钢铸件是通过铸造工艺制造的钢制零部件,广泛应用于一般工程领域,如机械制造、建筑结构、汽车工业、船舶建造和能源设备等。这些铸件通常由碳钢或合金钢制成,具有高强度、耐磨性和抗冲击能力,是大型设备的核心组成部分。在工程应用中,钢铸件承受着高载荷、极端温度和环境腐蚀,因此其质量直接关系到整体系统的安全性和可靠性。缺陷如气孔、缩松、裂纹或成分偏差可能导致铸件失效,引发安全事故和经济损失。检测钢铸件是生产过程中不可或缺的环节,旨在验证其设计参数、材料性能和结构完整性。一般工程用钢铸件检测覆盖全生命周期,从原材料入厂到成品验收,涉及多学科技术,确保符合行业规范和客户要求。检测不仅提升产品合格率,还优化生产工艺,降低维护成本。总之,通过系统化的检测流程,钢铸件能在严苛的工程环境中高效服役。
检测项目
一般工程用钢铸件的检测项目主要包括化学成分分析、机械性能测试、无损检测和外观检验等。化学成分分析验证材料元素含量,如碳、锰、硅、硫、磷等,确保符合合金设计;机械性能测试涵盖拉伸强度、屈服强度、延伸率、冲击韧性和硬度,以评估铸件的承载能力;无损检测聚焦于内部缺陷,包括气孔、夹渣、裂纹和疏松;外观检验则检查表面粗糙度、尺寸精度和几何形状偏差。这些项目相互关联,能全面评估铸件质量,预防潜在失效。例如,机械性能测试在铸件承受动态载荷时至关重要,而无损检测则用于隐蔽缺陷的早期发现。
检测仪器
钢铸件检测常用的仪器包括光谱仪、万能材料试验机、硬度计、超声波探伤仪和磁粉探伤设备等。光谱仪(如直读光谱仪或X射线荧光光谱仪)用于快速精确地分析化学成分;万能材料试验机通过拉伸和压缩测试评估机械性能;硬度计(如布氏或洛氏硬度计)测量材料硬度以间接推断强度;超声波探伤仪利用高频声波探测内部缺陷的深度和尺寸;磁粉探伤设备则用于表面和近表面裂纹的视觉化。