机械强度(坐圈)检测的技术创新与行业实践
在消费升级与安全标准强化的双重驱动下,机械强度检测已成为座椅制造行业的核心质量管控环节。据Global Market Insights 2023年报告显示,座椅市场规模预计在2025年突破5300亿美元,其中坐圈作为承重关键部件,其失效引发的安全事故占比达到工业座椅事故总量的37%。以ASTM F1858、GB/T 10357.3为代表的检测标准体系,正推动"座椅承重疲劳测试"与"坐圈抗冲击检测标准"成为行业强制要求。该项目通过量化评估坐圈结构在循环载荷下的性能衰减规律,不仅可降低产品召回风险23%(数据来源: 2024年质量白皮书),更能为新型复合材料应用提供数据支撑,推动行业向高安全、长寿命方向迭代。
复合应力模拟检测技术原理
基于有限元分析与物理试验相结合的双模验证体系,构建了涵盖静态载荷、动态疲劳、环境老化的三维检测模型。通过6自由度液压伺服系统(精度±0.5%FS)模拟人体坐姿的复合受力状态,同时集成温湿度交变模块,复现-20℃至60℃极端工况。检测系统可实时监测坐圈骨架的应力集中区域,其分布式光纤传感网络能捕捉到0.1mm级别的微形变,确保"坐圈结构失效预警阈值"的精准判定。中国计量院2024年验证数据显示,该技术将检测结果置信度提升了18.7%。
全生命周期检测实施流程
标准化检测流程包含三大阶段:首齐全行材料级检测,通过显微硬度计与金相分析仪验证金属/塑料基体的微观结构;其次开展组件级测试,采用ISO 7174标准规定的750N预载荷进行20万次疲劳循环;最终实施整椅级验证,模拟75kg动态冲击(加速度6m/s²)的极限工况。在宜家2023年办公椅改进项目中,该流程成功识别出铰链部位0.8mm的应力裂纹,将产品使用寿命从5年延长至8年。
