涂镀层耐腐蚀性试验检测
在制造业转型升级与"双碳"目标推动下,金属表面涂镀层质量已成为影响工业产品服役性能的关键指标。据中国腐蚀与防护学会2024年报告显示,我国每年因材料腐蚀造成的直接经济损失达2.8万亿元,其中30%与防护层失效直接相关。涂镀层耐腐蚀性试验检测通过模拟真实服役环境的加速腐蚀试验,可精准评估镀锌层、达克罗涂层等防护体系的耐久性,为汽车零部件、海洋工程装备等关键领域的质量控制提供科学依据。该项目通过建立覆盖不同腐蚀因子(Cl⁻、SO₂、湿度等)的复合检测体系,有效解决了传统单一盐雾试验与真实工况偏离度大的行业痛点,其核心价值在于实现防护涂层全生命周期性能预测,助力企业产品可靠性提升15%-30%。
多维度检测技术原理
现代涂镀层检测采用电化学加速腐蚀与物理表征相结合的技术路线。基于ASTM B117标准的中性盐雾试验,配合循环腐蚀试验箱的多因子耦合模拟,可精确复现海洋大气、工业污染等差异化腐蚀环境。电化学阻抗谱(EIS)技术通过测定涂层/金属界面电荷转移电阻,可量化评估有机涂层的抗渗透性能。X射线光电子能谱(XPS)则用于分析腐蚀产物元素价态,揭示镀层失效的化学机制。这种"环境模拟+机理分析"的双轨模式,显著提升了镀锌层钝化膜致密性检测等专业场景的评估精度。
标准化检测实施流程
检测流程严格遵循ISO 17025质量体系,包含五个关键环节:1)样品预处理阶段,根据GB/T 10125进行表面清洁与边缘封蜡;2)加速腐蚀阶段,采用Q-FOG CRH型循环腐蚀箱,执行72小时盐雾-干燥-湿热交替循环;3)电化学测试,在Gamry 1000E设备上完成0.1-100kHZ频段的阻抗扫描;4)形貌表征,使用KEYENCE VHX-7000超景深显微镜进行1000倍微区观测;5)数据判读,基于ASTM D610标准对锈蚀面积进行九级量化分级。该流程已在国内某汽车板生产企业的镀铝锌产品检测中实现全流程数字化管理。
