动车组列车作为中国高速铁路系统的核心组成部分,其客室车窗不仅是乘客舒适度和视野体验的关键要素,更是行车安全、密封性能和整体结构完整性的重要屏障。在高速运行环境下(常达300公里/小时或更高),车窗面临极端挑战,包括外部气压骤变(如隧道穿越)、雨水侵入风险、飞石或异物冲击,以及长期振动疲劳等。这些因素可能导致车窗失效,引发漏风、漏水、碎裂等事故,严重威胁乘客安全和列车运营稳定性。因此,动车组客室车窗检测是制造、维护和定期检修中的强制性环节,旨在通过系统化评估,确保车窗满足高强度、高密封性和优良光学性能的要求。检测过程覆盖从设计、生产到服役全生命周期,涉及多维度测试项目,采用齐全仪器和标准化方法,严格遵循国家及行业规范,以保障动车组在高速铁路网中的可靠性与安全性。
检测项目
动车组客室车窗检测包含一系列综合性项目,每个项目针对特定性能指标进行验证。核心检测项目包括:气密性测试(评估车窗在高速行驶中抵抗气压变化的能力,确保密封性以防止漏风或空调系统失效)、水密性测试(模拟降雨条件下车窗的防水性能,检查有无渗水现象,保障内部干燥和电气安全)、机械强度测试(如抗压强度和抗拉强度,验证车窗承受外部载荷的能力,避免因振动或冲击导致变形或破裂)、光学性能测试(测量透光率、紫外线阻隔率和眩光控制,确保视野清晰度和乘客舒适度,减少视觉疲劳)、抗冲击测试(模拟飞石或异物撞击场景,评估车窗的抗碎性和碎片防护等级),以及耐久性测试(通过循环温湿度变化和振动模拟长期使用,检测材料老化、密封圈寿命等)。这些项目共同构成车窗的整体性能评估框架,确保其在各种极端工况下保持可靠功能。
检测仪器
动车组客室车窗检测依赖于专用仪器,确保测试的精准性和可重复性。主要仪器包括:1. 压力测试仪(用于气密性测试,内置高精度传感器和真空系统,模拟列车高速运行下的正负压差,实时监测泄漏率);2. 水密性测试装置(配备喷淋系统和流量控制器,可调节水压和角度,模拟不同降雨强度,通过摄像头或湿度传感器检测车窗内部渗水情况);3. 万能材料试验机(执行机械强度测试,施加可控的拉伸、压缩或弯曲力,记录应力-应变曲线并评估极限强度);4. 光谱光度计(用于光学性能测试,测量透光率、反射率和紫外线透过率,确保车窗符合视觉舒适标准);5. 冲击试验机(进行抗冲击测试,以气动或电磁方式发射标准冲击物,如钢球或冰雹模拟物,记录破裂阈值和碎片分布);6. 环境模拟舱(结合温湿度控制器和振动台,进行耐久性测试,模拟极端气候和长期运行条件)。这些仪器均需校准至国家计量标准,确保数据可靠。
