铜及铜合金制品铅、铁、砷、锡、镍、锌、磷、硫、锰、硒、铬、钴、镉检测
铜及铜合金制品中的成分检测:关注铅、铁、砷等元素
铜及铜合金因其优越的导电性、导热性以及抗腐蚀性能而广泛应用于各个行业。然而,在生产和应用过程中,其化学成分的检测显得尤为重要,以确保其性能与安全性。尤其是铅、铁、砷、锡、镍、锌、磷、硫、锰、硒、铬、钴、镉等元素,它们的含量直接影响到铜合金制品的质量和应用效果。
铜合金成分检测的重要性
随着工业的不断发展,铜合金制品被广泛应用于电气、建筑、通信等领域。为保证这些产品在使用过程中的可靠性和安全性,必须对其组成成分进行严格检测。检测不仅仅是保证产品质量的手段,同时也能够推动行业标准化的发展,确保市场上产品的合格性。
具体来说,各元素的含量决定着铜合金的物理、化学特性。例如,铅和砷虽然能赋予合金一定程度的加工性能,但其对人体的毒性不容忽视。因此,严格控制产品中这些元素的含量不仅是出于性能上的考虑,也是对公众健康的负责。因此,铜及铜合金中元素成分的检测是生产过程中的重要环节。
关键元素的检测及其影响
铅(Pb):铅在铜合金中主要是用来改善合金的切削性能。然而,由于其毒性,它的含量必须受到严格控制。过量的铅摄入会导致中毒,影响神经系统和心血管健康。因此,相关产品的铅含量检测至关重要。
铁(Fe):铁元素有利于提高合金的强度和硬度。然而,若铁含量过高,可能导致合金的导电性下降,影响其在电子元件中的应用。因此,准确测定铁的含量对于使用性能的保证至关重要。
砷(As):砷作为一种毒性很强的元素,其在铜合金中的存在通常源于原材料的矿物成分。尽管其主要用于提高合金的耐腐蚀性,但砷的有害性决定了必须对其含量进行严密的监督。
