洞眼检测的重要性及背景
洞眼检测是工业生产和材料质量控制中的关键环节,主要针对金属、塑料、复合材料等产品表面的孔洞、裂纹或微小缺陷进行系统性分析。在汽车制造、航空航天、电子设备、包装材料等领域,产品表面的完整性直接影响其密封性、强度及耐久性。例如,铸件中的气孔可能引发结构失效,薄膜材料的微孔会导致渗透问题。随着精密制造技术的提升,检测精度需求已从毫米级向微米级甚至纳米级延伸,这对检测方法、仪器和标准提出了更高要求。
洞眼检测的核心项目
检测项目根据应用场景可分为以下五类:
1. 孔洞位置与分布:分析缺陷在材料表面的空间排列规律
2. 孔径尺寸与深度:量化孔洞的几何参数并通过阈值判定是否合格
3. 形状特征分析:区分圆形气孔、不规则裂纹或加工残留痕迹
4. 单位面积密度:计算缺陷在特定区域的出现频率
5. 穿透性检测:判断孔洞是否贯穿材料整体结构
主流检测仪器与技术
现代洞眼检测主要依托以下设备实现:
- 光学显微镜:配备图像分析软件,适用于0.1mm以上缺陷检测
- 工业CT扫描仪:实现三维断层成像,分辨率可达5μm
- 激光共聚焦扫描仪:通过点云重建获取微米级表面形貌数据
- 超声波探伤仪:检测材料内部闭合性缺陷的深度信息
