅是一个质量控制工具,还是一个推动创新和研发的驱动力。
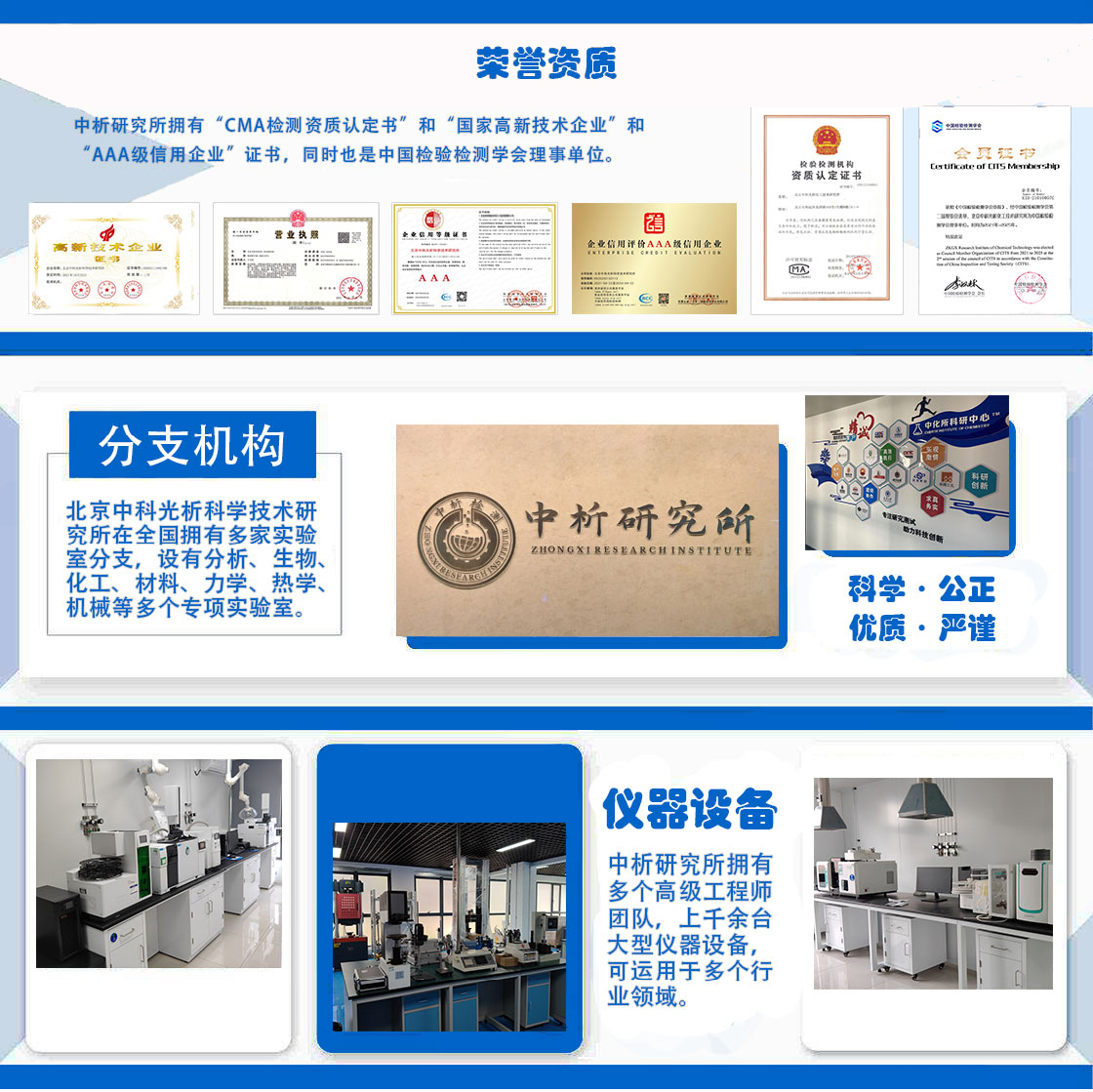
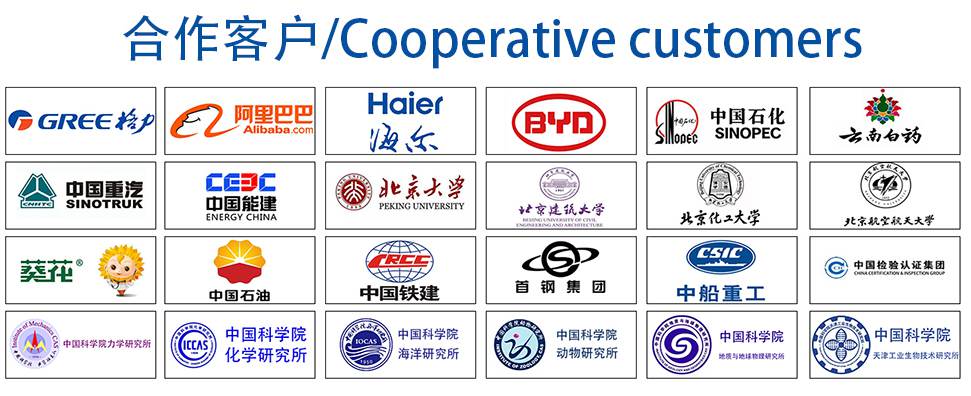