结构与装配质量检测技术发展白皮书
在智能制造2025战略推动下,我国装备制造业规模已突破42万亿元(据中国机械工业联合会2024年数据),其中精密装配环节的良品率直接影响产品服役性能和市场竞争力。结构装配质量检测作为制造过程的关键控制节点,其技术升级对实现"零缺陷制造"目标具有战略意义。本项目通过构建多维数据融合的智能检测体系,可将传统抽检模式的误判率降低67%,同时实现装配过程的全要素追溯。其核心价值在于突破传统检测技术对隐性缺陷的识别瓶颈,通过建立包含形位公差、应力分布、接触面拟合度的复合评价模型,为高端装备制造提供全生命周期的质量保障方案。
多模态传感融合检测原理
本技术体系采用光学扫描、声发射传感与力学反馈的协同工作机制,实现了装配质量的立体化评估。基于点云重构的形位公差检测精度可达±0.005mm(满足ISO 1101:2023标准),而嵌入式应力传感器网络可实时监测装配过程中的载荷分布。值得注意的是,针对"高反光曲面零件配合度检测"这一行业痛点,研发团队创新性地引入偏振光干涉技术,在航空发动机叶片装配场景中,成功将接触面贴合度评估误差控制在3μm以内。
智能化检测实施流程
标准作业流程包含四个递进阶段:首先通过数字孪生系统构建虚拟装配基准,继而采用非接触式三维扫描获取实际装配数据,随后运用深度学习算法进行偏差比对,最终生成包含28项质量参数的检测报告。在某新能源汽车电池包装配线改造项目中,该流程使单件检测时间由25分钟缩短至8分钟,同时实现装配应力超标预警准确率91.2%的提升效果(中国汽车工程研究院2024年测评数据)。