- X射线实时成像系统:适用于高速在线检测场景
检测方法与技术路线
目前应用最广泛的检测方法包括:
1. 目视检查放大法:采用10-100倍放大镜进行初步筛查
2. 光学成像分析法:结合机器视觉系统实现自动识别与分类
3. 三维扫描重建法:通过点云数据生成缺陷三维模型
4. 无损检测技术:包括涡流检测、渗透检测等特殊方法
5. AI智能判读系统:基于深度学习的自动化缺陷识别技术
检测标准体系
国内外主要执行以下标准规范:
- ISO 10360:几何量测量设备性能评定标准
- ASTM E1441:工业射线检测通用标准
- GB/T 24637:产品几何技术规范表面缺陷检测要求
- VDI/VDE 2630:光学三维测量系统校准规范
- JIS Z 2344:渗透探伤检测方法标准
根据行业应用差异,各企业可结合ISO 9001质量管理体系制定具体验收标准,通常要求关键部位缺陷尺寸不超过材料厚度的5%,单位面积缺陷密度小于0.5个/cm²。随着智能制造的推进,基于大数据的过程控制标准正在成为新的发展方向。
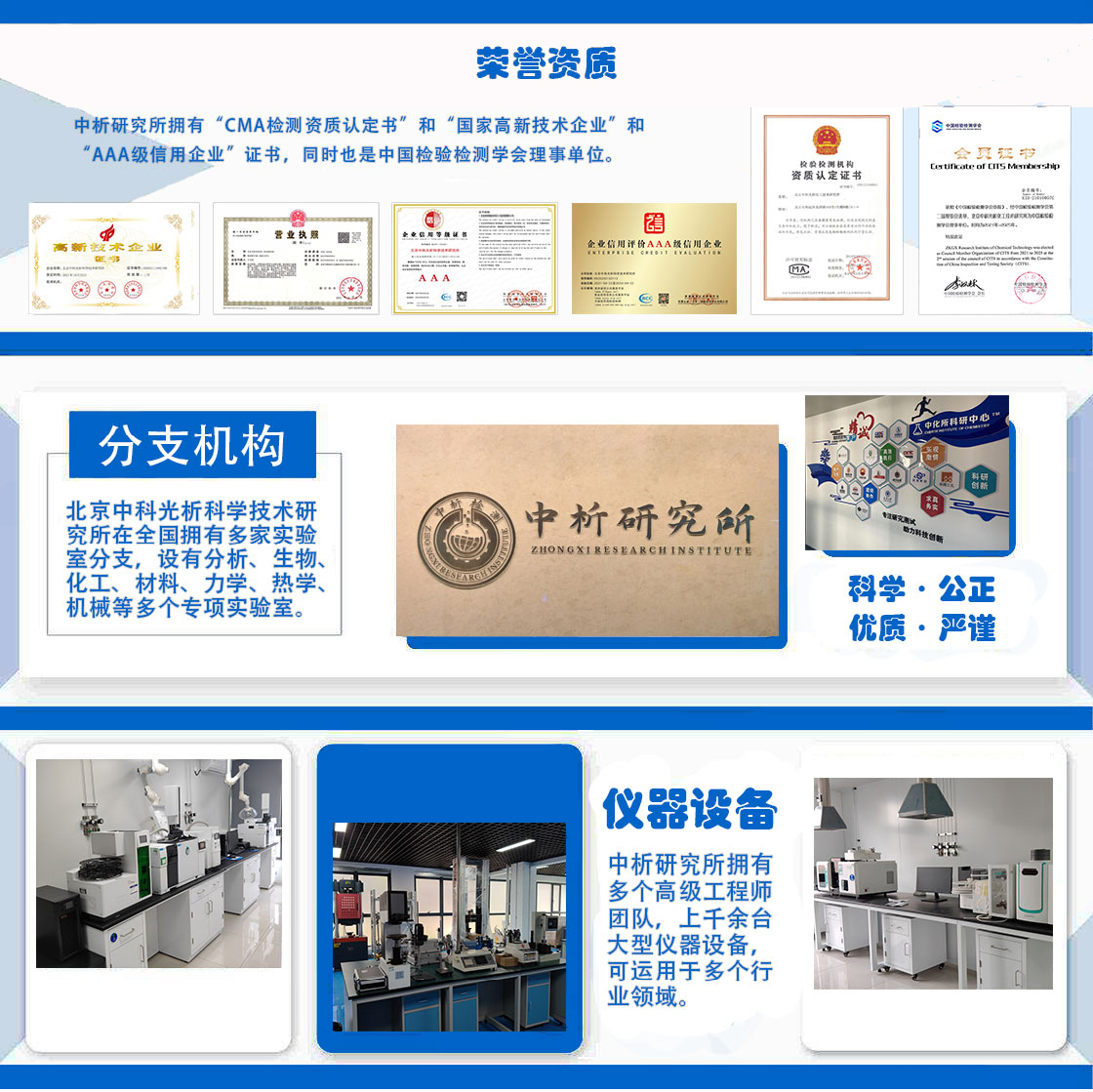
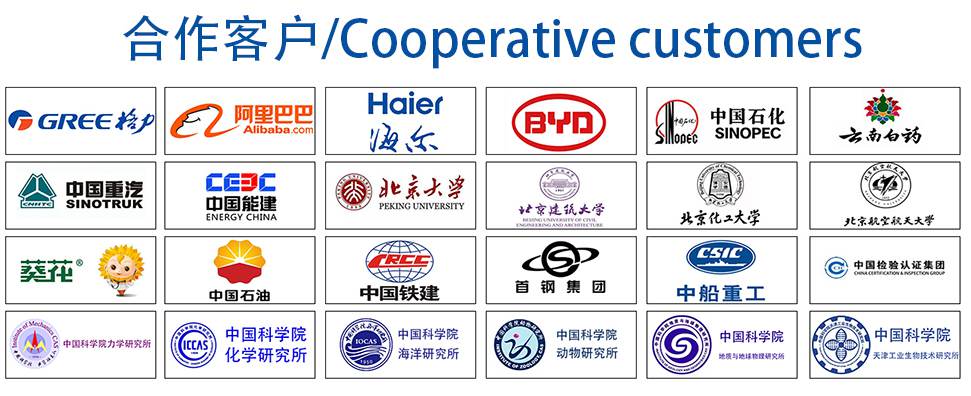