此外,金相显微镜用于微观组织观察,确保晶粒结构和热处理效果达标。这些仪器结合智能化软件,可自动化数据采集和分析,显著提升检测效率和准确性。
检测方法
钢铸件的检测方法涉及取样、测试和评价步骤。对于化学成分分析,采用取样熔炼法或原位光谱法,通过钻取铸件样品进行实验室化验;机械性能测试在标准试样上进行拉伸、冲击或弯曲试验,按照固定规程加载并记录数据;无损检测常用方法包括超声波法(发射声波检测回波异常)、磁粉法(施加磁场和磁粉显示裂纹)或渗透法(涂布染料凸显缺陷);外观检验则使用目视检查或3D扫描仪测量尺寸。检测过程强调标准化操作,如根据铸件尺寸选择合适的取样点,确保代表性。同时,方法需结合破坏性测试和非破坏性技术,以平衡效率和精度。
检测标准
钢铸件检测遵循国际和国家标准,以确保一致性和可比性。主要标准包括ASTM A703(美国材料与试验协会标准,涵盖一般工程铸件的化学和机械要求)、ISO 4990(国际标准化组织标准,规定铸钢件的通用技术条件)以及GB/T 11352(中国国家标准,针对一般工程用铸钢件)。这些标准详细定义了检测项目限值、仪器校准要求和测试方法,如ASTM E8用于拉伸试验,ISO 10675用于无损检测验收等级。此外,行业特定标准如EN 10293(欧洲标准)也适用。遵守这些标准可保证检测结果的可追溯性,并支持跨地区认证,满足工程项目的质量保证体系。
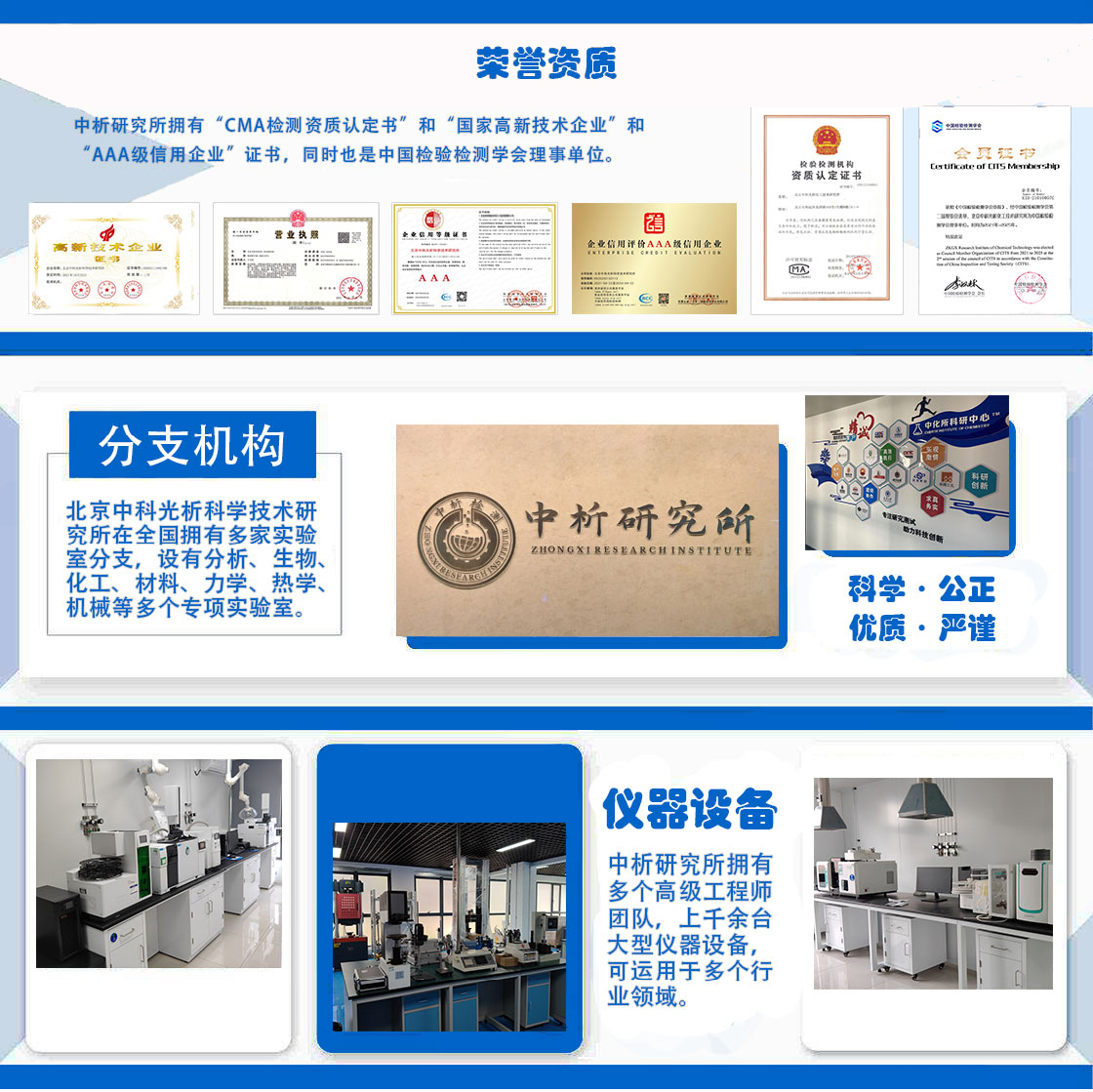
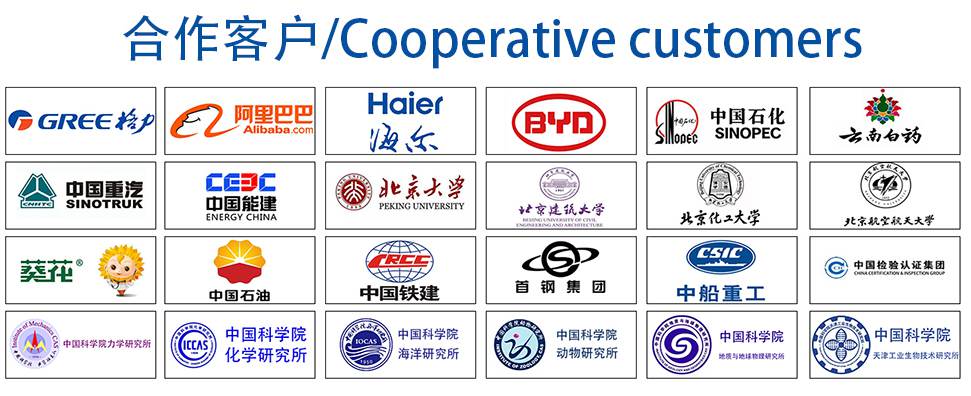