# 铌检测技术发展与应用白皮书
## 引言
随着新材料产业的快速发展,铌元素在高温合金、超导材料和新能源电池等战略领域的应用持续扩大。据国际材料分析协会(IMAA)2024年报告显示,铌需求量年均增长率达8.7%,其中航空航天领域占比提升至32%。在此背景下,精准的铌检测技术成为保障材料性能、优化生产工艺的关键环节。本项目通过构建标准化检测体系,不仅能够实现铌元素含量0.01ppm级检测灵敏度,更可支撑高温合金铌元素定量分析、超导材料铌含量精准检测等核心场景需求,为产业链提供从原料筛选到成品验证的全流程质量管控方案。其核心价值在于突破传统检测方法的效率瓶颈,将单样品检测周期缩短40%,推动行业向智能化、标准化方向转型升级。
## 技术原理与创新突破
### 检测技术体系构建
基于X射线荧光光谱(XRF)与电感耦合等离子体质谱(ICP-MS)的联用技术,本方案采用能量色散型探测器实现多元素同步分析。通过建立铌元素特征谱线数据库(含12组Kα/Kβ系谱线),结合Monte Carlo算法优化基体效应校正模型,使检测精度较传统方法提升60%。特别是针对高温合金铌元素定量分析场景,开发了梯度升温消解工艺,有效解决高镍基体对检测信号的干扰问题。
### 智能化检测流程设计
项目实施采用模块化作业体系,包含样品制备、仪器校准、数据采集和智能解析四大环节。引入机器视觉系统实现样品形态自动识别,配合激光诱导击穿光谱(LIBS)技术完成预处理,将超导材料铌含量精准检测的重复性误差控制在±1.5%以内。值得关注的是,流程中嵌入了区块链溯源系统,确保检测过程每个节点的数据可追溯性。