锡(Sn):锡的添加可以提高铜合金的强度和耐磨性。然而,在某些应用中,锡含量需要在一定范围内,避免合金的脆化和硬度下降。
镍(Ni)和锌(Zn):这两种元素通常用于提高铜合金的耐腐蚀性和机械稳定性。过高的含量则可能导致合金变得过于坚硬,影响其加工性能。
检测技术的发展与挑战
随着技术的进步,铜及铜合金中的成分检测方法也在不断发展。目前,常用的检测技术包括光谱分析、质谱分析、X射线荧光光谱(XRF)等。这些方法能够快速、准确地检测出合金中的各种元素含量,为质量控制提供可靠数据支持。
不过,检测技术面临的挑战依然存在。首先是检测的精度问题。随着合金元素数量的增多,复杂的化学环境可能导致检测误差。因此,齐全的检测设备和技术人员的专业水平至关重要。其次,不同国家和地区对于合金成分的标准不同,这增加了国际贸易中的技术性壁垒。
标准化及未来展望
为解决检测中的问题,国际上已经有众多相关标准出台,例如美国的ASTM标准以及中国的国家标准(GB),这些标准对铜及铜合金的化学成分进行了明确的规定。此外,国际标准化组织(ISO)也在不断致力于推动化的检测标准,保障行业的统一性及公平性。
展望未来,随着科技的进步和环保意识的增强,对铜合金的检测将会更加精确和环保。新型的无损检测技术、基于人工智能的分析软件等将进一步推动行业的发展。我们期待,在不久的将来,检测技术的进步能够带来铜合金制品的更高质量和更广泛的应用。
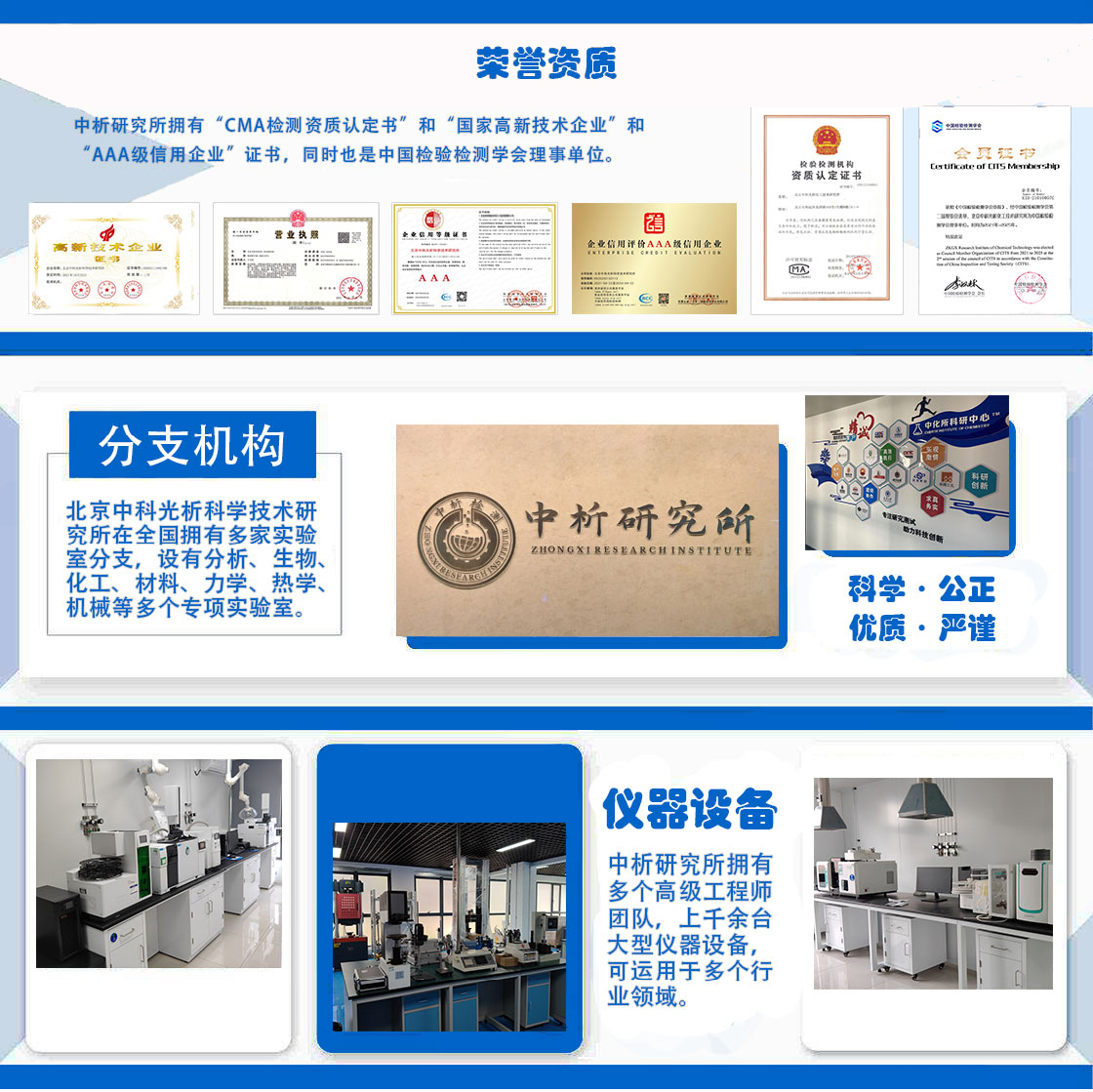
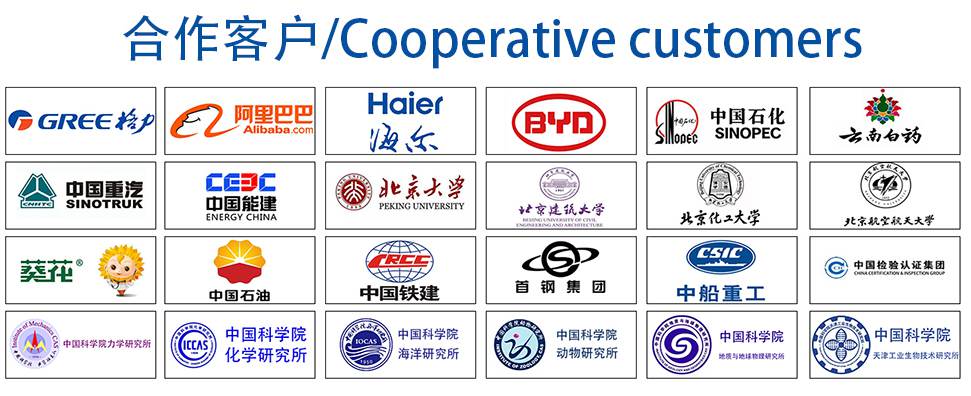