船舶部件检测介绍
船舶部件检测是海洋工程和造船行业的核心环节,它直接关系到船舶的安全性、可靠性和使用寿命。在航运业快速发展的背景下,船舶在恶劣的海洋环境中运行,包括高盐度海水、极端气候和频繁的机械负荷,导致部件易出现腐蚀、疲劳裂纹、变形或磨损等问题。这些缺陷如果不及时检测和修复,可能引发灾难性事故,如沉船或漏油事件。因此,船舶部件检测不仅是为了满足国际海事组织(IMO)和各国法规的要求,如SOLAS(海上人命安全公约),更是保障船员生命、环境保护和经济效益的关键措施。检测通常在船舶制造、维修、改装或定期检验阶段进行,涉及从船体、推进系统到电气设备的全方位检查。现代检测技术已从传统的人工目视发展到高度自动化的无损检测(NDT),大大提高了效率和准确性。通过系统化的检测流程,船东和船厂能优化维护计划、降低运营成本,并确保船舶在长达20-30年的服役期内安全航行。
检测项目
船舶部件检测涵盖多个关键项目,主要分为结构性和功能性两大类。结构性项目包括船体检测(如钢板焊接缝的裂纹、腐蚀厚度测量)、甲板和舱壁的变形评估,以及推进系统的轴系和螺旋桨的完整性检查。功能性项目则涉及机械部件(如阀门、泵和管道系统的泄漏或堵塞测试)、电气系统(如电缆绝缘和接地装置的电阻检测),以及安全设备(如消防和救生装置的可用性验证)。常见检测项目还包括疲劳裂纹检测(在高应力区域如舱口围板)、腐蚀速率评估(通过壁厚测量),以及材料性能测试(如金属硬度和韧性)。这些项目通常基于风险分析,优先关注高风险区域,例如易受海水侵蚀的压载水舱或关键传动部件。通过全面覆盖这些项目,检测能识别潜在故障点,预防事故发生。
检测仪器
船舶部件检测依赖于齐全的专用仪器,这些设备能高效、精准地完成无损检测任务。核心仪器包括超声波检测仪(UT),用于测量材料内部缺陷和壁厚,如手持式UT设备可扫描船体焊缝;磁粉探伤仪(MT),适用于铁磁性材料的表面裂纹检测,常用于轴系和齿轮检查;渗透检测设备(PT),用于非磁性部件如铝合金螺旋桨的表面缺陷识别;X射线和伽马射线检测仪(RT),能穿透厚实材料生成内部影像,用于焊接质量评估;涡流检测仪(ET),专用于导电材料如铜制电气部件的腐蚀检测。此外,现代仪器还集成数字技术,如便携式工业内窥镜用于管道内部可视化、激光扫描仪用于三维建模变形分析,以及红外热像仪用于电气系统热点检测。这些仪器通常具备数据记录功能,确保检测结果可追溯和自动化处理。
