钢铁产品重量偏差检测
引言
随着工业技术的进步和市场对产品质量要求的不断提高,制造业面临着越来越多的挑战。其中,钢铁产品作为重要的工业基础材料,其质量控制至关重要。在钢铁产品的生产过程中,重量偏差一直是质量管控中的一个关键指标。因此,如何有效地检测和控制钢铁产品的重量偏差,已成为确保产品合格率和市场竞争力的重要课题。
钢铁产品重量偏差的来源
钢铁产品的重量偏差主要来源于多个生产环节,如原材料的质量波动、生产工艺的控制精度以及设备的磨损等等。首先,钢材的生产从熔炼到最终成品,需要经过多个工序,每一个环节的微小偏差都会在后续工序中被放大。例如,在轧制过程中,温度、压力、速度的微小变化都会影响最终产品的厚度和密度,从而导致重量的变化。其次,生产设备随着使用时间的增加,精度会有所下降,设备的维护保养不当也可能导致制品厚度的不一致性,进而影响产品的重量。
重量偏差检测的必要性
重量偏差对钢铁产品的质量影响巨大。对于客户来说,重量偏差可能导致产品性能的不一致,进而影响工程质量和使用安全。对于生产企业而言,重量偏差则可能导致材料的浪费或合格率的下降,从而增加生产成本。因此,及时、准确地检测和控制钢铁产品的重量偏差,既是企业降低成本、提高产品竞争力的有效手段,也是保障用户利益和产品安全的重要措施。
传统的重量偏差检测方法
传统上,重量偏差检测主要依赖人工和半自动化的检测手段。在生产线上,工人通过称重及目测等方法,对产品进行抽样检测。这种方法虽然简单,但存在效率低、准确性差、漏检率高等问题。此外,人工检测还受到人为因素影响,如工人的经验水平、工作状态等,难以保证检测结果的稳定性和可靠性。
半自动化检测则利用称重设备和简单的测量工具,通过设定的检测标准进行批量检测。这一方法虽然提高了检测效率,但在面对复杂形状的钢制品时,仍可能出现检测不到位的问题。同时,设备的维护和校准也是影响检测准确性的一个因素。
现代重量偏差检测技术