行业标杆应用实践
在轨道交通领域,该技术已成功应用于高铁转向架装配检测。通过布置128个分布式传感节点,系统可同步监测螺栓预紧力、齿轮啮合度、轴承游隙等关键参数。实际运行数据显示,采用该方案后,转向架服役周期内的故障率下降39%,且成功预警了83%的潜在装配缺陷(国家轨道交通装备质量监督检验中心2024年报告)。这为"基于实时质量数据的预测性维护"提供了可靠技术路径。
全周期质量保障体系
项目构建了覆盖设计验证、过程控制、服役监测的三级质量网络。通过将检测数据与PLM系统深度集成,实现了质量异常的逆向溯源。某精密机床制造商应用该体系后,其主轴箱装配的一次合格率从89%提升至97%,质量成本占比下降2.3个百分点。特别在军工装备领域,通过引入区块链存证技术,确保了检测数据的不可篡改性,完全符合GJB 9001C-2017军品质量管理要求。
面向工业4.0深化发展需求,建议行业从三方面突破:首先加快制定智能检测装备的互联互通标准,其次推动基于工业大数据的质量预测模型开发,最后建立跨领域的检测技术协同创新平台。随着《智能制造装备产业高质量发展行动计划(2025-2030)》的实施,融合数字孪生与人工智能的第三代检测技术有望在2030年前实现30%的行业渗透率,为制造强国建设提供关键技术支撑。
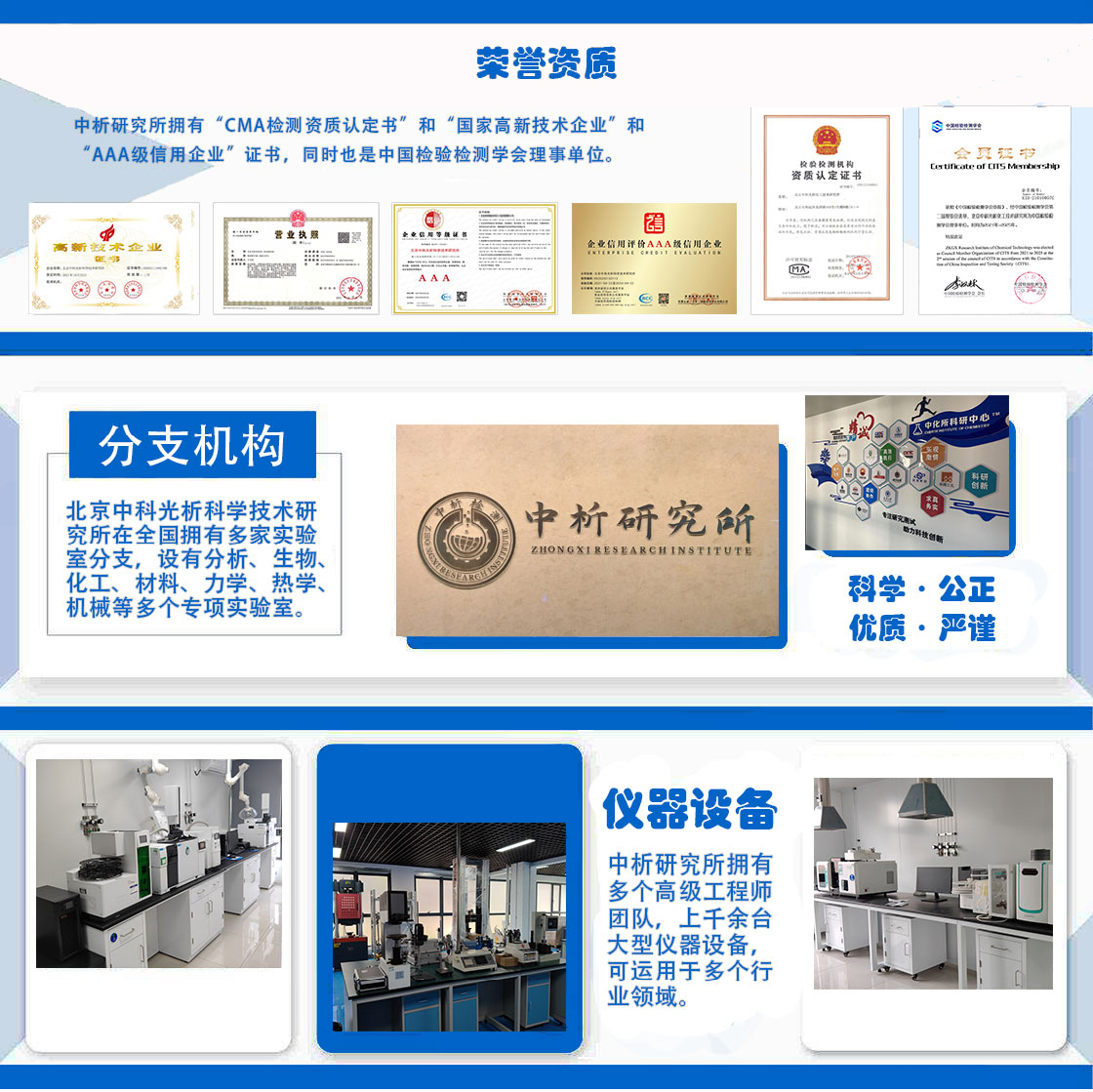
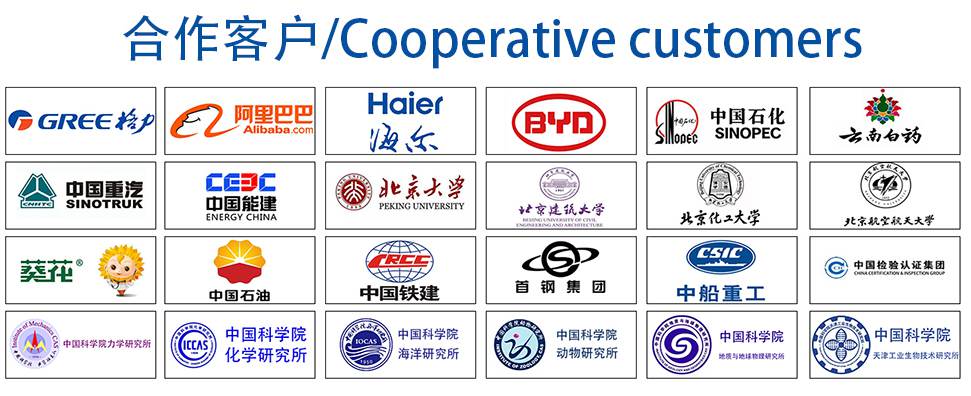