检测方法
动车组客室车窗检测采用标准化方法,确保过程高效且一致。具体方法包括:1. 气密性测试方法:将车窗安装在密封测试台上,施加阶梯式压力变化(如-3000Pa至+5000Pa),使用流量计测量空气泄漏量,计算气密性等级;2. 水密性测试方法:在喷淋装置下,以规定水压(如150-200L/m²/h)对车窗喷射15-30分钟,通过目视检查或电子传感器检测内部是否有水渍;3. 机械强度测试方法:在万能试验机上固定车窗样本,逐步增加载荷直至破坏,记录最大载荷和变形量,评估安全余量;4. 光学性能测试方法:利用光谱光度计在标准光源下(如D65光源)测量透光率,并分析眩光指数和紫外线阻隔率;5. 抗冲击测试方法:在冲击试验机中以规定速度(如50-100km/h)发射冲击物撞击车窗中心或边缘,评估破损模式和碎片尺寸;6. 耐久性测试方法:在环境模拟舱中进行温湿度循环(如-40°C至+80°C)和振动模拟(频率1-50Hz),持续数百小时,检查密封胶老化和结构完整性。所有方法均采用非破坏性测试优先原则,必要时辅以破坏性测试。
检测标准
动车组客室车窗检测严格遵循国家和国际标准,确保统一性和合规性。主要标准包括:1. 中国国家标准(GB/T),如GB/T 7106-2020《建筑门窗气密、水密、抗风压性能分级及检测方法》(适用于气密和水密测试),以及GB/T 11976-2022《建筑用安全玻璃光学性能试验方法》(规范光学测试);2. 铁路行业标准(TB/T),核心是TB/T 1979-2020《动车组车窗技术条件》,该标准详细规定车窗的材料要求、性能指标(如气密性泄漏率≤1.5m³/h·m²)、测试流程和验收准则;3. 国际标准,如ISO 16933:2007《玻璃在建筑中的抗冲击性能试验方法》(用于抗冲击测试)和EN 1279-5:2005《建筑玻璃中空玻璃的耐久性》(参考耐久性测试)。此外,检测过程还需符合质量管理体系标准如ISO 9001:2015,确保结果可追溯。检测报告必须包括实测数据、标准符合性声明和风险评估,未达标车窗需返修或报废。
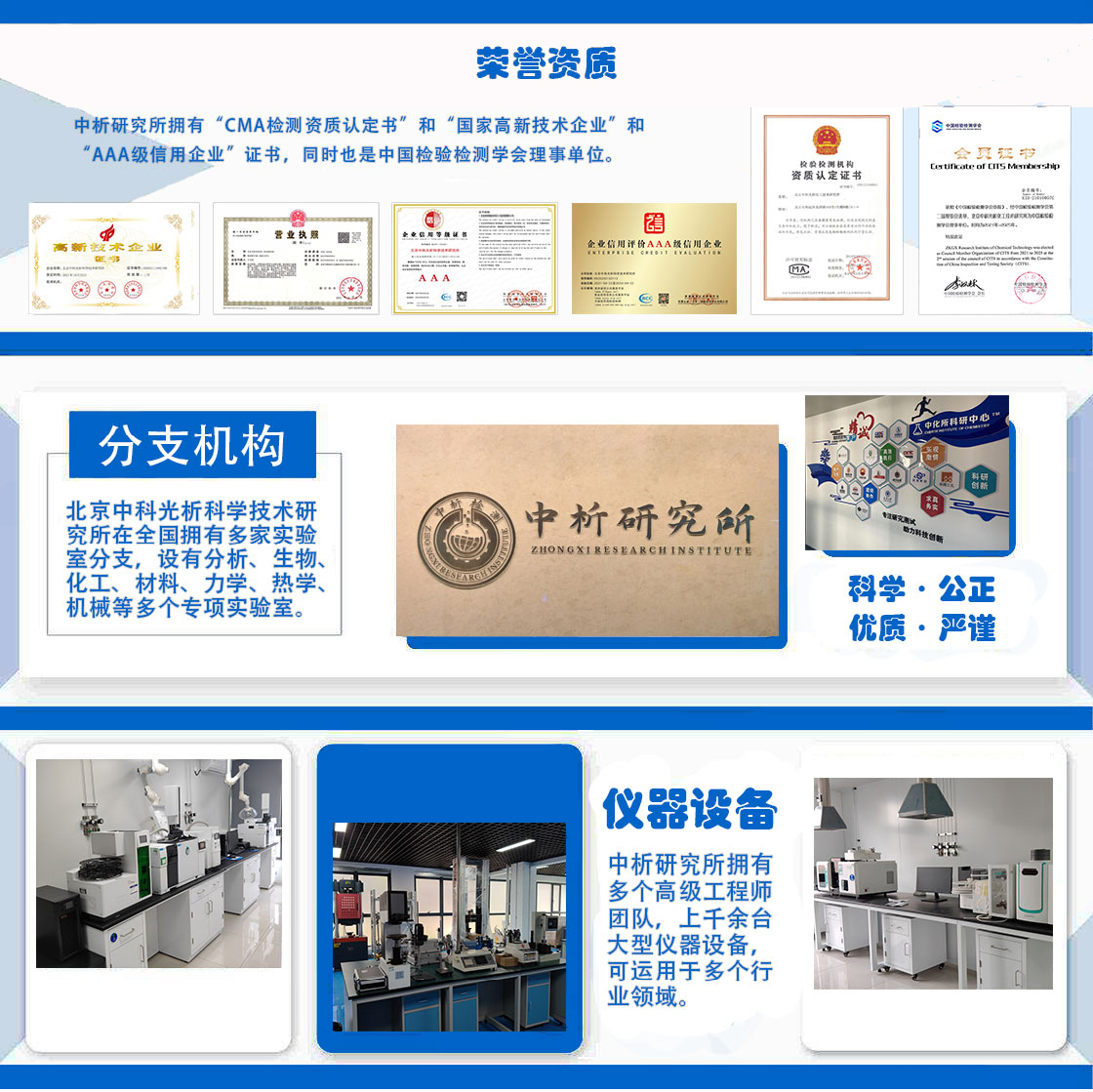
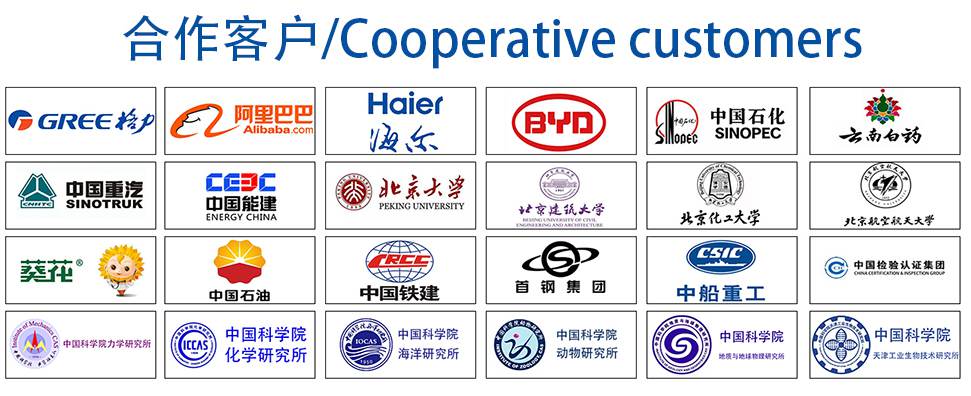