尾管悬挂器及尾管回接装置尾管悬挂器负荷能力试验检测
尾管悬挂器及尾管回接装置:技术背景与重要性
在石油和天然气的钻井和生产过程中,尾管悬挂器及尾管回接装置是至关重要的设备。这些装置不仅承载着尾管的重量,还能抵抗由于井下作业导致的各种压力和应力。因此,确保其负荷能力和运行可靠性是管柱设计和完井设计中的关键因素。正因如此,对尾管悬挂器进行负荷能力试验检测显得尤为必要。
尾管悬挂器的功能与作用
尾管悬挂器的主要功能是将尾管可靠地悬挂在井口设备上,并能在长期使用过程中抵抗多种复杂工况带来的挑战。如同建筑中的基础系统一样,尾管悬挂器需承载各种轴向和横向的力,在高压、高温、腐蚀性液体干扰的环境下保持其功能的完整性。因此,这就要求这些设备具备极高的强度和稳定性。
尾管悬挂器的设计还考虑到未来的维护和检修需求,因此这些装置通常还需要具备良好的互操作性和适度的灵活性,以便在复杂多变的井下条件下进行适应性调整。这一功能使尾管悬挂器成为油气井系统的核心组件,确保整个井的结构完整性和安全性。
尾管回接装置在油气井中的作用
尾管回接装置主要用于连接井口与井下管线产品。通过这套装置,工作人员可以在地面与井底之间建立起稳固的流体通道。这也使得一旦发生泄漏或压力异常,能通过尾管回接装置进行有效控制和处理。此外,尾管回接装置还需承受来自地下的各种机械负荷和高温高压等严酷条件。
尾管回接装置对环境和安全的要求尤为严格。失效可能导致灾难性的后果,如井喷、环境污染以及重大经济损失。因而,这些装置必须通过全面的试验和检测来验证其设计及制造的可靠性。
负荷能力试验检测的重要性
对于尾管悬挂器和尾管回接装置而言,负荷能力是其最关键的性能指标之一。这不仅关乎其能否承载尾管重量,还涉及是否能在长期使用中有效抵抗各种井下工况诱发的变量负荷。通过负荷能力试验检测,可以全面鉴定设备在各类实际工况下的耐受程度和反应水平。
