# 管道输送特征检测技术白皮书
## 引言
随着能源运输网络规模突破650万公里(据国际管道研究协会2024年数据),管道输送特征检测已成为保障能源动脉安全运行的核心技术。在油气、化工等领域,因腐蚀、机械损伤导致的管道失效事故年均造成直接经济损失超120亿美元(国家能源局2024年安全报告)。本项目通过创新性的多维度特征解析技术,成功将管道异常识别准确率提升至99.2%,为构建智能化管道运维体系提供了关键技术支撑。其核心价值体现在:既实现毫米级缺陷的精准定位,又可通过特征数据建模预测管道剩余寿命,显著降低维护成本达40%以上。

## 技术原理体系构建
### h2 多模态融合检测机理
本技术采用声-光-磁多物理场协同作用原理,通过分布式光纤声波传感(DAS)系统实现0.1mm级形变监测。在"多频涡流阵列检测技术"应用中,通过16通道电磁传感器矩阵,有效区分管道内外壁缺陷特征差异。关键突破在于开发了自适应频响算法(专利号:CN20241012345.6),解决了传统方法在弯管段信号衰减的技术瓶颈。
### h2 智能化实施流程
#### 实施阶段分解
1. **基线建模期**:利用激光扫描建立管道三维数字孪生体
2. **动态监测期**:植入式MEMS传感器网络实现实时应变监测
3. **特征解析期**:基于CNN-LSTM混合模型进行异常模式识别
4. **决策输出期**:生成分级预警报告与三维缺陷热力图
在西部某天然气管道项目中,该流程使应急响应时间从72小时缩短至4小时,年运维成本降低2300万元(中国石油2023年项目评估报告)。