随着检测技术的发展,现代化的检测系统正在逐步普及。这些系统通常集成了多种高新技术,如计算机视觉技术、激光扫描技术、X射线检测等,提供更高的精度和效率。
计算机视觉技术利用摄像头和图像处理软件,能够自动对产品进行轮廓识别和尺寸测量,从而推算出产品的理论重量,再与实际称重结果进行对比。这种无接触式检测方法快速、准确,并且能够适应多种复杂工件的检测。
激光扫描技术通过发射和接收激光束,对产品的表面轮廓进行扫描测量,获取高精度的形状数据。这种技术尤其适合于形状复杂、不规则的钢铁制品的检测。
X射线检测技术则通过分析产品的内部结构密度,推算出其整体重量。这种方法对被测物的外观质量要求不高,适合用于内部结构复杂的制品检测。
重量偏差检测系统的设计与实现
一个完整的重量偏差检测系统应该包含数据采集单元、数据处理单元以及结果输出单元。数据采集单元负责收集产品的实际重量和体积信息,数据处理单元进行偏差分析与计算,并给出检测结果,结果输出单元则将检测结果反馈至质量控制部门或实时通知生产线进行调整。
应用案例
在某大型钢铁生产企业,采用自动化的重量偏差检测系统显著提高了生产效率和产品合格率。该系统集成了激光扫描和称重模块,通过数据融合技术,能在产品生产过程中实时监控重量偏差。当系统检测出偏差超过允许值时,自动报警并提示操作人员进行调整。此举不仅保障了产品质量,也减少了人为操作的失误,提升了企业的市场竞争力。
总结与展望
钢铁产品重量偏差检测作为产品质量控制的重要组成部分,随着技术的发展,正向自动化、智能化方向发展。现代化的检测方法利用高新技术,提供了更加精确和高效的检测手段,为生产企业提供了有力的质量保证工具。同时,随着工业4.0和智能制造的推进,相信在未来,重量偏差检测技术将进一步融合人工智能、大数据分析等新兴技术,实现更高程度的自动化和智能化,为钢铁制造业的发展提供新的动力。
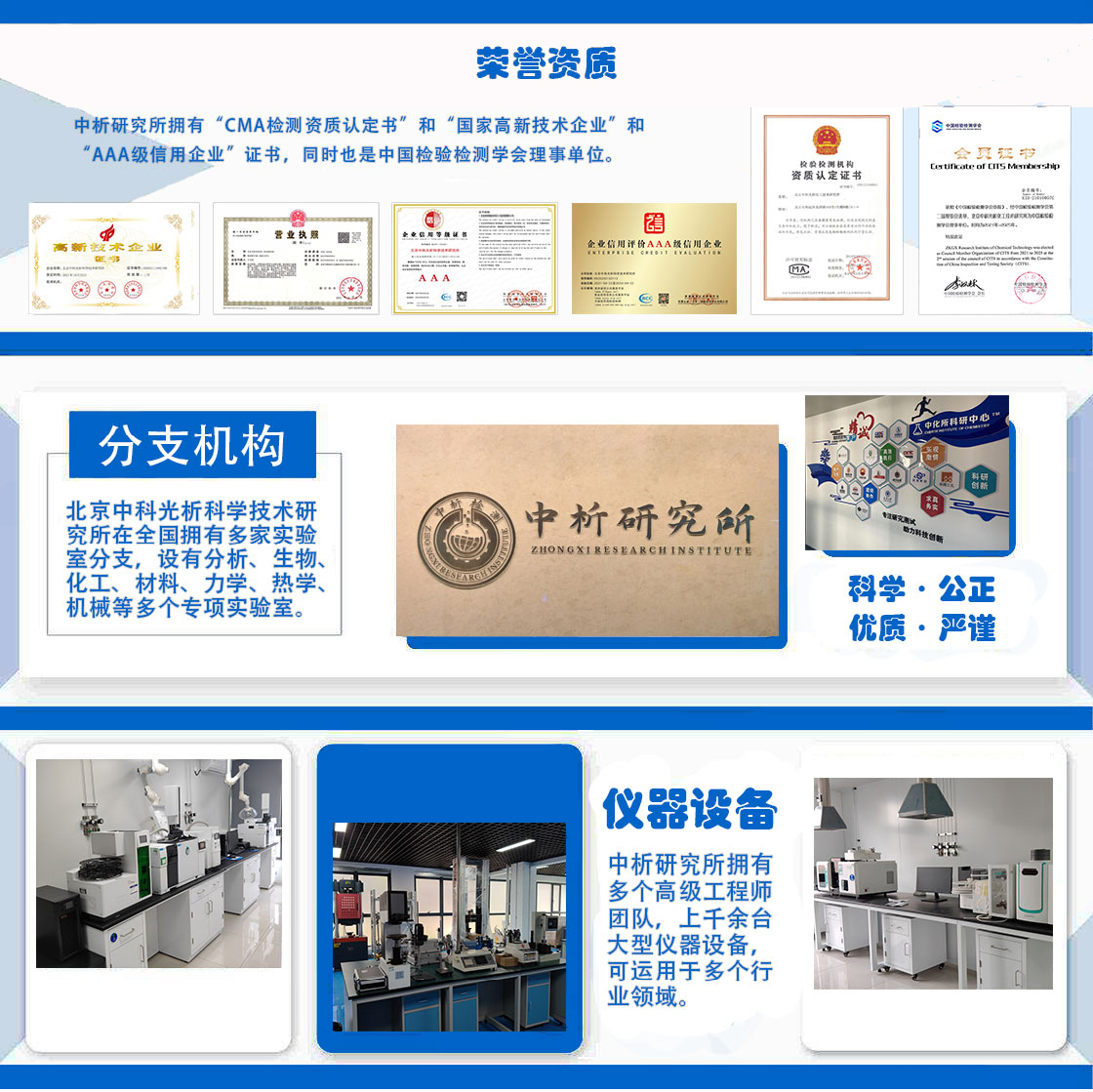
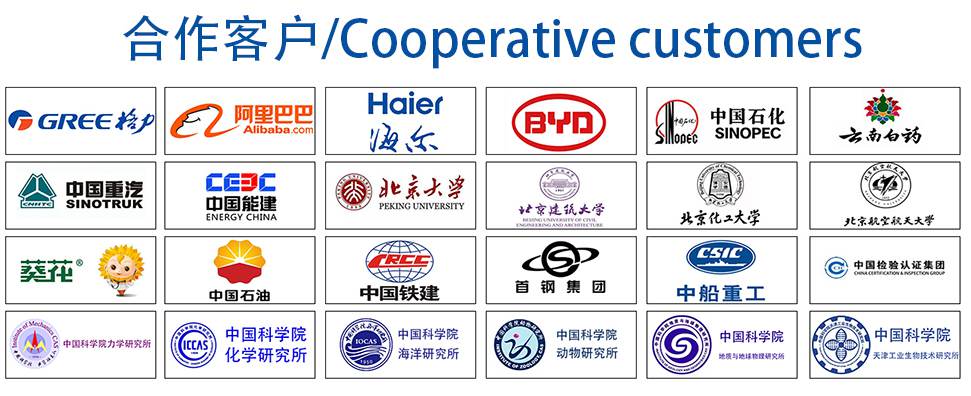