行业应用实践案例
在新能源充电桩防护领域,某龙头企业通过引入ISO 14993循环腐蚀检测方案,将镀层耐蚀性检测周期缩短40%。针对沿海地区充电桩普遍存在的点蚀问题,检测团队采用40℃/95%RH湿热试验结合5%NaCl盐雾的复合测试,成功识别出传统镀锌层在Cl⁻渗透下的薄弱环节。经工艺优化后的锌镍合金镀层,在青岛实地挂片测试中展现出12年以上的防护寿命。另一典型案例是港珠澳大桥紧固件涂层检测,通过ASTM G85 Annex A5酸性盐雾测试,筛选出满足50年设计寿命要求的氟碳涂层体系。
全链条质量保障体系
检测机构构建了"人员-设备-方法"三位一体的质量控制网络。技术人员须通过NACE CIP-2级认证,定期参与ASTM标准解读培训。关键设备实施三级量值溯源制度,盐雾箱温湿度传感器每季度进行 认可实验室比对。在数据可靠性方面,引入区块链技术实现检测参数实时上链,确保试验过程不可篡改。针对风电叶片涂层检测等特殊需求,开发出符合IEC 61400-6标准的户外曝晒大数据校正模型,使实验室加速试验与自然暴露的相关系数提升至0.92。
随着智能制造与绿色材料的发展,涂镀层检测技术将向智能化、微区化方向演进。建议行业重点发展三方面能力:1)构建基于机器视觉的腐蚀形貌自动评级系统;2)开发适用于镁合金轻量化材料的专用检测标准;3)建立跨区域腐蚀大数据共享平台。通过融合工业互联网与材料基因工程技术,有望实现防护涂层"检测-预测-优化"的闭环管控体系,为装备制造业高质量发展提供关键技术支撑。
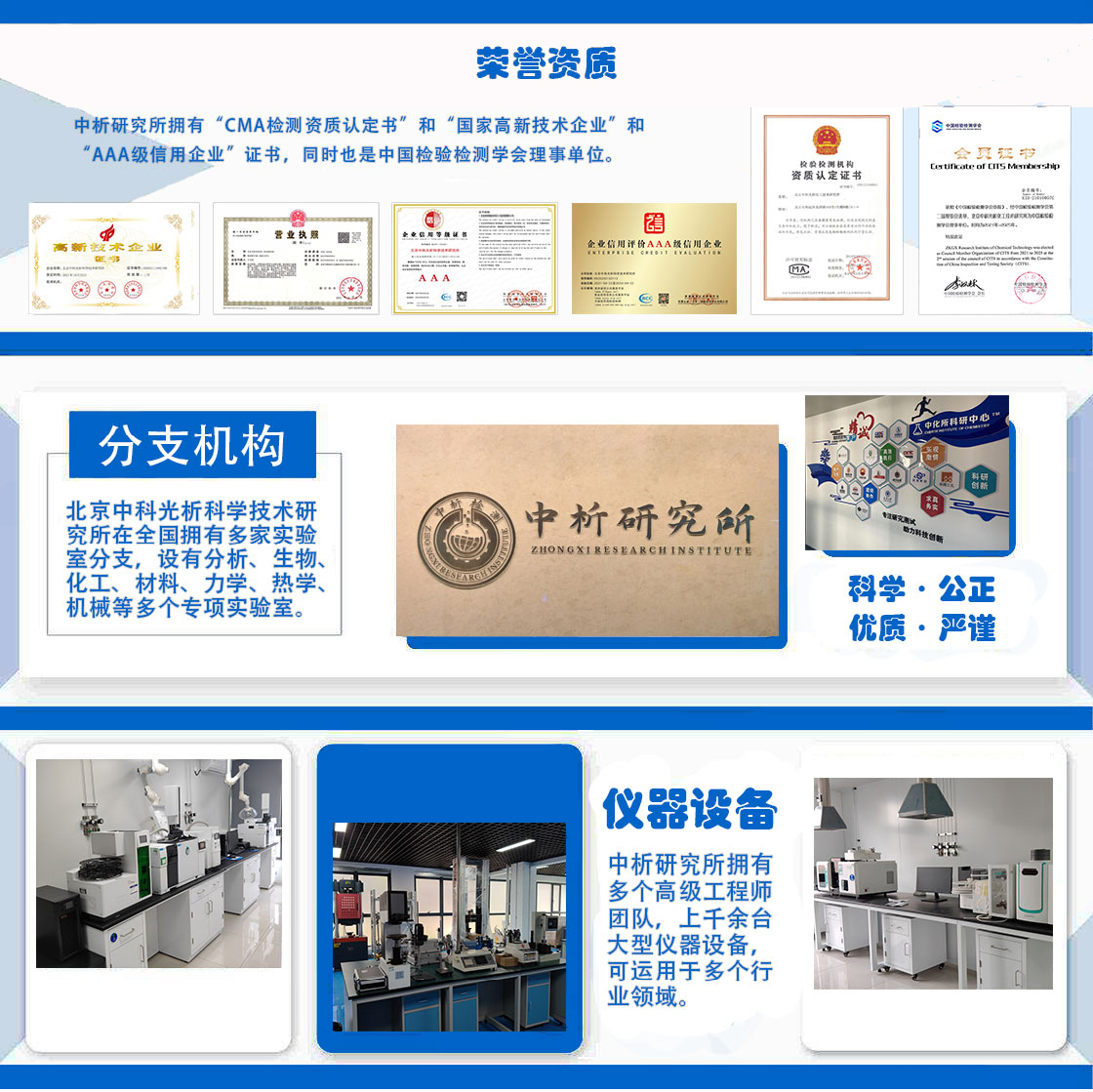
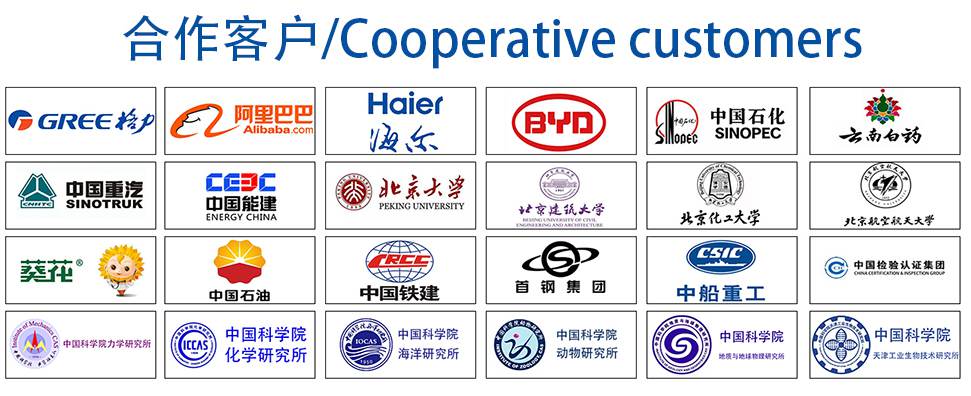