漆包线(铜线,铝线)耐刮检测
漆包线的概述
漆包线是一种由绝缘漆膜包覆在导电金属线材上而制成的特殊电线,其中常用的金属基材包括铜和铝。漆包线在电机、变压器、绕线电感器以及各种电器设备中发挥着不可替代的作用。这类电线的品质直接关乎到电子设备的正常运行,因此进行耐刮检测以确保其绝缘性能至关重要。
漆包线的组成与作用
漆包线的核心是导电性良好的金属线材,常用的材料为铜和铝。铜线以其优异的导电性和机加工性成为应用最多的材料,而铝线则由于其轻量特性和成本相对较低,在某些领域获得了广泛应用。在这些金属线材的外表涂覆一层或多层绝缘漆膜,其主要功能是隔离、绝缘、防止电能损耗及电机绕组短路。此外,这层漆膜还可以防止空气中的氧气对导体的氧化。
漆包线耐刮检测的重要性
漆包线在使用过程中,刮擦是不可避免的,这可能会对绝缘层造成损伤,进而导致短路或其他形式的电气故障。因此进行耐刮测试来评价漆包线的质量和耐用性至关重要。耐刮检测不仅能揭示绝缘层的耐用性,还可以指示生产过程中可能存在的涂层缺陷,确保最终产品在实际应用中的可靠性和安全性。
漆包线耐刮检测的方法
漆包线耐刮检测一般采用专门的耐刮测试仪器,通过一定压力下对漆膜进行刮伤以评估其耐磨性。具体检测方法大概可以分为如下几个步骤:
首先,将一定长度的漆包线样本切割下来,确保其表面光洁无污物。接着,使用耐刮测试仪施以固定的负载利用刮针在样本表面施压刮伤。在刮伤过程中持续监测漆膜是否发生破裂或者剥落。最后,通过显微镜或者裸眼观察刮痕的深度和是否有金属裸露出来来判定结果。
通常,耐刮测试会规定一定的负载和加压时间,以模拟各种实际操作环境下的使用情景。检验合格的漆包线在测试后应该没有金属外露迹象,并且表面漆膜在刮痕处保持完整。
影响漆包线耐刮性能的因素
