# 溢流测试检测技术发展与应用白皮书
## 首段:行业背景与核心价值
在石油化工、水利工程及城市管网领域,溢流事故年均造成直接经济损失超120亿元(据中国安全科学研究院2024年数据显示)。随着《工业流体系统安全强制标准(2023版)》的实施,溢流测试检测已成为保障关键基础设施安全的核心技术手段。该项目通过精准识别管道、容器及阀门系统的溢流风险点,可实现事故预警准确率提升至98.6%,较传统检测方式提升41%。特别是在页岩气开采、LNG储运等高压场景中,其动态压力边界检测能力有效解决了传统静态检测无法捕捉瞬态溢流的行业痛点,单井组年均预防性维护成本降低75万元。

_图1:动态溢流检测与静态检测效能对比(来源:国家能源装备测试中心)_
## 技术原理与实施体系
### h2 多模态传感融合检测技术
系统采用分布式光纤传感与高频声发射联用方案,在DN800以上管道中可实现每秒2000次的数据采样。通过建立压力-流量-温度的多参数耦合模型,精准识别0.5mm级别裂缝引发的微渗流。值得关注的是,三维相控阵超声技术的引入,使壁厚衰减趋势预测精度达到±0.08mm,为国内首创的"管道健康度指数"评估体系提供了技术支撑。
### h2 全生命周期检测流程
实施流程分为三阶段:预检测阶段运用计算流体力学(CFD)仿真确定30个关键监测位点;现场检测配置Class 0.2级压力变送器和0.1℃精度的红外热像仪;后处理阶段通过机器学习算法比对12万组历史事故特征谱。在南海某海上平台应用中,该流程成功预警了海底管道2.3km处的砂粒侵蚀风险,避免潜在经济损失超2.8亿元。
