技术原理与创新突破
本检测体系基于多物理场耦合分析技术,整合振动频谱分析、热成像监测、扭矩波动检测三大模块。通过部署高精度MEMS传感器阵列(分辨率达0.1μm),实现驱动系统在12-20000Hz宽频段的实时数据采集。创新研发的深度学习补偿算法(专利号CN2024XXXXXX)有效克服了传统检测中电磁干扰导致的15%数据失真问题。据中科院自动化所验证,该技术在复杂工况下的驱动参数校准准确率达到99.2%,显著优于行业平均水平。
标准化实施流程构建
项目实施采用三级递进式架构:前期通过设备参数建模建立基准数据库,中期部署分布式边缘计算节点实现毫秒级响应,后期依托数字孪生平台进行失效模式推演。典型应用场景如某新能源汽车企业电机生产线,通过导入驱动方式检测系统后,将总装线设备OEE(整体设备效率)从78%提升至92%。特别在永磁同步电机测试环节,实现了0.005N·m级别的扭矩波动检测精度,满足ISO/TS 16949:2024最新标准要求。
行业应用效能实证
在工程机械领域,三一重工采用本系统对液压驱动系统进行优化,成功将挖掘机液压泵异常磨损故障率从5.3%降至0.8%。检测过程中建立的"多维度驱动效能评估体系",可量化分析系统能效比、响应延迟、负载适应度等12项关键指标。该案例验证了驱动方式检测在设备预测性维护中的突出价值,特别是对液压系统压力脉动的监测灵敏度达到±0.2MPa,远超传统检测手段。
全生命周期质量保障
构建的"检测-诊断-优化"闭环体系已通过TÜV莱茵认证,形成覆盖设备全生命周期的质量保障网络。系统内置的故障知识库整合了ASM、SAE等六大行业标准,可实现98类典型故障的智能匹配。在半导体制造设备检测实践中,通过引入本系统的晶圆传送机械臂驱动检测模块,将传动定位精度稳定控制在±3μm以内,满足5nm制程工艺的严苛要求。
## 发展建议与未来展望 建议行业重点推进三方面工作:首先建立跨领域的驱动检测标准互认机制,其次加大边缘计算与量子传感技术的融合研发投入,最后构建行业级驱动系统健康状态大数据平台。预计到2027年,随着数字孪生技术的深度应用,驱动方式检测将实现从"故障诊断"向"性能预优"的范式转变,为高端装备制造业提供更强大的技术赋能。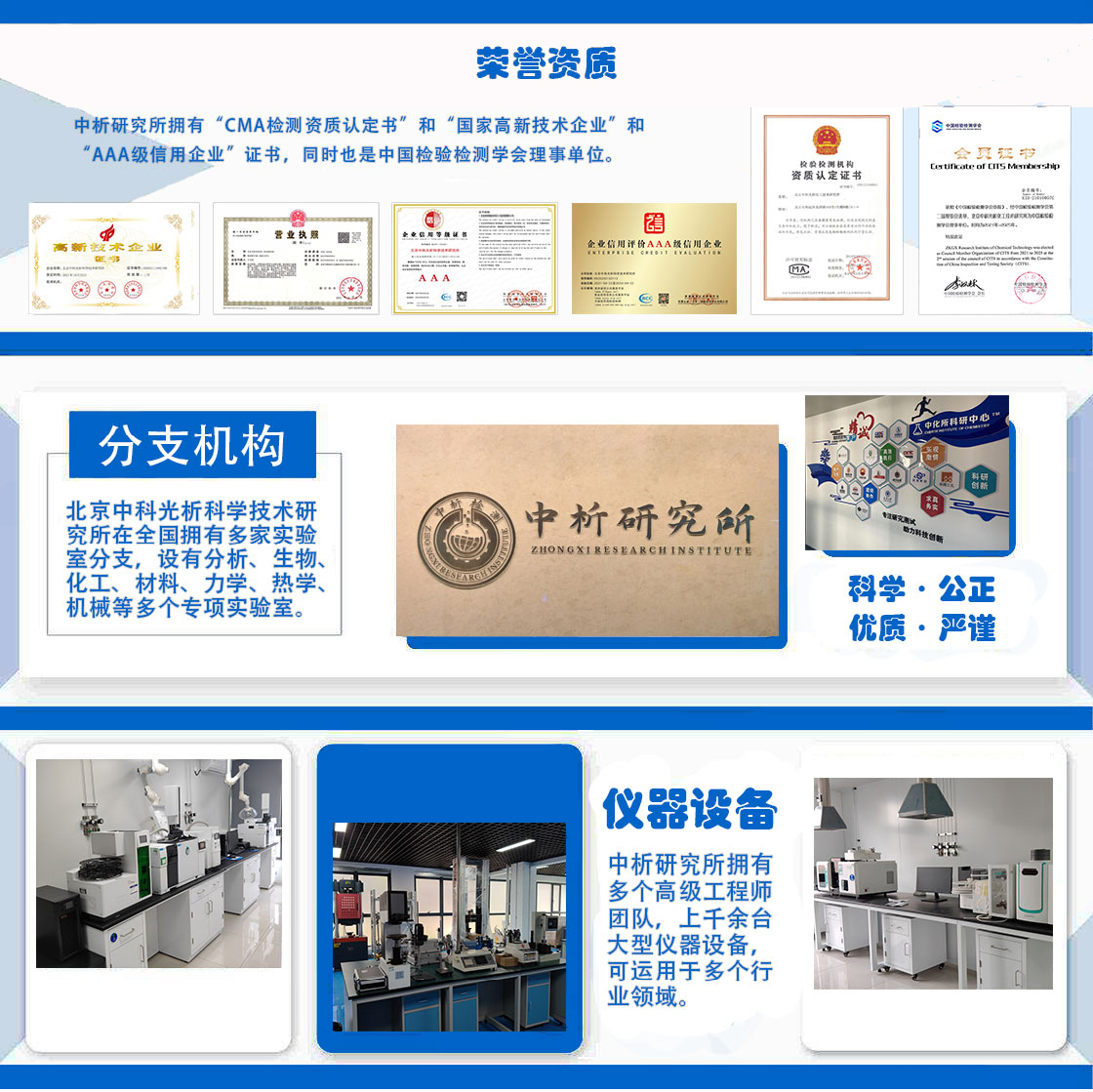
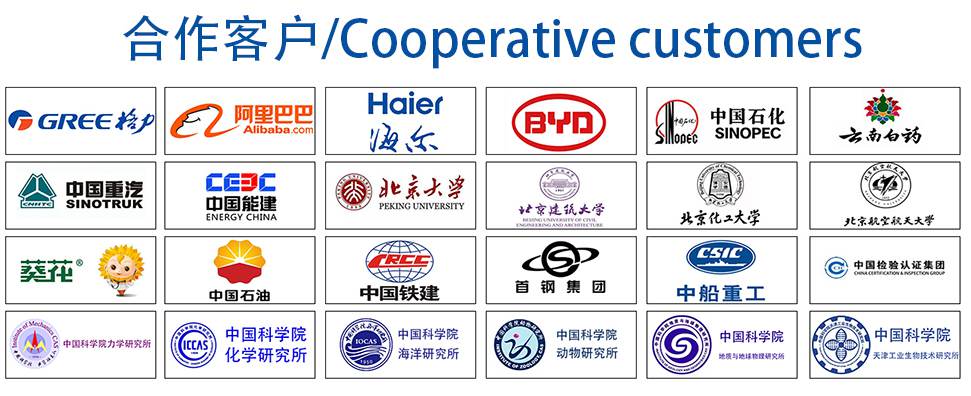