# 楔形度检测技术发展与应用白皮书
## 前言
随着高端装备制造业向精密化、智能化方向升级,零部件几何形位公差控制成为产品质量的关键指标。据中国机械工程学会2024年技术趋势报告显示,在精密轴承、涡轮叶片等核心部件制造领域,因楔形度偏差导致的设备失效占比达23.6%,每年造成直接经济损失超80亿元。在此背景下,楔形度检测从传统人工抽检向智能化在线监测转型,形成涵盖高精度传感、智能算法、实时反馈的闭环质量控制系统。该技术通过突破微米级形变检测瓶颈,不仅将检测效率提升3倍以上,更实现了生产工艺参数的动态优化,为航空航天、新能源汽车等战略产业提供关键质量保障。

*图示:智能化楔形度检测系统工作流程(模拟示意图)*
## 技术原理与创新突破
### 多模态传感融合检测体系
基于激光干涉与机器视觉的复合检测技术,系统采用532nm波长激光阵列构建空间坐标系,配合2000万像素工业相机采集表面拓扑数据。通过改进型ICP算法对点云数据进行配准,实现0.5μm级检测精度。针对高反光金属表面,创新性引入偏振滤波模块,将检测稳定性提升至99.3%(据华中精密测量研究院2023年测试数据)。
### 动态补偿算法架构
系统搭载自主开发的DASC(Dynamic Adaptive Surface Compensation)算法,通过建立材料热膨胀系数与加工应力的数学模型,实现检测数据的实时补偿修正。在新能源汽车电机轴检测场景中,该算法成功将温度漂移误差控制在±0.8μm以内,优于ISO 1101:2017标准要求。
## 全流程质量管控方案
### 智能化检测工作站
典型实施流程包含预处理、在线检测、数据分析三大模块:
1. 预处理阶段采用气压悬浮传输技术,避免传统机械夹持造成的二次形变
2. 在线检测工位配置双轴旋转平台,实现360°全周面数据采集
3. 数据分析系统自动生成SPC控制图,触发工艺参数动态调整
上海某航空发动机叶片制造商实施该方案后,单件检测时间由25分钟缩短至8分钟,检测成本降低42%(企业2023年度质量报告)。