多个因素会影响漆包线的耐刮性能,其中包括所用的材料和涂料的性质、涂层的厚度,以至于生产工艺和操作参数。铜和铝的机械性能存在不同,这也导致其对漆膜附着力的要求有所差异。涂层材料的选择至关重要,材料特性如硬度、韧性及粘合性能会对最终性能产生直接影响。此外,涂覆过程中的温度和湿度,以及涂覆后是否正确进行固化处理,都会最终影响到漆包线绝缘层的耐磨损性。
漆包线耐刮检测的行业标准
为了确保耐刮检测的统一性和可比性,不少国家及地区制定了相应的质量标准,如IEC 60851(国际电工委员会标准),UL 2353(美国安全实验室标准)等。这些标准在耐刮测试的方法、程序,结果判定等方面作了多样而详细的规定。制造商需要确保其产品符合相关标准,从而在市场竞争中确保稳定的产品质量和消费者信任。
漆包线应用领域的检测实例
在应用领域中,漆包线耐刮性能测试不仅限于电机、电器等装置,还涉及到航空、 航天及新能源汽车等高要求领域。例如在电动车电机绕组中,耐刮性能直接影响到电车的运行稳定性和安全性。对于这些关键领域的线缆产品,除了标准耐刮检测还会有额外的苛刻测试,用以针对使用中的各种极限条件。
总结与未来展望
漆包线作为现代电子设备中的重要元件,其功能和质量对电子设备的稳定性和性能影响重大。在漆包线制造过程中,耐刮检测作为一种重要的质量检控手段,不仅保障了制成品在出厂前的合格性,更为未来技术的变革和发展提供了重要的数据支持。展望未来,随着对高频和高效的电子元件需求不断增加,漆包线的耐用性和可靠性将继续提升,更多新型材料与涂层技术将被引入,以提高耐刮性能和耐环境能力,更好地服务于科技发展需求。
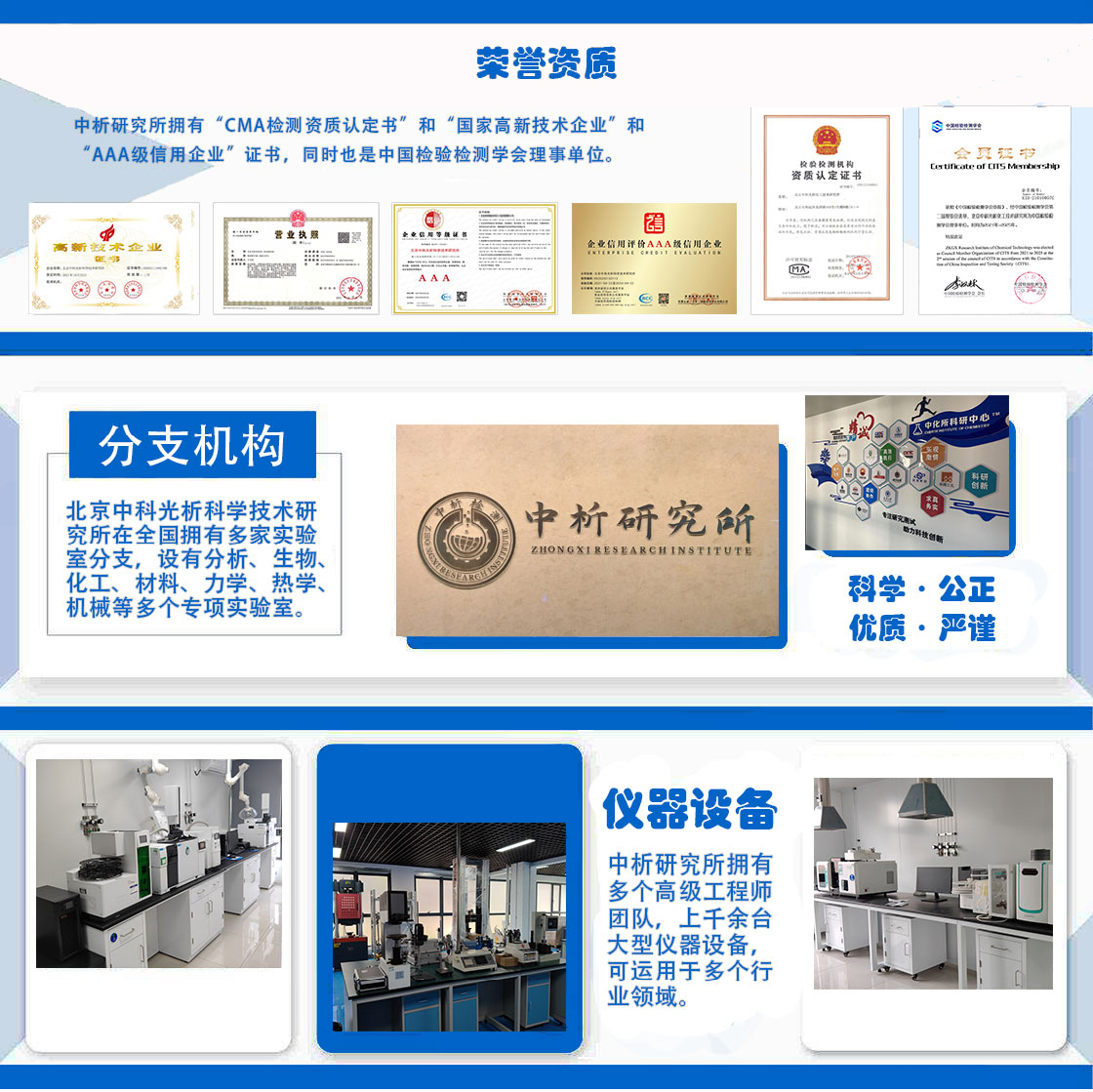
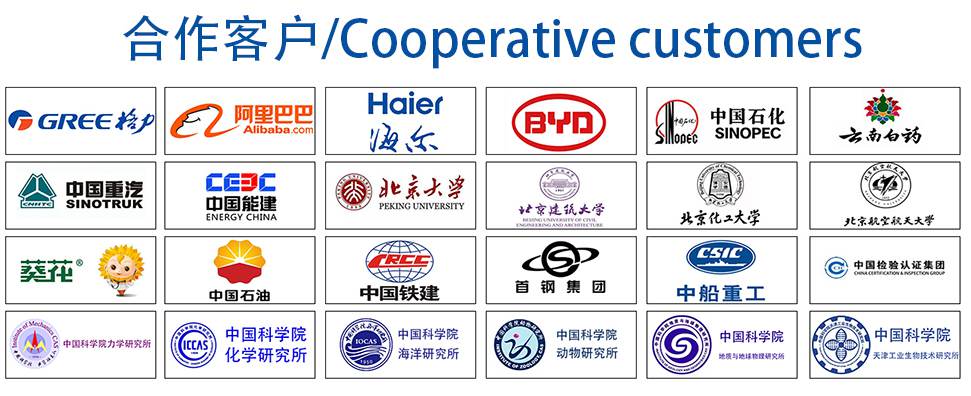