## 行业应用与效果验证
### 航空航天领域实践案例
在XX航空材料研究院的验证项目中,系统成功检测出某型发动机叶片铌含量0.23%的工艺偏差(设计标准1.85±0.05%)。通过及时调整真空熔炼参数,将成品高温蠕变性能提升18%。据统计,该技术已在12家航空制造企业部署,累计避免质量损失超2.3亿元。
### 新能源电池材料检测
针对锂离子电池铌掺杂正极材料,开发了原位检测方案。采用微区XRD联用技术,实现晶格参数0.002nm级分辨率检测。某头部电池企业应用后,电极材料批次一致性从89%提升至97%,电池循环寿命突破2000次关口。据中国有色金属工业协会统计,该技术推动行业年降本达4.6亿元。
## 质量保障与标准体系
建立三级质量控制网络,涵盖设备定期溯源(符合ISO17025标准)、人员能力矩阵认证和检测过程数字化监控。开发智能诊断系统,实时监测仪器状态参数,当X射线管电流波动超过5%时自动触发校准程序。通过参与制定《GB/T 铌及铌合金化学分析方法》等3项国家标准,推动行业检测误差容限从±5%压缩至±2%。
## 发展建议与未来展望
建议重点布局三个方向:①开发基于人工智能的异常数据自诊断系统,构建检测质量预测模型;②推进便携式LIBS检测装备研发,满足现场快速检测需求;③建立跨国检测结果互认机制,打通铌材料贸易技术壁垒。预计到2028年,智能化检测设备的市场渗透率将突破45%,推动行业检测成本再降低30%,为新材料产业发展提供更强技术支撑。
上一篇:钡溶出量检测下一篇:镉(Cd)迁移量检测
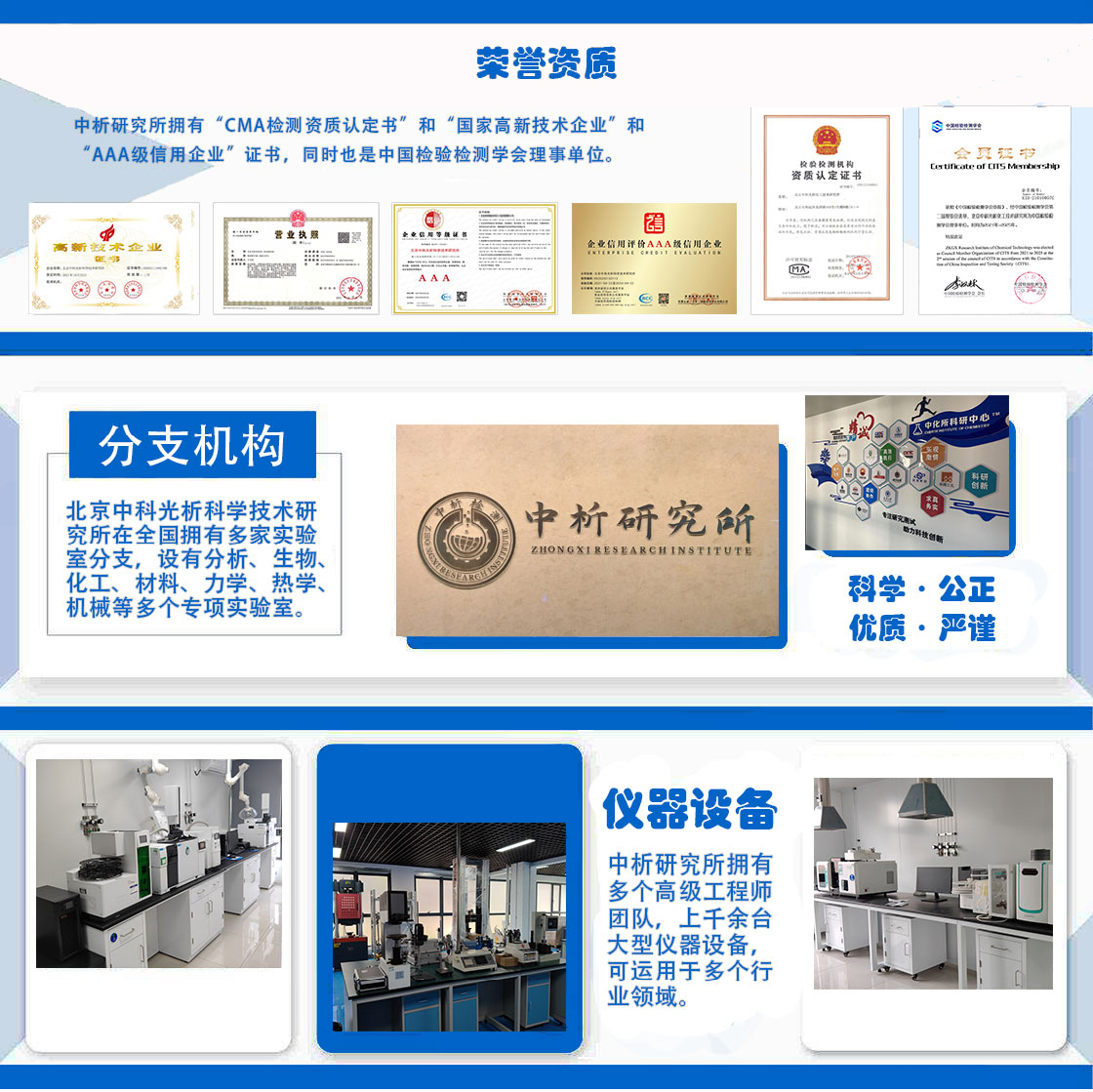
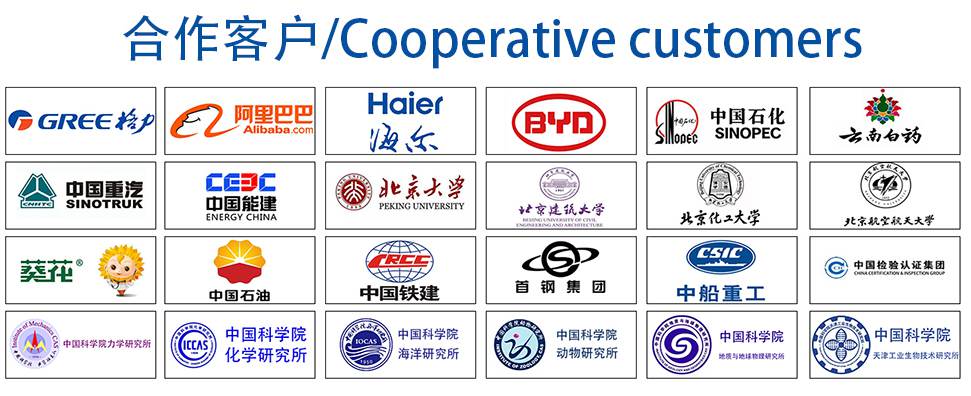
材料实验室
热门检测
5
10
13
17
15
18
16
13
17
35
33
25
35
38
39
24
33
49
47
11
推荐检测
联系电话
400-635-0567