检测方法
船舶部件检测方法以无损检测(NDT)为主,旨在不破坏部件的前提下评估其状态,常见方法包括视觉检查、超声波检测、射线检测、磁粉检测和渗透检测。视觉检查是最基础的方法,通过目视或内窥镜观察表面缺陷,适用于初步筛查。超声波检测(UT)利用高频声波原理,当声波遇到缺陷时产生回波信号,用于深度测量内部裂纹或腐蚀,操作时需耦合剂确保声波传导。射线检测(RT)使用X射线或伽马射线穿透部件,通过胶片或数字成像显示内部结构,特别适合焊接缝的质量控制。磁粉检测(MT)通过磁化部件并施加磁粉,使表面裂纹显形,常用于铁质材料。渗透检测(PT)则应用染色剂渗透表面缺陷,经清洗后显示裂纹轮廓。此外,自动化方法如机器人辅助检测可应用于难以到达的区域。这些方法需结合人员培训和标准流程,确保数据一致性和可靠性。
检测标准
船舶部件检测严格遵循国际和行业标准,以确保一致性和合规性。主要标准包括ISO系列,如ISO 5817(焊接质量验收标准)、ISO 9712(无损检测人员资格认证要求),以及ISO 10893(管材检测规范)。船级社标准是核心依据,例如美国船级社(ABS)的Rules for Building and Classing Steel Vessels、挪威-德国船级社(DNV GL)的Ship Rules,和劳氏船级社(LR)的Rules and Regulations,这些标准详细规定了检测频率、方法和验收准则。国家层面,中国有GB/T标准如GB/T 2970(无损检测通则),同时IMO的公约如MARPOL(防止船舶污染公约)也影响环境相关部件的检测。标准通常强制要求定期检验(如5年入级检验),覆盖从设计、制造到维护的全生命周期。通过遵守这些标准,检测结果可在国际间互认,避免贸易壁垒。
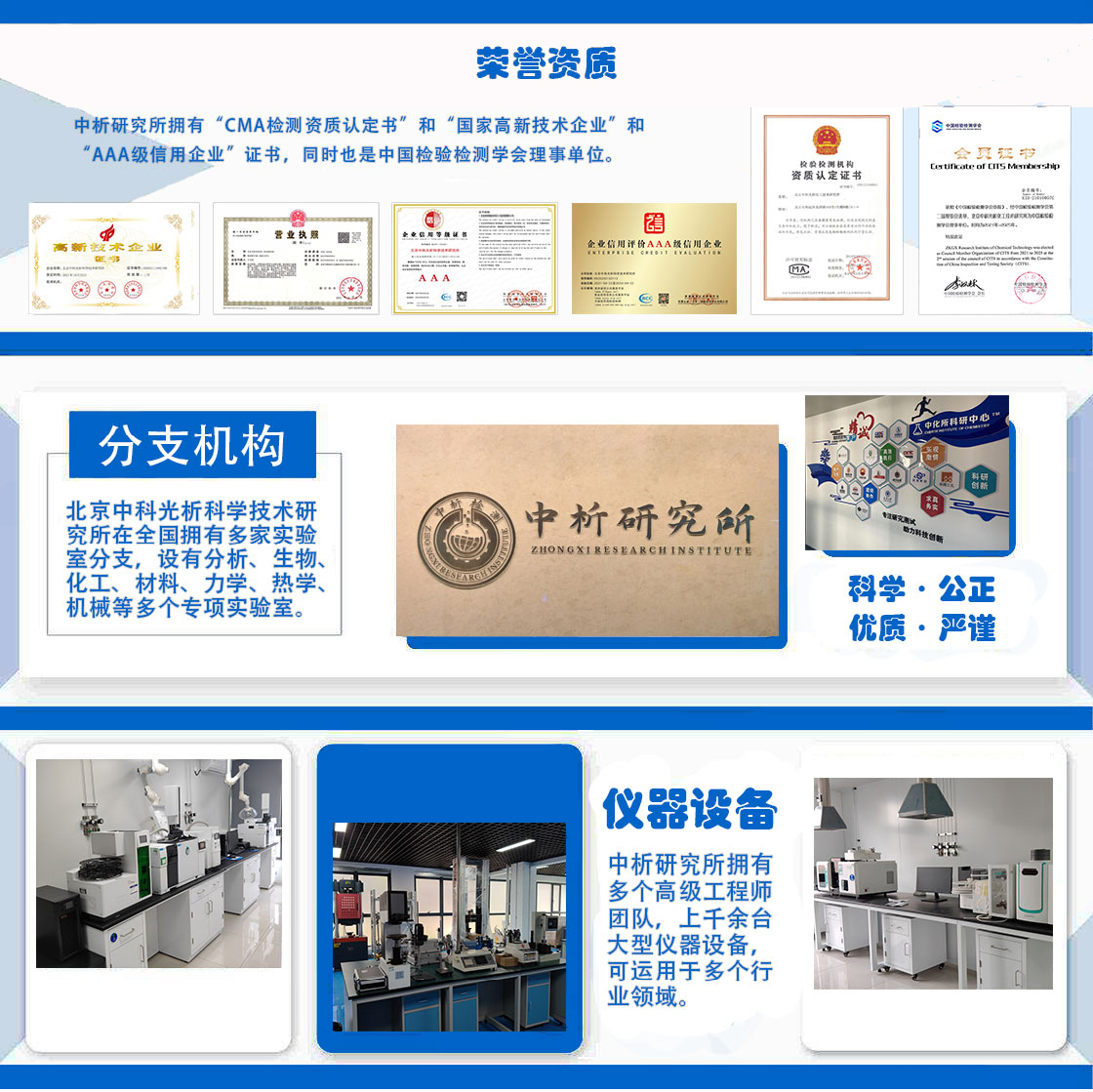
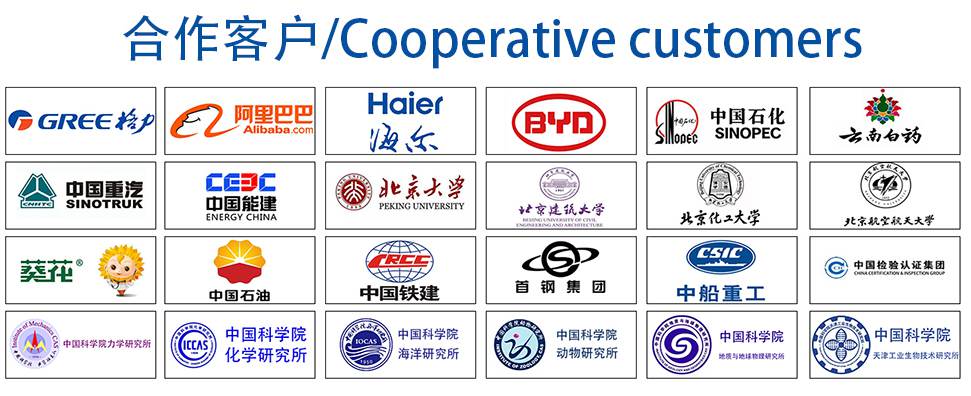