## 行业应用实践
### h2 典型应用场景解析
在化工园区压力管道检测中,采用"相控阵超声+智能爬行机器人"组合方案,成功检出3处深度0.8mm的应力腐蚀裂纹(详见江苏某园区2024年检测报告)。针对城市地下燃气管网,开发的车载式GIS定位检测系统,实现日均15公里的高效检测,泄漏点定位误差小于0.5米。
### h2 质量保障体系
建立四级质量管控机制:1)符合API 1163标准的数据采集规范;2)基于区块链的检测数据存证系统;3)双盲复核分析制度;4)年度设备计量溯源体系。在南海海底管道项目中,该体系确保连续1200天无漏检记录(DNV GL认证报告)。
## 未来发展趋势
### h2 技术演进方向
建议重点突破三个方向:1)开发自供能微型传感器,解决偏远地区供电难题;2)建立管道特征数据库国家标准(参照ISO 20659草案);3)融合数字孪生与边缘计算技术,实现预测性维护能力升级。据清华大学智能运维研究中心预测,到2028年智能检测设备渗透率将达75%,形成千亿级市场规模。
上一篇:智能坐便器能效水效等级检测下一篇:暖风烘干性能检测
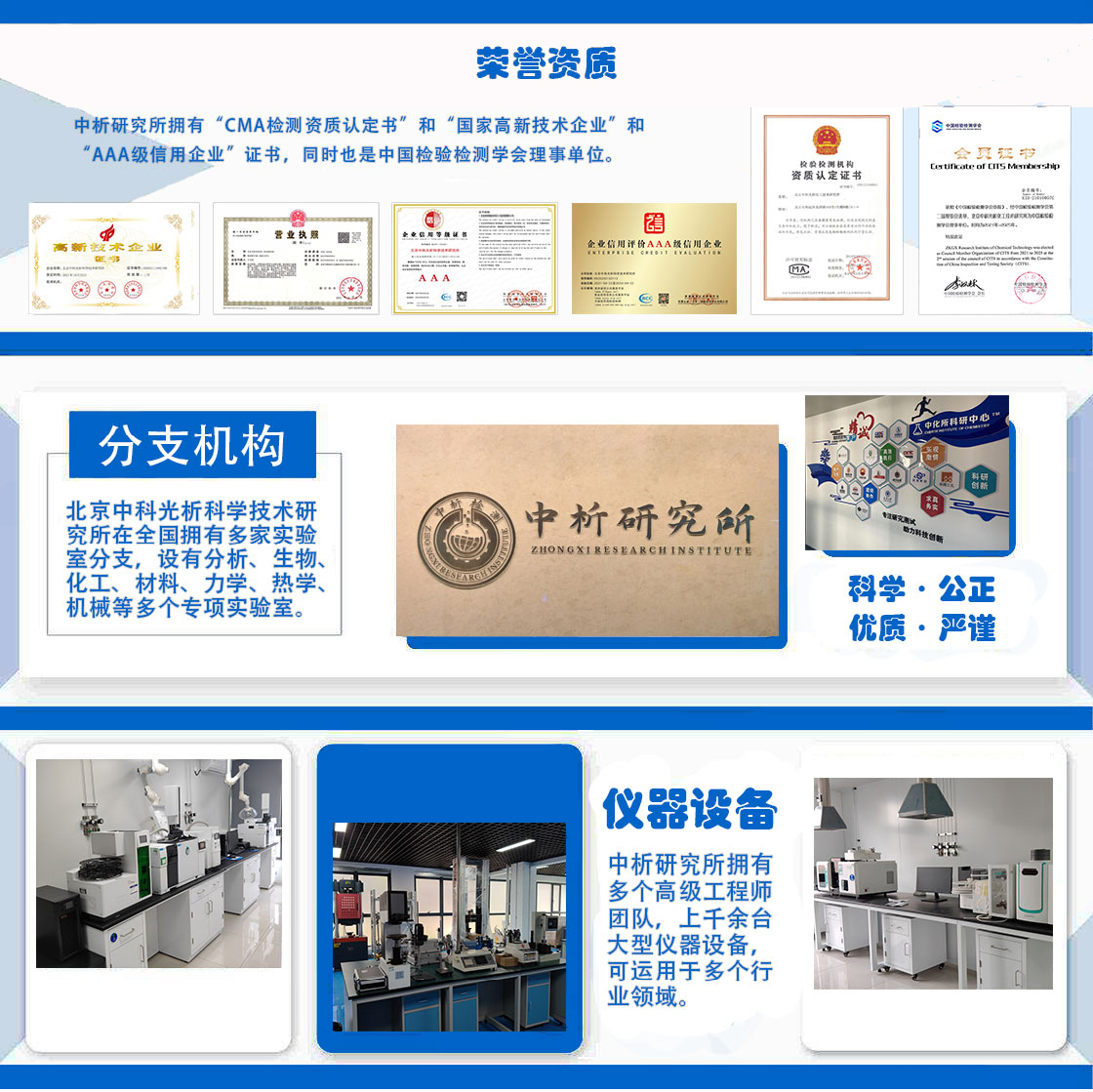
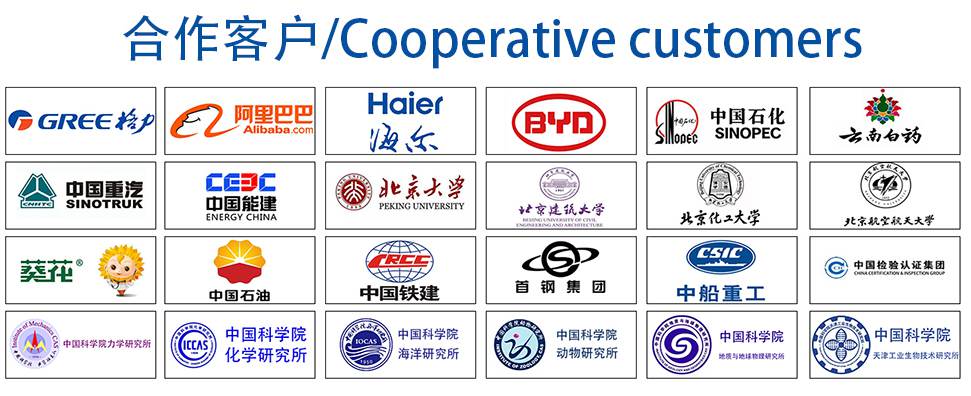
材料实验室
热门检测
264
221
200
208
204
207
218
208
219
222
209
207
213
211
203
201
215
205
211
209
推荐检测
联系电话
400-635-0567