电连接器及组件盐雾检测
电连接器及组件盐雾检测的重要性
电连接器是电气和电子设备中不可或缺的基本组件,广泛应用于从消费电子到航天航空的各个领域。由于这些组件的多功能性和关键性,它们必须在各种环境中保持卓越的性能。然而,自然环境中如海洋或工业大气中的盐雾,对金属和材料的耐腐蚀性能提出了严峻挑战。因此,盐雾检测成为保证电连接器质量和可靠性的重要步骤。
盐雾环境对电连接器的潜在危害
在实际应用环境中,电连接器常会暴露在高湿度和含盐环境中,尤其是应用于海洋工程、沿海城市的基础设施以及某些工业和交通工具上。这些状况下的盐雾会加速金属材料的腐蚀,可能导致电连接器的导电性能下降,接触不良,甚至完全失去功能。此外,腐蚀产生的产物还可能进一步导致与之连接的其他组件受到影响。
因此,为了保证电连接器在腐蚀性环境中保持良好性能,盐雾测试成为了一种常见的评估手段。通过实验室中模拟的盐雾环境中测定样品的耐腐蚀性,设计和材料能够在投放市场之前得到验证和改进。
盐雾检测的标准和方法
国际和国家层面上存在多种针对电连接器盐雾检测的标准,其中最为常见的包括ISO 9227、ASTM B117和IEC 60068-2-11等。各个标准对测试条件、时间和评价准则有一定的区分,但检测的核心目的都在于评估连接器及其材料在相应环境中的耐腐蚀性。
盐雾检测通常在一个可控的密闭空间内进行,其过程包括喷洒含有盐(通常是氯化钠)的雾状溶液,模拟高盐环境。通过调整温度、湿度和喷雾密度,实验室能够再现不同程度的腐蚀条件。在测试之后,检查试样的表面状态、导电性变化,以及机械性能变化等指标,以确定材料或涂层的耐腐蚀能力。
例如,ISO 9227是一种广泛采用的盐雾测试标准,其将盐雾环境的氯化钠浓度设置为5%,pH值处于6.5到7.2之间,同时测试温度保持在35°C。这种条件下的测试通常持续48至1000小时,时间长短因测试目的和材料性能差异而变化。
