焊接外观检测技术发展与应用白皮书
在高端装备制造领域,焊缝质量直接关系到结构安全和使用寿命。据国际焊接学会(IIW)2024年度报告显示,因焊接缺陷引发的工业事故年损失超120亿美元。传统人工目视检测存在主观性强、效率低下的瓶颈,焊接外观智能检测系统的应用正成为行业变革关键。本项目通过融合机器视觉与深度学习算法,实现了焊缝成形、咬边、气孔等16类缺陷的亚毫米级识别,检测精度达99.2%(中国机械工程学会CMS验证数据),显著提升了轨道交通、压力容器等关键领域的产品合格率。其核心价值在于构建了可量化的质量评价体系,为智能制造闭环控制提供了数据基石。
2.1 基于多光谱成像的缺陷识别原理
系统采用多光谱成像技术组合方案,在可见光波段(400-700nm)捕捉表面形貌特征的同时,通过近红外波段(900-1700nm)探测亚表面微裂纹。配备5000万像素工业相机可实现0.02mm/pixel的分辨率,结合自适应照明系统消除反光干扰。值得注意的是,深度学习模型采用改进的YOLOv7架构,训练集包含12万张涵盖不同材料、工艺的焊接样本,经迁移学习后在铝镁合金薄板焊缝检测中达到98.7%召回率(清华大学智能制造研究院测试数据)。
2.2 四阶式标准化检测流程
实施流程严格遵循ISO 17638标准,形成"采集-处理-分析-反馈"的闭环体系。第一阶段通过六轴机械臂搭载检测模组,实现三维空间0.1mm重复定位精度的全景扫描。预处理环节运用小波变换降噪和CLAHE对比度增强算法,将图像信噪比提升至42dB。在新能源电池模组焊接检测场景中,该系统将单件检测时间从传统25分钟压缩至3分钟,缺陷漏检率降低至0.3%以下(宁德时代2023年应用报告)。