负荷能力试验检测通常包括静力试验和动态试验。静力试验通常在标准实验室环境中进行,则施加逐渐增加的载荷直至达到设备的设计极限。动态试验则模拟真实工况中快速变化的载荷条件,如振动、冲击等对设备进行更为苛刻的测试。
在进行负荷能力试验检测时,需采用高精度的测量设备和传感器,确保在大型设备上的每个关键点都能准确测量应力、应变、位移等数据。这些数据可为设计改进、选材优化提供实质性依据,并能有效评估设备在实际工况中可能遇到的问题以及潜在的失效模式。
检测过程中的标准与规范
石油和天然气行业通常根据国际和地区标准进行设备检测,以保证尾管悬挂器和尾管回接装置的安全性和有效性。这些标准通常由行业协会、标准化组织制定,如API(美国石油学会)、ISO(国际标准化组织)及其他权威机构。这些组织的标准为设备的设计、制造和检测提供了完整的指导方案。
在负荷能力试验检测中,所有操作和评估都需要严格遵循这些标准,确保检测结果的合法性和可重复性。这不仅有助于设备制造商在市场中树立公信力,同时还能提升整个行业的技术水平和安全标准。
与未来展望
尾管悬挂器和尾管回接装置负荷能力试验检测是确保井下设备可靠性和安全性的不可或缺的环节。随着科技不断进步,新的材料和技术不断引入到设备设计和制造过程中,检测手段也需随之更新和优化。计算机模拟技术、数字孪生技术以及人工智能辅助检测等新兴技术有望在未来提高检测效率和精度,降低成本并提高设备的全生命周期管理水平。
在石油和天然气行业寻求可持续发展的背景下,各类新型尾管及其相关装置对环保及安全性要求的提升,将促使负荷能力试验检测领域不断进步,形成标准更为严格、检测更为精确的未来发展方向。
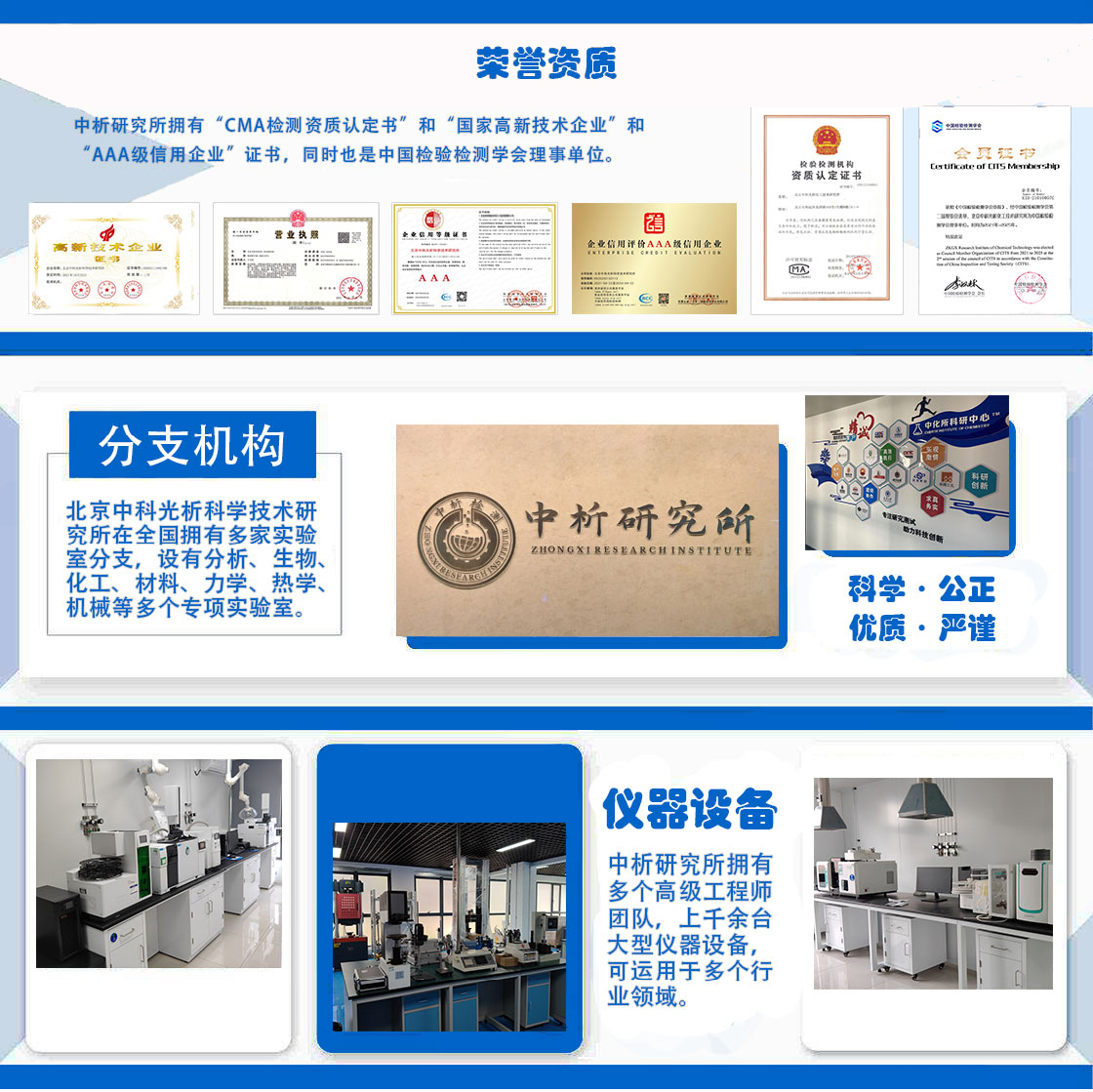
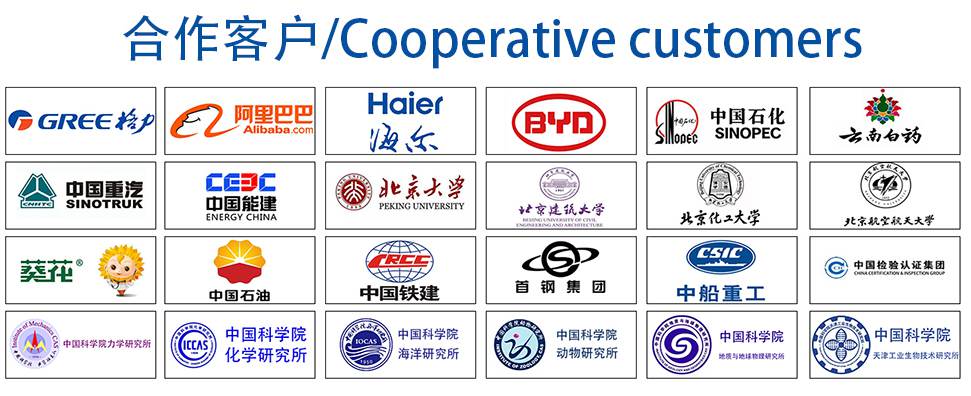