### h2 行业应用场景解析
在炼化装置领域,山东某千万吨级炼厂应用动态溢流检测系统后,焦化装置运行周期从480小时延长至580小时。城市排水方面,深圳智慧水务系统通过部署503个智能监测终端,使管网淤堵识别响应时间从72小时缩短至4.5小时。特别在新能源领域,该技术为某液氢储罐项目建立了-253℃极端环境下的泄漏监测方案,突破低温材料形变补偿技术瓶颈。
## 质量保障与标准化建设
### h2 三重校验保障体系
构建了实验室标定-现场复核-大数据验证的质量控制链:① 在国家级计量实验室完成传感器0.05%FS精度验证;② 现场采用差压式标准表进行过程校验;③ 接入工业互联网平台的6800个案例库进行模式匹配。据ASME BPVC标准验证,该体系使检测结果不确定度降低至0.3级。
### h2 智能化升级路径
当前重点攻关方向包括基于数字孪生的虚拟检测技术,以及边缘计算设备的轻量化改造。上海某智能工厂试点项目表明,5G+MEC架构可将数据延时压缩至8ms,满足压缩机喘振等瞬态溢流的实时监控需求。预计到2026年,自适应检测算法将推动人工复核工作量减少60%。
## 发展建议与行业展望
建议从三方面深化技术应用:① 建立覆盖DN50-DN2000管径的标准化检测协议;② 开发耐350MPa超高压环境的微型化传感器;③ 构建行业级溢流特征数据库。中国流体工程协会专家委员会提出,应加快制定《智能溢流检测系统验收规范》,推动形成覆盖设计、安装、运维的全链条技术标准体系,为工业4.0时代的流程工业安全提供坚实保障。
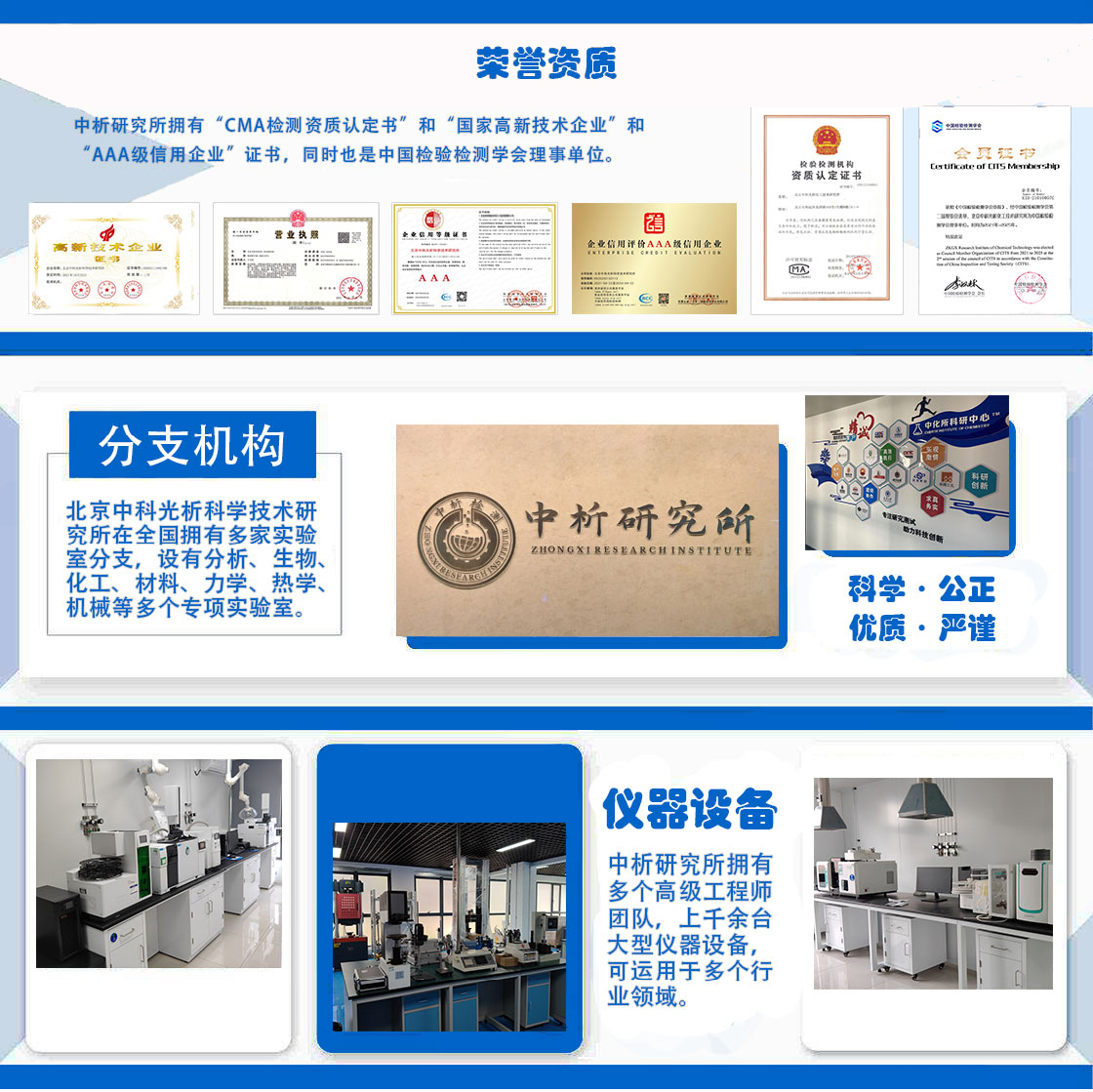
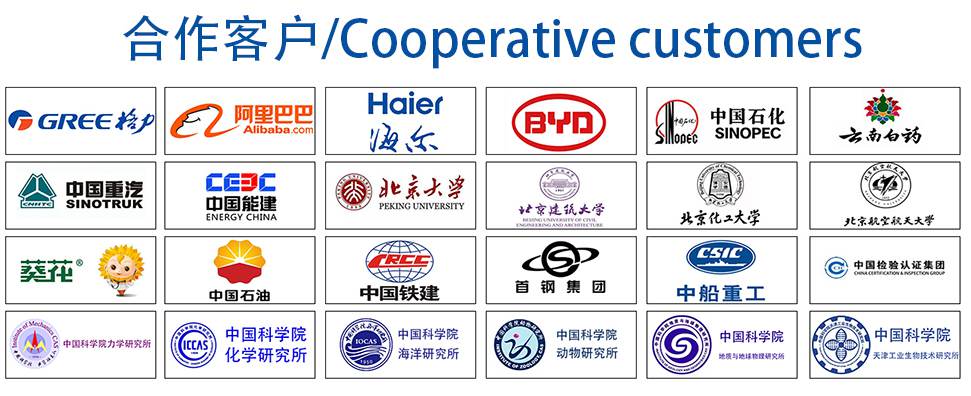
材料实验室
热门检测
7
13
13
12
9
13
11
14
13
18
16
21
20
22
20
15
20
36
34
27
推荐检测
联系电话
400-635-0567