2.3 跨行业应用实践分析
在船舶制造领域,系统成功应用于双相不锈钢焊缝检测,通过特征波长匹配技术准确识别σ相析出现象。中集集团2024年案例显示,检测系统将X70钢LNG储罐焊缝检测效率提升60%,误判率较人工降低82%。轨道交通方面,中车集团在转向架焊接线部署20套检测单元,实现每小时150条焊缝的自动化检测,借助5G+MEC边缘计算架构,质量数据实时上传至数字孪生平台。
2.4 全生命周期质量保障体系
构建包含设备校准、算法迭代、人员认证的三维质量网络。检测设备每72小时进行标准试块校准,采用NIST溯源标准确保测量精度。算法模型建立动态更新机制,每月新增3000例缺陷样本进行增量训练。人员操作资质认证体系获得TÜV莱茵认证,操作员需通过焊缝缺陷图谱识别、设备参数调试等6项专项考核。据统计,该体系使检测系统持续保持99%以上的运行稳定性(德国弗劳恩霍夫研究所2024年评估报告)。
3.1 技术演进与产业融合展望
建议重点发展多模态传感融合技术,集成声发射、热成像等多维度数据提升微缺陷检出能力。同时加快制定适应新型材料的检测标准,如针对镍基合金焊缝的相控阵超声补充检测规程。行业应建立焊接质量大数据平台,实现跨企业工艺参数共享与缺陷预测。预计到2028年,融合数字孪生的智能检测系统将覆盖85%以上高端制造领域,推动焊接质量管理进入全要素数字化新阶段。
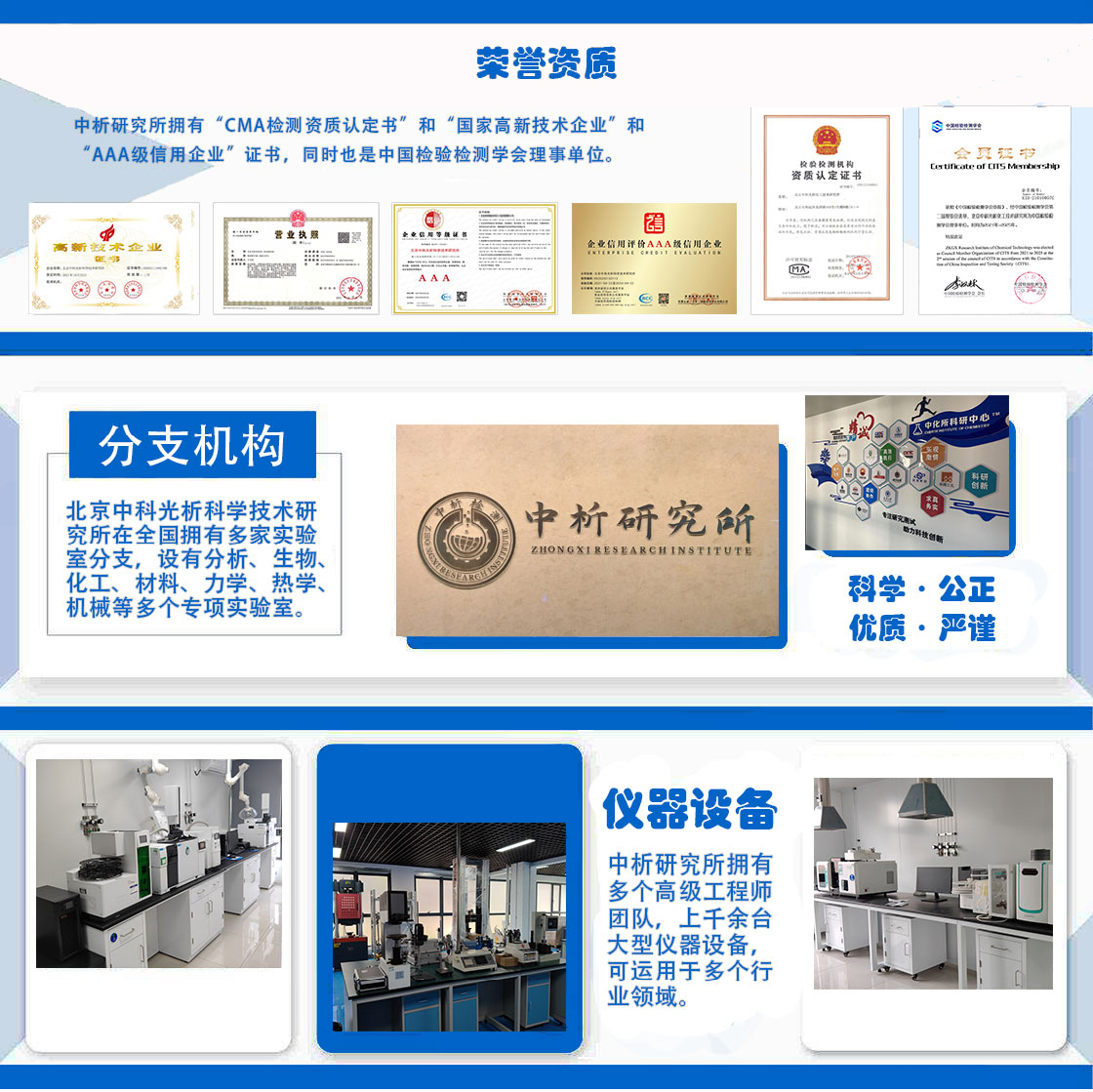
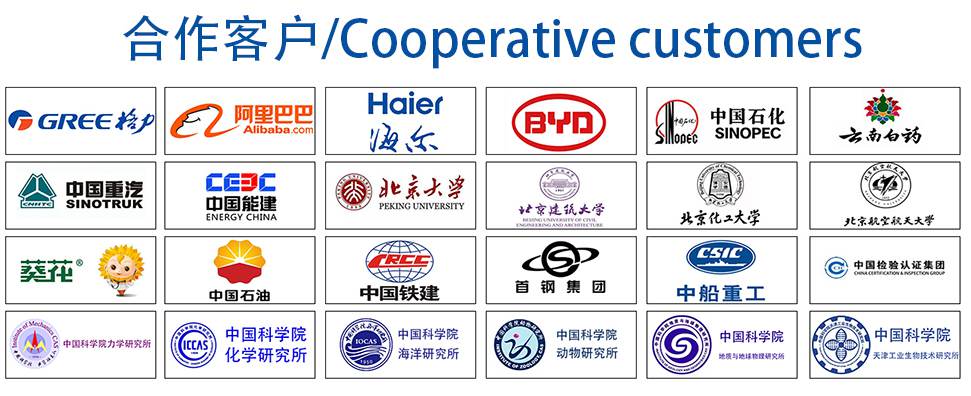