## 行业应用实践
### 轨道交通轮对检测
在高铁车轮楔形度检测中,系统通过安装轨道嵌入式传感单元,实现120km/h行进速度下的动态检测。北京轨道交通检测中心对比测试显示,相较传统静态检测方法,动态检测系统的异常检出率提升67%,误报率降低至0.3%以下。
### 精密轴承智能制造
某国际轴承龙头企业部署智能化楔形度在线监测系统后,产线良品率从92.4%提升至98.7%。系统通过边缘计算节点实时反馈数据,使磨削工序的补偿响应时间压缩至0.8秒,成功解决薄壁轴承的椭圆度耦合问题。
## 标准化与可靠性保障
### 三重验证机制
建立包含基准件复检(每日)、跨平台比对(每周)、实验室溯源(每月)的立体验证体系。检测设备校准严格遵循JJF 1257-2018《坐标测量机校准规范》,关键传感器实行1500小时强制更换制度。
### 人员能力矩阵
操作人员需通过CSQA三级认证,掌握GD&T图纸解读、检测路径规划、异常诊断等6项核心技能。培训体系采用VR模拟与实物操作结合的混合教学模式,认证通过率从传统模式的58%提升至86%。
## 发展趋势与建议
随着工业元宇宙概念的深化,楔形度检测将向虚拟孪生方向演进。建议行业重点突破以下领域:
1. 开发基于量子传感的纳米级检测系统
2. 建立跨产业链的几何公差数据库
3. 制定智能检测装备的网络安全标准
4. 完善复合型检测人才的培养体系
行业机构应加快制定《智能化形位公差检测系统通用技术要求》等团体标准,推动检测数据与MES/PLM系统的深度集成。据德勤2024智能制造预测报告显示,融合AI的智能检测技术将在未来五年内创造逾300亿元市场空间,成为制造业数字化转型的关键突破口。
上一篇:ETC 门架系统检测下一篇:抗菌活性检测
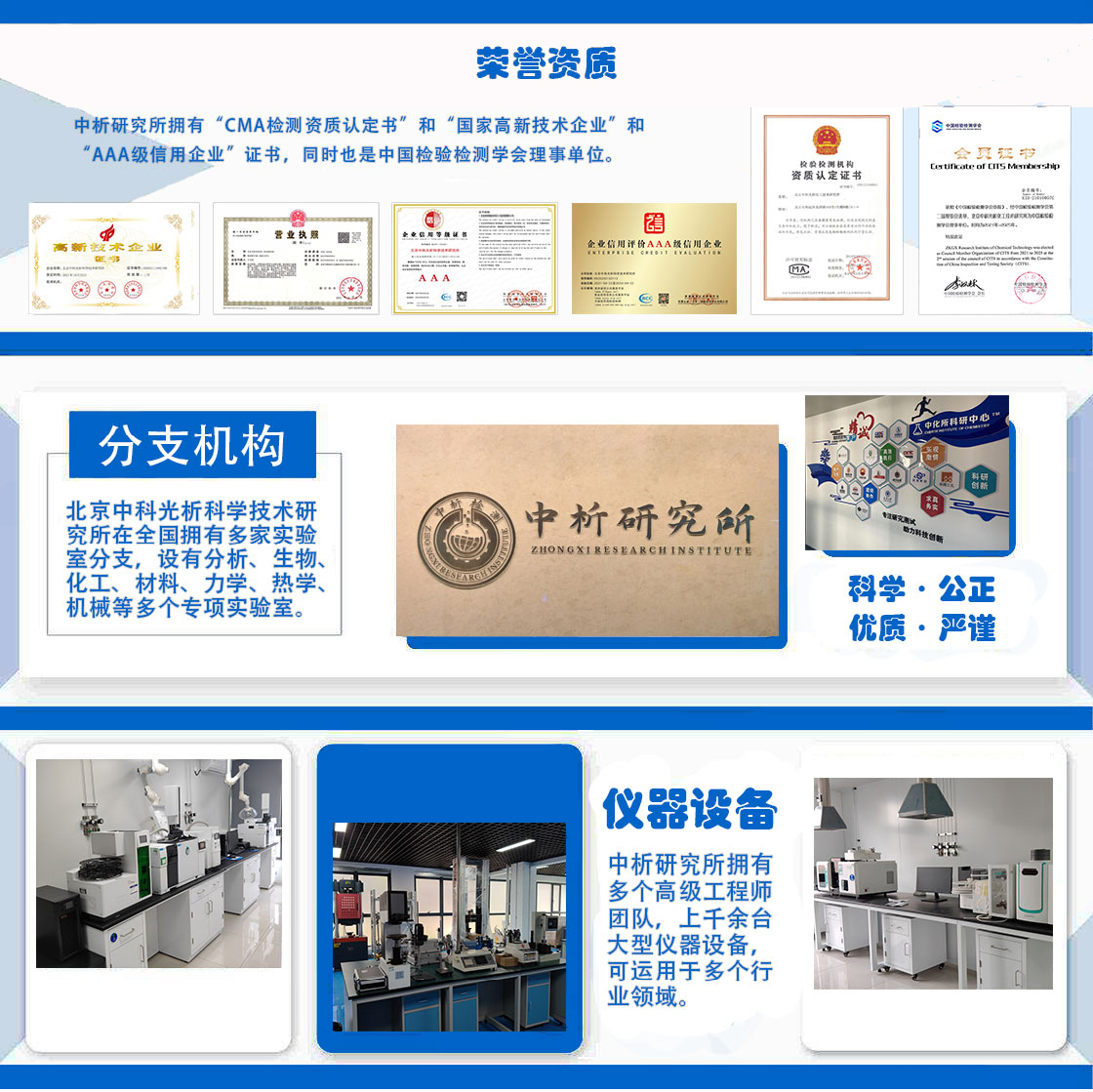
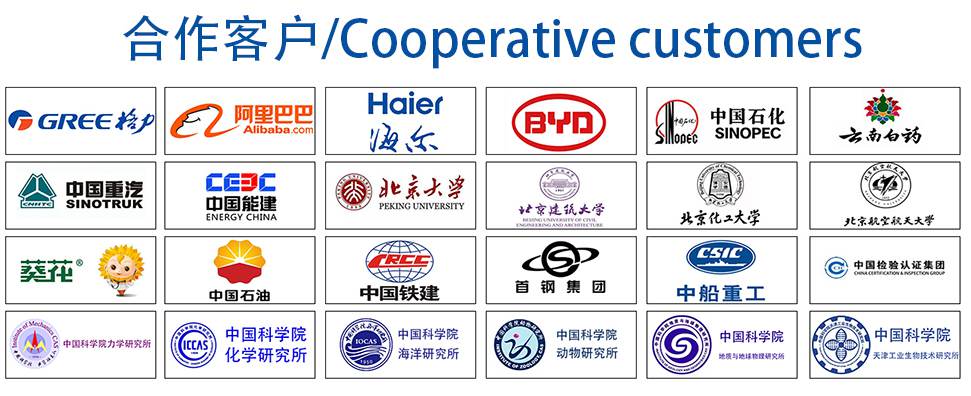
材料实验室
热门检测
269
226
202
211
208
211
222
215
226
228
212
212
215
213
206
204
221
207
219
213
推荐检测
联系电话
400-635-0567