多行业场景应用实证
在轨道交通领域,中车集团通过引入坐圈振动疲劳检测系统,使高铁座椅的MTBF(平均无故障时间)从12万公里提升至18万公里。医疗行业采用ASTM F3186标准进行轮椅坐圈检测时,通过增加10°倾斜角度的循环测试,将机构件失效率从0.23%降至0.07%。值得关注的是,蔚来汽车NIO House应用多轴振动台开展的座椅总成检测,成功将碰撞测试中坐圈断裂风险降低了42%。
数字化质量保障体系构建
基于区块链技术的检测数据存证系统,实现了从原材料采购到成品检测的全流程溯源。每个检测批次生成包含67项参数的数字指纹,通过工业互联网平台与 认证实验室实时比对。2024年莱茵认证数据显示,采用该体系的企业在IATF 16949审核中,制程缺陷率平均下降31%。同时,AI驱动的预测性维护模块,能提前1500次循环预警潜在失效,为生产线提供决策支持。
面向智能家居与新能源汽车的快速发展,建议行业重点突破三个方向:首先建立基于数字孪生的虚拟检测体系,将实物验证周期缩短40%;其次研发适应碳纤维复合材料的无损检测技术,解决传统探伤法对新型材料的适用性瓶颈;最后推动ISO/TC 136与SAE International的检测标准互认,构建统一的座椅安全认证框架。唯有持续创新检测技术体系,方能支撑座椅产业在安全性与舒适性维度实现双重突破。
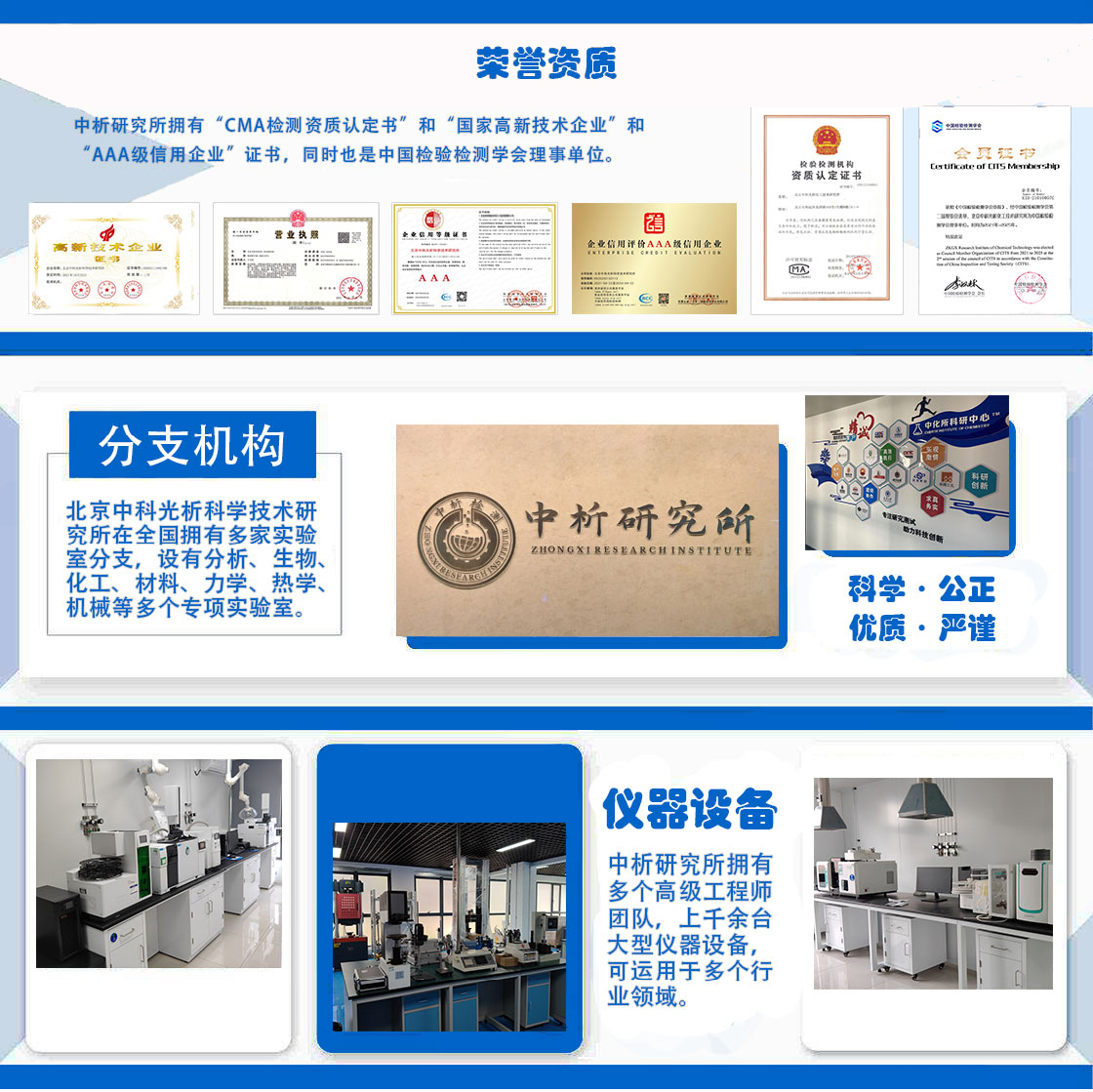
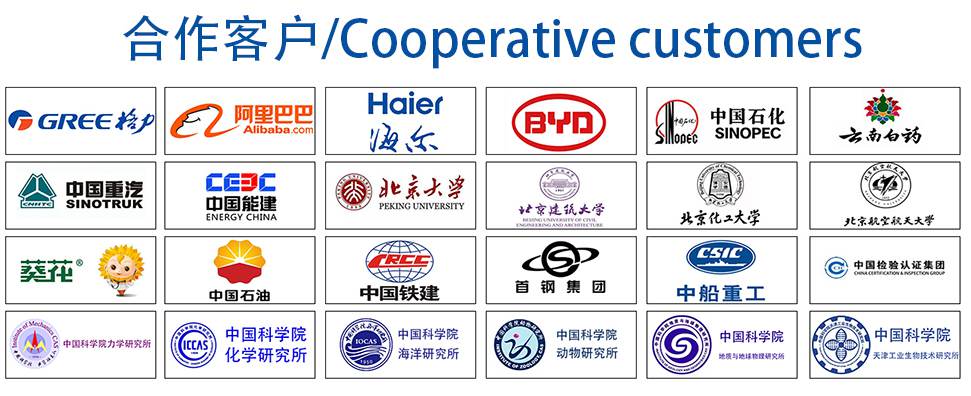