电连接器材料选择与改进
对抗腐蚀性条件的首要策略是选择适合的材料。许多电连接器采用铝合金、不锈钢、铜合金以及镀锌层等具有良好耐腐蚀性能的材料。不过,材料的选择不仅仅需要考虑耐腐蚀性,还需要兼顾导电性、成本、重量等因素。
涂层技术的应用是提高组件耐盐雾性能的另一种有效方法。采用防腐蚀涂层可以有效隔绝盐雾与金属表面的接触,从而延长组件的寿命。近年来,新型涂层材料和技术的开发,提供了更为高效、经济的解决方案。例如,纳米涂层技术和电镀金属镀层可以在改善耐腐蚀性能的同时,不显著增加成本。
未来盐雾检测的发展方向
随着科技的进步和使用需求的变化,电连接器及组件的盐雾检测技术也在不断进化。未来的发展方向包括检测技术的智能化、数据分析的更精细化以及标准的统一化。
智能化的盐雾检测将通过大数据和人工智能技术,实现对测试数据的深度分析,提高检测的准确性和效率。此外,集成传感器和自我监测系统的应用能让实时监控腐蚀过程成为可能,从而得出更具参考意义的腐蚀行为数据。
同时,不同行业和地区之间检测标准的统一化将为国际贸易降低技术壁垒,促进化合作。标准的统一化不仅便于各国的产品在市场流通,也能推动相关领域的技术创新和共同进步。
盐雾检测在电连接器及其组件的质量保证中占有重要位置。通过它,产品在早期阶段得以评估其在复杂环境下的寿命和性能,有效保障最终用户的使用安全以及产品的市场竞争力。随着相关技术的不断发展,我们期待盐雾检测能在日趋严苛的应用环境中,为更多的电气与电子设备提供坚实的质量保障。
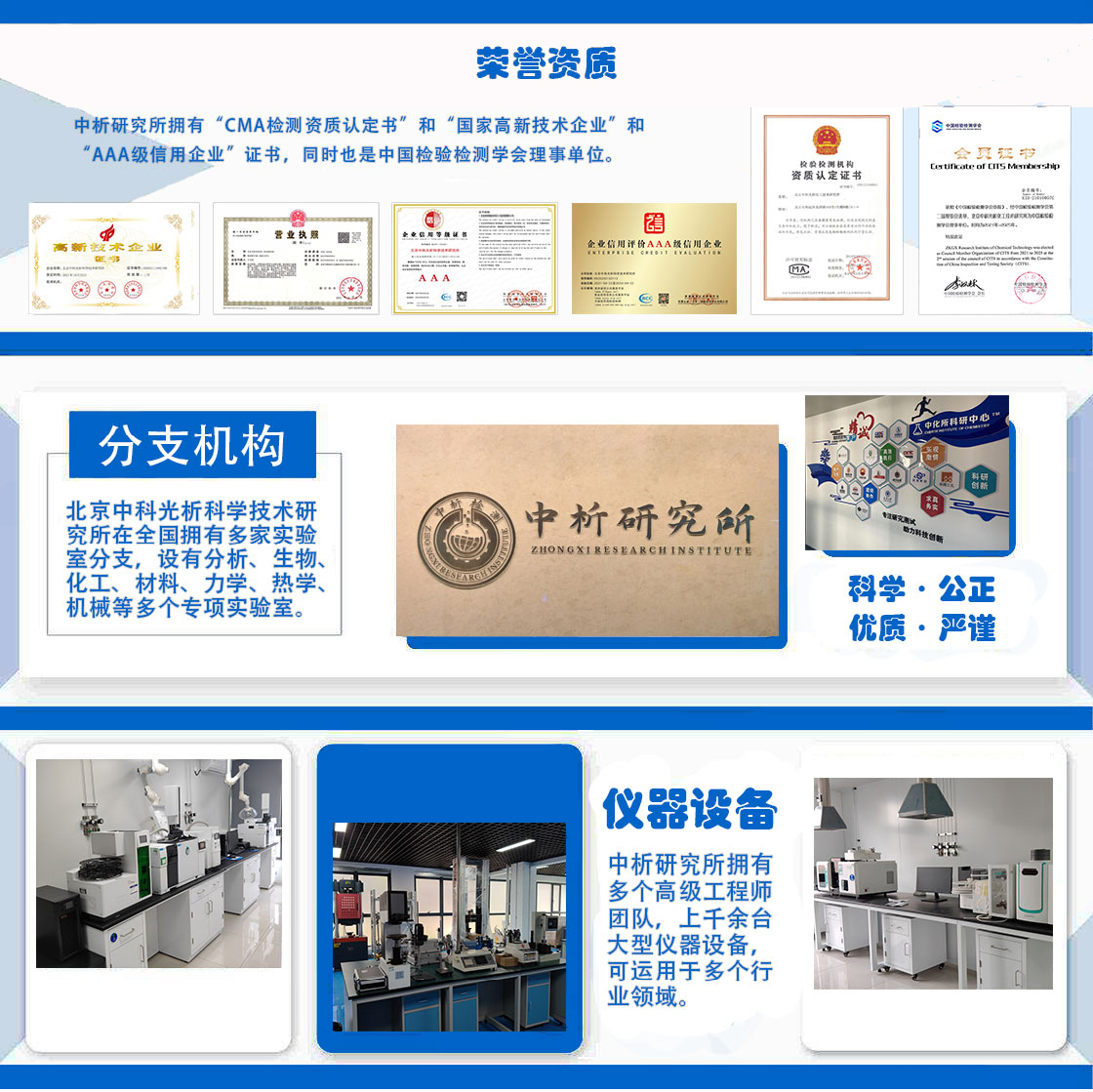
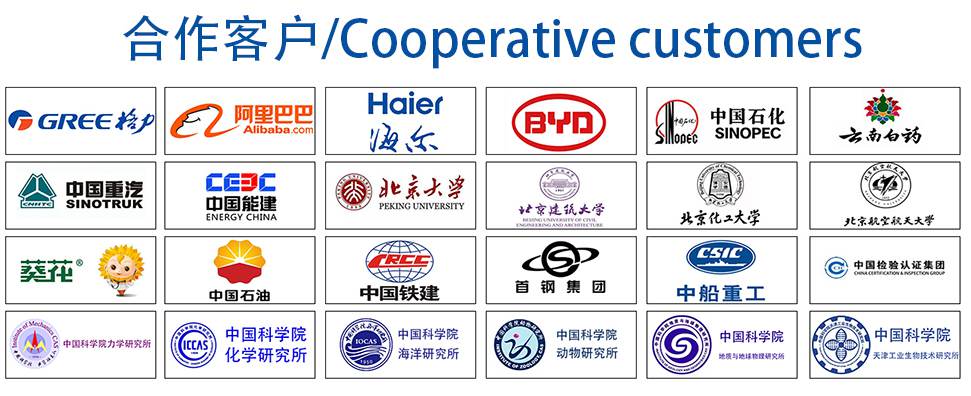